Chemical Vapor Deposition
Introduction
Chemical Vapor Deposition (CVD) is a widely used materials science technique for the production of high-quality, high-performance, solid materials, typically on a substrate. The process is often used in the semiconductor industry to produce thin films. In a typical CVD process, the substrate is exposed to one or more volatile precursors, which react or decompose on the substrate surface to produce the desired deposit.
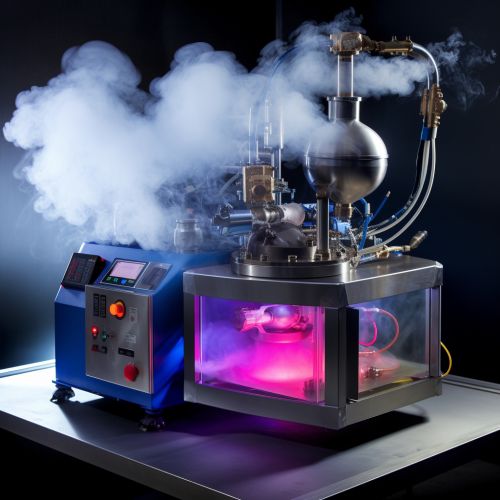
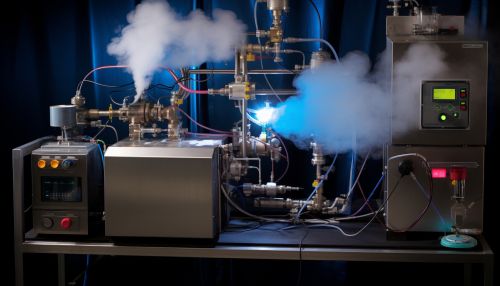
Process Types
There are several types of CVD, categorized by the physical and chemical characteristics of the process. These include:
- Atmospheric Pressure CVD (APCVD) - CVD processes that take place at pressure of about 1 atmosphere.
- Low Pressure CVD (LPCVD) - CVD processes that take place at significantly lower pressures. Reduces unwanted gas-phase reactions and improves film uniformity across the wafer.
- Ultrahigh Vacuum CVD (UHVCVD) - CVD processes that take place at very low pressure, typically below 10−6 Pa (~10−8 torr). Higher quality films at lower deposition rates.
- Plasma Enhanced CVD (PECVD) - CVD processes that utilize a plasma to enhance chemical reaction rates at the substrate surface.
Process Steps
The CVD process consists of several steps that can be adjusted to optimize the deposition of the desired material. These steps include:
- Gas Delivery - The precursor gases are introduced into the CVD chamber.
- Activation - The gases are activated by being heated or subjected to a plasma. This breaks the gas molecules into reactive species that can then react at the substrate surface.
- Reaction - The reactive species adsorb onto the substrate surface and react to form the desired material.
- Desorption - Byproducts of the reaction desorb from the surface and are removed from the CVD chamber.
Materials
A wide range of materials can be deposited using CVD. These include:
- Insulators - Such as silicon dioxide (SiO2), silicon nitride (Si3N4), and silicon oxynitride (SiON).
- Semiconductors - Such as silicon (Si), germanium (Ge), and various forms of carbon including diamond and graphene.
- Metals - Such as tungsten (W), copper (Cu), and nickel (Ni).
Applications
CVD is used in a wide range of applications. These include:
- Semiconductor Industry - CVD is used extensively in the fabrication of integrated circuits. Films are deposited to create layers of material with different properties.
- Solar Cells - CVD is used to deposit thin film solar cells. These are typically made from silicon, but can also be made from other semiconductors.
- Protective Coatings - CVD is used to deposit hard, wear-resistant coatings on tools and components.
- Optical Fibers - CVD is used to deposit the core and cladding materials in the manufacture of optical fibers.
Advantages and Disadvantages
Like any process, CVD has its advantages and disadvantages. Some of the advantages of CVD include:
- Quality - CVD can produce high quality, high purity materials.
- Uniformity - CVD can produce films with very uniform thickness.
- Conformality - CVD can deposit films on complex shapes, providing excellent step coverage.
Some of the disadvantages of CVD include:
- Cost - CVD equipment can be expensive and the process can be costly due to the high temperatures and vacuum conditions required.
- Safety - The precursor gases used in CVD can be toxic, flammable, or both.
- Environmental Impact - The byproducts of CVD can be hazardous and require proper disposal.