Failure Mode and Effects Analysis
Introduction
Failure Mode and Effects Analysis (FMEA) is a systematic, proactive method for evaluating a process to identify where and how it might fail and to assess the relative impact of different failures, in order to identify the parts of the process that are most in need of change. FMEA includes review of the following:
- Steps in the process - Failure modes (What could go wrong?) - Failure causes (Why would the failure happen?) - Failure effects (What would be the consequences of each failure?)
History
The FMEA methodology was first developed by the U.S. military in the 1940s as a reliability evaluation technique. It was further developed and widely applied by the NASA and the automotive industry in the 1960s and 1970s.
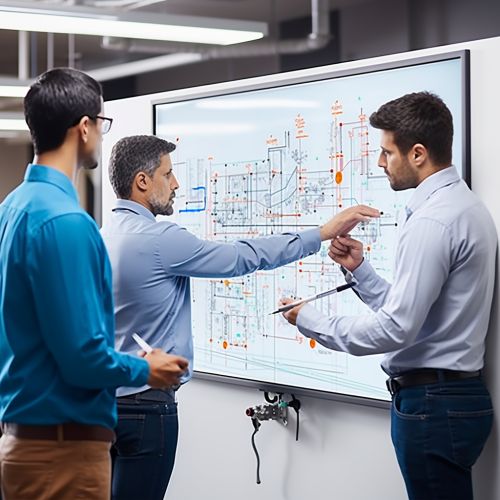
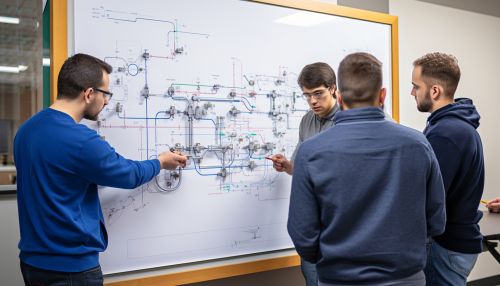
Methodology
The FMEA process begins by identifying all of the possible failure modes for the process or product. These are potential errors or defects that could affect the performance or function of the item. Each failure mode is then rated based on three criteria:
- Severity: The seriousness of the effect of the failure - Occurrence: The likelihood that the failure will occur - Detection: The likelihood that the failure will be detected before it affects the customer
These three ratings are then multiplied together to calculate a Risk Priority Number (RPN) for each failure mode. The failure modes with the highest RPNs are considered the most critical and are prioritized for improvement.
Types of FMEA
There are several types of FMEA, each designed for a specific purpose:
- Design FMEA (DFMEA): This type of FMEA is used to analyze products before they are released to identify any potential design-related failure modes. - Process FMEA (PFMEA): This type of FMEA is used to analyze manufacturing and assembly processes. - System FMEA (SFMEA): This type of FMEA is used to analyze systems and subsystems in the early concept stages to prevent system failures. - Service FMEA (SFMEA): This type of FMEA is used to analyze services and identify potential service-related failure modes.
Benefits of FMEA
The main benefits of FMEA include:
- Improved quality and reliability of products or processes - Increased customer satisfaction due to fewer failures and complaints - Reduced costs due to fewer recalls and warranty claims - Improved company reputation due to higher quality products or services
Limitations of FMEA
Despite its benefits, FMEA also has some limitations:
- It is a time-consuming process that requires a significant amount of resources. - The effectiveness of FMEA depends on the knowledge and expertise of the team conducting the analysis. - FMEA is a qualitative method and its results can be subjective. - FMEA does not consider multiple failures or combinations of failures.
Conclusion
FMEA is a powerful tool for identifying potential failures and their impacts on a process or product. By systematically evaluating each step of a process, FMEA can help organizations prioritize improvements and reduce the risk of failures. Despite its limitations, FMEA is widely used in many industries due to its effectiveness in improving quality and reliability.
See Also
- Risk Management - Quality Control - Reliability Engineering