Quality management
Introduction
Quality management (QM) is a comprehensive and structured approach to organizational management that seeks to improve the quality of products and services through ongoing refinements in response to continuous feedback. QM requires the organization to focus on customers' needs and expectations, and to make the best use of its resources to achieve customer satisfaction.
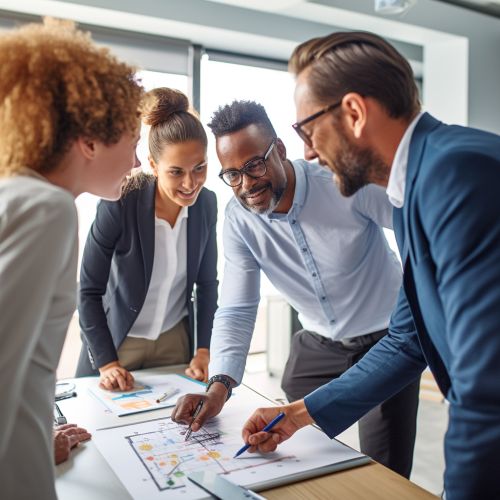

History of Quality Management
The concept of quality management was introduced during the industrial revolution when goods were made in bulk. Frederick W. Taylor, the father of scientific management, introduced quality control procedures to improve production efficiency. During the 1920s, Walter A. Shewhart proposed a theory of statistical control, forming the basis for the discipline of quality management.
Principles of Quality Management
Quality management is guided by a few fundamental principles. These include the involvement of people, the process approach, the system approach to management, continual improvement, factual approach to decision making, and mutually beneficial supplier relationships.
Involvement of People
People at all levels are the essence of an organization and their full involvement enables their abilities to be used for the organization's benefit.
Process Approach
A desired result is achieved more efficiently when activities and related resources are managed as a process.
System Approach to Management
Identifying, understanding and managing a system of interrelated processes for a given objective improves the organization's effectiveness and efficiency.
Continual Improvement
Continual improvement of the organization's overall performance should be a permanent objective of the organization.
Factual Approach to Decision Making
Effective decisions are based on the analysis of data and information.
Mutually Beneficial Supplier Relationships
An organization and its suppliers are interdependent, and a mutually beneficial relationship enhances the ability of both to create value.
Quality Management Systems
A quality management system (QMS) is a collection of business processes focused on achieving quality policy and quality objectives to meet customer requirements. It is expressed as the organizational structure, policies, procedures, processes and resources needed to implement quality management.
Quality Management Models
There are several models for implementing a quality management system, including ISO 9001, TQM, Six Sigma, and Lean.
ISO 9001
ISO 9001 is an international standard for quality management systems. The standard is based on a number of quality management principles including a strong customer focus, the involvement of top management, a process approach, and continual improvement.
Total Quality Management
Total Quality Management (TQM) is a management approach that originated in the 1950s and has steadily become more popular since the early 1980s. TQM includes a number of management practices, philosophies and methods to improve the quality of goods and services.
Six Sigma
Six Sigma is a disciplined, statistical-based, data-driven approach and continuous improvement methodology for eliminating defects in a product, process or service.
Lean Manufacturing
Lean manufacturing is a systematic method for waste minimization within a manufacturing system without sacrificing productivity.
Quality Management Tools
Quality management tools are the means to implement the quality management process. They include SPC, FMEA, DOE, and QFD.
Conclusion
Quality management is an essential part of any business. It helps to improve products and services, and to achieve customer satisfaction. The principles and tools of quality management provide a robust framework for improving organizational performance.