Lean Manufacturing
Introduction
Lean manufacturing or lean production, often simply "lean", is a systematic method for waste minimization ("Muda") within a manufacturing system without sacrificing productivity. Lean also takes into account waste created through overburden ("Muri") and waste created through unevenness in workloads ("Mura"). Lean manufacturing is derived from the Toyota Production System (TPS) and its key thrust is to increase the value-added work by eliminating waste and reducing incidental work.
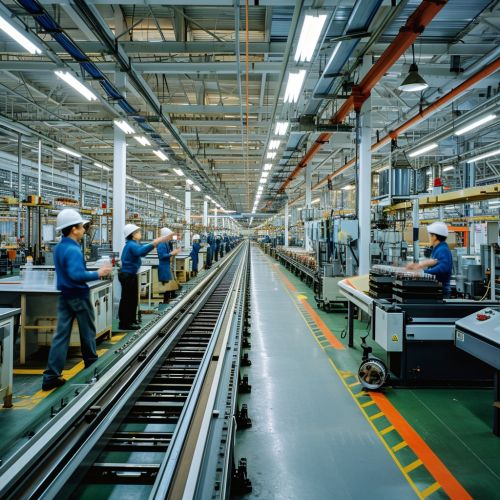
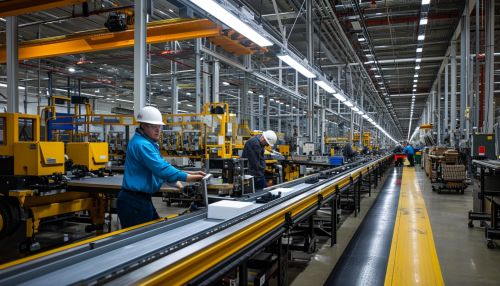
History
The concept of lean manufacturing was developed for maximizing the resource utilization through minimization of waste, later it was proven that lean methodology is applicable to every aspect of business, not just manufacturing. Now, it is being used as a business performance improvement tool all over the world.
Principles
Lean manufacturing is based on a number of key principles and concepts. These include:
Value
In lean manufacturing, the concept of value is defined from the customer's perspective. This is often referred to as 'customer value'. The goal is to create processes that provide value to the customer and eliminate those that do not.
Value Stream
The value stream in lean manufacturing refers to the series of activities that create and build value in the final product from raw material extraction to the end customer. In lean manufacturing, waste is eliminated from the value stream.
Flow
In lean manufacturing, the goal is to create a 'flow' of value to the customer through the value stream. This involves the elimination of waste and the continual improvement of processes.
Pull
In a lean manufacturing system, production is 'pulled' from customer demand rather than being 'pushed' from production schedules. This helps to reduce overproduction and inventory, and improve responsiveness to customer demand.
Perfection
Lean manufacturing is a continuous improvement process where the goal is to achieve perfection. This involves the constant elimination of waste and the continual improvement of processes.
Tools and Techniques
There are many tools and techniques used in lean manufacturing to help achieve these principles. These include:
5S
5S is a workplace organization method that uses a list of five Japanese words: seiri, seiton, seiso, seiketsu, and shitsuke. These have been translated as Sort, Set in order, Shine, Standardize, and Sustain.
Kanban
Kanban is a scheduling system for lean manufacturing and just-in-time manufacturing. It is an inventory-control system to control the supply chain.
Poka-yoke
Poka-yoke is a Japanese term that means "mistake-proofing". It is any mechanism in a lean manufacturing process that helps an equipment operator avoid mistakes.
Just In Time (JIT)
Just In Time (JIT) is an inventory strategy companies employ to increase efficiency and decrease waste by receiving goods only as they are needed in the production process, thereby reducing inventory costs.
Total Productive Maintenance (TPM)
Total Productive Maintenance (TPM) is a system of maintaining and improving the integrity of production and quality systems through the machines, equipment, processes, and employees that add business value to an organization.
Benefits of Lean Manufacturing
Lean manufacturing provides significant benefits to companies that properly implement its principles. These benefits include:
- Reduction in manufacturing cost - Improvement in product quality - Reduction in lead time - Reduction in total cycle time - Improved delivery performance - Increased customer satisfaction
Challenges in Implementing Lean Manufacturing
Implementing lean manufacturing is not without its challenges. These can include:
- Resistance to change - Lack of understanding of lean principles - Difficulty in changing old habits and ways of thinking - The need for ongoing training and education
Conclusion
Lean manufacturing is a powerful tool for improving efficiency, reducing waste, and increasing productivity. However, it requires a commitment to continuous improvement, a willingness to change, and a focus on customer value to be successful.
See Also
- Six Sigma - Total Quality Management - Theory of Constraints