Total Quality Management
Introduction
Total Quality Management (TQM) is a management approach that originated in the 1950s and has steadily become more popular since the early 1980s. TQM means that the organization's culture is defined by and supports the constant attainment of customer satisfaction through an integrated system of tools, techniques, and training. This involves the continuous improvement of organizational processes, resulting in high-quality products and services.
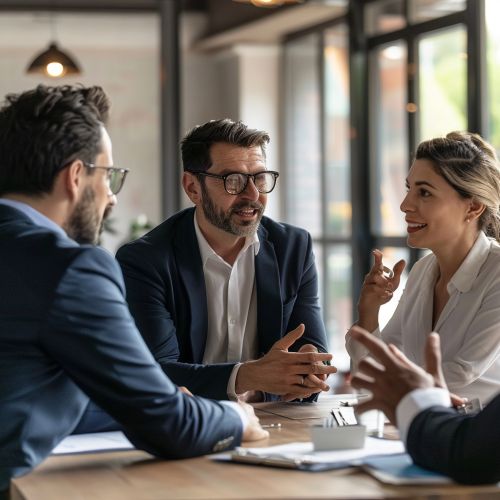
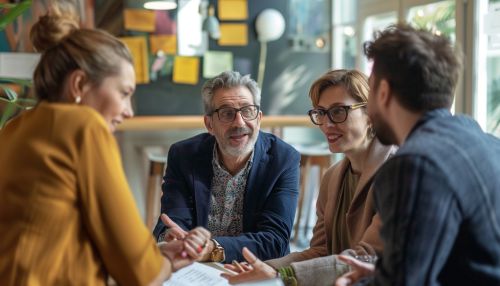
History and Evolution
The roots of TQM can be traced back to the teachings of experts such as Deming, Juran, and Feigenbaum, each of whom proposed a systematic approach for business management. The concept of quality control in business performance gained prominence during World War II, with an emphasis on improving the production process and exceeding customer expectations.
Principles of TQM
TQM principles are drawn from the beliefs of quality management pioneers. These principles include:
- Customer-focused: The customer ultimately determines the level of quality. No matter what an organization does to foster quality improvement—training employees, integrating quality into the design process, or upgrading computers or software—the customer determines whether the efforts were worthwhile.
- Total employee involvement: All employees participate in working toward common goals. Total employee commitment can only be obtained after fear has been driven from the workplace when empowerment has occurred, and when management has provided the proper environment.
- Process-centered: A fundamental part of TQM is a focus on process thinking. A process is a series of steps that take inputs from suppliers (internal or external) and transforms them into outputs that are delivered to customers (internal or external).
- Integrated system: Although an organization may consist of many different functional specialties often organized into vertically structured departments, it is the horizontal processes interconnecting these functions that are the focus of TQM.
Implementation of TQM
Implementing TQM may be a significant change for many organizations. It requires an understanding of the process, commitment from top management, training, and time. The implementation of TQM is considered a strategic decision and should be based on the needs of the organization rather than the adoption of a particular model proposed by a quality guru.
Benefits of TQM
When implemented correctly, TQM can provide numerous benefits to organizations. These include improved customer satisfaction, reduced costs due to fewer rework and waste, increased productivity, and improved employee morale.
Criticisms and Challenges
Despite its many benefits, TQM also faces criticism. Some argue that it is not a panacea for organizational woes and that it can be difficult to implement in organizations that have deeply entrenched cultures that do not support change. Moreover, TQM requires a long-term commitment, which may not be feasible for all organizations.