The Physics of Thin Film Deposition Techniques
Introduction
Thin film deposition is a process used in physics, materials science, and engineering to create layers of material that can be as thin as a single atom. These films can be used in a variety of applications, from semiconductor devices to optical coatings. There are several techniques used to deposit thin films, each with its own advantages and disadvantages.
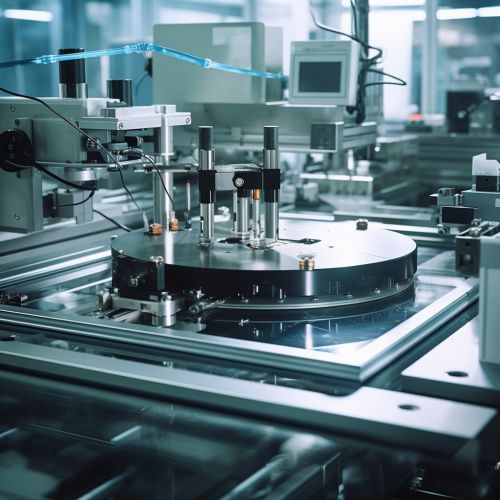
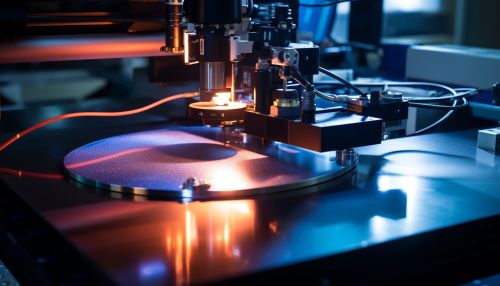
Physical Vapor Deposition (PVD)
Physical Vapor Deposition (PVD) is a category of thin film deposition techniques that involve the evaporation or sputtering of a material, followed by its recondensation onto a substrate. This process can occur in a vacuum or at low pressure, and the resulting film can be pure or a composite of multiple materials.
Evaporation
Evaporation is a PVD technique in which a material is heated until it evaporates, and the vapor is then condensed onto a substrate. This can be done in a vacuum to reduce contamination and improve the quality of the film. There are several methods of evaporation, including resistive evaporation, electron beam evaporation, and flash evaporation.
Resistive Evaporation
In resistive evaporation, a resistive heating element is used to heat the material until it evaporates. The material is usually placed in a crucible or boat made of a material that can withstand high temperatures, such as tungsten or molybdenum.
Electron Beam Evaporation
Electron beam evaporation uses a focused beam of electrons to heat the material. This method can achieve higher temperatures than resistive evaporation, allowing for the evaporation of materials with high melting points.
Flash Evaporation
Flash evaporation involves rapidly heating a small amount of material until it evaporates. This can be done using a variety of methods, including laser ablation or electrical discharge.
Sputtering
Sputtering is another PVD technique in which atoms are ejected from a target material and then deposited onto a substrate. This is typically done by bombarding the target with ions in a vacuum. There are several types of sputtering, including diode sputtering, magnetron sputtering, and reactive sputtering.
Diode Sputtering
In diode sputtering, a voltage is applied between the target and the substrate, creating a plasma. The ions in the plasma are accelerated towards the target, causing atoms to be ejected and deposited onto the substrate.
Magnetron Sputtering
Magnetron sputtering uses a magnetic field to confine the plasma to the area around the target. This increases the efficiency of the sputtering process and allows for the deposition of thicker films.
Reactive Sputtering
In reactive sputtering, a reactive gas is introduced into the vacuum chamber. The gas reacts with the target material, forming a compound that is then sputtered onto the substrate.
Chemical Vapor Deposition (CVD)
Chemical Vapor Deposition (CVD) is a category of thin film deposition techniques that involve the chemical reaction of gaseous precursors on a heated substrate. The resulting product is a solid material that forms a thin film on the substrate. There are several types of CVD, including atmospheric pressure CVD, low-pressure CVD, and plasma-enhanced CVD.
Atmospheric Pressure CVD
In atmospheric pressure CVD, the chemical reaction takes place at atmospheric pressure. This method is often used for the deposition of oxide films.
Low-Pressure CVD
Low-pressure CVD is similar to atmospheric pressure CVD, but the reaction takes place at a lower pressure. This can improve the uniformity of the film and reduce the risk of contamination.
Plasma-Enhanced CVD
Plasma-enhanced CVD uses a plasma to enhance the chemical reaction. This allows for the deposition of films at lower temperatures, which can be beneficial for temperature-sensitive substrates.
Conclusion
Thin film deposition techniques are a crucial part of many areas of physics, materials science, and engineering. The choice of technique depends on the specific requirements of the application, including the desired properties of the film, the type of substrate, and the available resources. By understanding the principles and advantages of each technique, scientists and engineers can make informed decisions about the best method for their needs.