Quality Control
Introduction
Quality control (QC) is a process by which entities review the quality of all factors involved in production. This approach places an emphasis on three aspects: elements such as controls, job management, defined and well-managed processes, performance and integrity criteria, and identification of records. Quality management is focused not only on product and service quality, but also on the means to achieve it. Quality control emphasizes testing of products to uncover defects and reporting to management who make the decision to allow or deny product release, whereas quality assurance attempts to improve and stabilize production (and associated processes) to avoid, or at least minimize, issues which led to the defect(s) in the first place.
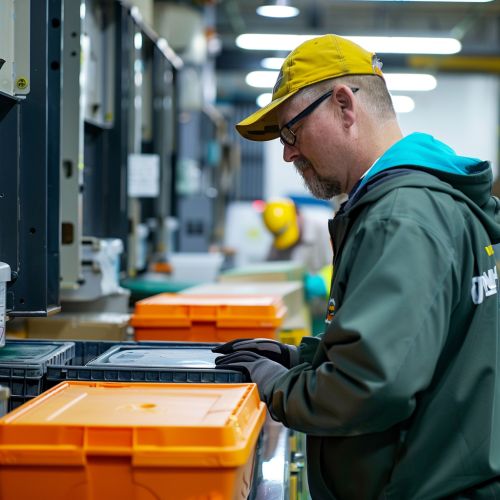
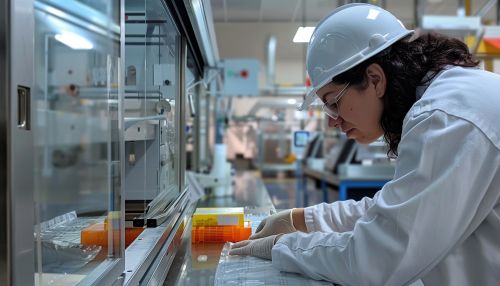
History
The concept of quality control in business and manufacturing has been around for over a hundred years. In the early 20th century, manufacturers began to include quality processes in quality practices. The idea of a quality control system was further developed during World War II, when high volumes of munitions had to be inspected for defects. This led to the development of statistical quality control (SQC), a theory that uses statistical methods to manage quality. The application of SQC to other types of business led to the development of the total quality control concept.
Principles of Quality Control
Quality control involves the examination of a product, service, or process for certain minimum levels of quality. The goal of a quality control team is to identify products or services that do not meet a company's specified standards of quality. If a problem is identified, the job of a quality control team or professional might involve stopping production or service until the problem has been corrected. Or it could be the team's responsibility to fix the problem itself.
Quality Control in Manufacturing
In manufacturing, quality control is a process that ensures customers receive products free from defects and meet their needs. When done the wrong way, it can put consumers at risk. For example, the recent defect found in Takata airbags resulted in the biggest automotive recall in history. The recall includes almost 69 million airbag inflators and may cost billions of dollars. The recall will last until the end of 2019 and take until 2020 to resolve.
Quality Control in Services
In terms of service, quality control is less tangible than in manufacturing. Service businesses have unique characteristics that often make it difficult to develop performance standards. The service sector of the economy is vast and includes a wide array of businesses ranging from web design to home repair.
Quality Control Techniques
Quality control techniques can be applied to any type of service or production process. These techniques can include statistical process control, acceptance sampling, process routing, and inspections. Each of these quality control techniques can be used in a variety of applications to help ensure that all products and services meet the highest standards.