Magnetron Sputtering
Introduction
Magnetron sputtering is a widely used physical vapor deposition (PVD) technique for thin film deposition. It involves the ejection of material from a target by bombarding it with energetic ions, typically from a plasma, and subsequently depositing the ejected material onto a substrate. This method is highly valued for its ability to produce high-quality, uniform coatings with excellent adhesion and control over film thickness and composition.
Principles of Magnetron Sputtering
Magnetron sputtering operates on the principle of sputtering, where atoms are ejected from a solid target material due to bombardment by energetic ions. The ions are typically generated in a plasma, which is sustained by applying a high voltage between the target (cathode) and the substrate (anode). The presence of a magnetic field near the target enhances the efficiency of the sputtering process by trapping electrons close to the target surface, thus increasing the ionization rate of the plasma.
Plasma Generation
In magnetron sputtering, a plasma is generated by applying a high voltage between the target and the substrate in a low-pressure gas environment, usually argon. The electric field accelerates electrons, which collide with gas atoms, ionizing them and creating a plasma. The ions in the plasma are then accelerated towards the negatively biased target, causing sputtering of the target material.
Magnetic Field Configuration
The magnetic field in magnetron sputtering is typically created using permanent magnets or electromagnets positioned behind the target. The magnetic field lines are arranged in such a way that they form closed loops parallel to the target surface. This configuration traps electrons in the vicinity of the target, increasing the ionization efficiency and the density of the plasma near the target surface.
Types of Magnetron Sputtering
Magnetron sputtering can be classified into several types based on the configuration of the magnetic field and the mode of operation. The most common types include:
Direct Current (DC) Magnetron Sputtering
DC magnetron sputtering is used for conducting target materials. A constant DC voltage is applied between the target and the substrate, creating a steady-state plasma. This method is simple and cost-effective but is limited to conductive materials.
Radio Frequency (RF) Magnetron Sputtering
RF magnetron sputtering is used for both conducting and insulating target materials. An alternating RF voltage is applied, typically at 13.56 MHz, which allows for the sputtering of insulating materials by preventing charge buildup on the target surface. This method is more versatile but also more complex and expensive than DC magnetron sputtering.
Pulsed DC Magnetron Sputtering
Pulsed DC magnetron sputtering is a variation of DC sputtering where the applied voltage is pulsed at a low frequency, typically in the range of 10-100 kHz. This technique helps to reduce arcing and improve the quality of the deposited films, especially for reactive sputtering processes.
High Power Impulse Magnetron Sputtering (HiPIMS)
HiPIMS is a recent advancement in magnetron sputtering where very high power pulses are applied to the target for short durations, typically in the microsecond range. This results in a high ionization rate of the sputtered material, leading to dense and smooth films with excellent adhesion properties.
Applications of Magnetron Sputtering
Magnetron sputtering is used in a wide range of applications due to its versatility and ability to produce high-quality coatings. Some of the key applications include:
Semiconductor Industry
In the semiconductor industry, magnetron sputtering is used for the deposition of thin films in the fabrication of integrated circuits (ICs) and other electronic devices. It is used to deposit various materials, including metals, dielectrics, and semiconductors, with precise control over film thickness and composition.
Optical Coatings
Magnetron sputtering is widely used for the deposition of optical coatings, such as anti-reflective coatings, mirrors, and filters. The ability to deposit uniform and high-quality films with precise control over optical properties makes it an ideal technique for these applications.
Hard and Wear-Resistant Coatings
Magnetron sputtering is used to deposit hard and wear-resistant coatings on tools, cutting instruments, and mechanical components. These coatings, such as titanium nitride (TiN) and diamond-like carbon (DLC), enhance the durability and performance of the coated surfaces.
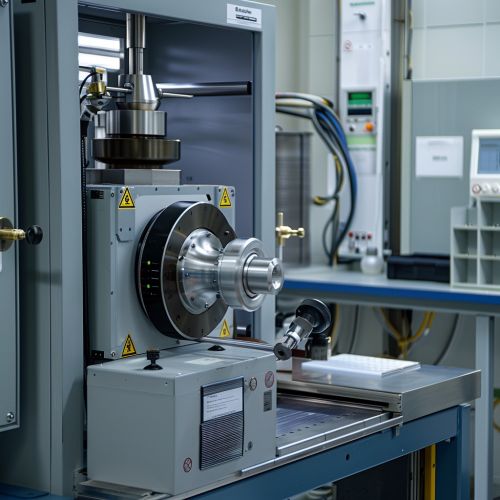
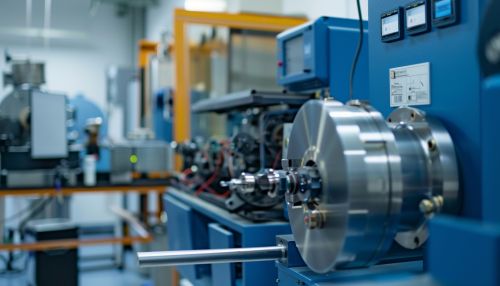
Decorative Coatings
Magnetron sputtering is also used for decorative coatings on consumer products, such as watches, jewelry, and automotive parts. These coatings provide aesthetic appeal and can also offer additional protection against wear and corrosion.
Advantages and Limitations
Magnetron sputtering offers several advantages over other thin film deposition techniques, but it also has some limitations.
Advantages
- **High Film Quality**: Magnetron sputtering produces films with excellent adhesion, uniformity, and control over thickness and composition.
- **Versatility**: It can be used to deposit a wide range of materials, including metals, alloys, ceramics, and polymers.
- **Scalability**: Magnetron sputtering can be easily scaled up for large-area deposition, making it suitable for industrial applications.
- **Low Substrate Temperature**: The substrate temperature during deposition is relatively low, which is beneficial for temperature-sensitive substrates.
Limitations
- **Complexity and Cost**: The equipment and process control for magnetron sputtering can be complex and expensive, especially for advanced techniques like RF and HiPIMS.
- **Target Poisoning**: In reactive sputtering processes, the target can become poisoned by the reactive gas, leading to process instability and reduced deposition rates.
- **Limited Step Coverage**: Magnetron sputtering may have limited step coverage for high aspect ratio features, which can be a limitation for certain applications.
Future Trends and Developments
The field of magnetron sputtering is continuously evolving, with ongoing research and development aimed at improving the performance and expanding the applications of this technique. Some of the future trends and developments include:
Advanced Power Supplies
The development of advanced power supplies, such as pulsed DC and HiPIMS, is enabling better control over the sputtering process and the properties of the deposited films. These advancements are expected to lead to further improvements in film quality and deposition efficiency.
Reactive Sputtering
Reactive sputtering, where a reactive gas is introduced into the sputtering chamber to form compound films, is an area of active research. Advances in process control and understanding of the reactive sputtering mechanisms are expected to enhance the stability and performance of this technique.
In-Situ Monitoring and Control
The integration of in-situ monitoring and control techniques, such as optical emission spectroscopy (OES) and quartz crystal microbalance (QCM), is improving the precision and reproducibility of magnetron sputtering processes. These advancements are enabling better control over film properties and process optimization.
Novel Materials and Applications
The exploration of novel materials and applications for magnetron sputtering is an ongoing trend. This includes the deposition of complex multi-layer structures, nanocomposite films, and functional coatings for emerging technologies such as flexible electronics, energy storage, and biomedical devices.
See Also
- Physical Vapor Deposition
- Thin Film Deposition
- Plasma Physics
- High Power Impulse Magnetron Sputtering
- Reactive Sputtering