Fibre Reinforced Polymer
Introduction
Fibre Reinforced Polymer (FRP), also known as Fiber-Reinforced Plastic, is a composite material made of a polymer matrix reinforced with fibres. The fibres are usually glass, carbon, aramid, or basalt. Rarely, other fibres such as paper, wood, or asbestos have been used. The polymer is usually an epoxy, vinyl ester, or polyester thermosetting plastic, and is sometimes phenol formaldehyde resins. FRPs are commonly used in the aerospace, automotive, marine, and construction industries.

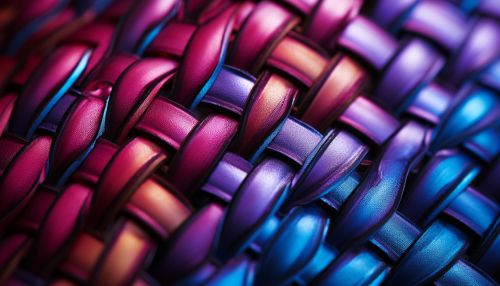
Composition
The primary function of the fibre reinforcement in an FRP composite is to carry load along the length of the fibre and to provide strength and stiffness in one direction. FRP composites typically contain more than one type of fibre, such as glass, carbon, aramid, and basalt. The choice of fibres depends on the desired properties. For example, carbon fibres and aramid fibres provide high stiffness, tensile strength, and temperature resistance, while glass fibres and basalt fibres provide high strength, flexibility, and impact resistance.
The polymer matrix in an FRP composite provides the shape and protects the fibres from damage, holding the fibres together and transferring load between them. The matrix is usually a thermosetting resin such as epoxy, vinyl ester, or polyester, but can also be a thermoplastic or other type of resin.
Manufacturing Process
The manufacturing process of FRP composites involves several steps. First, the fibres are woven, knitted, or braided together to form a preform. This preform is then combined with the resin to form a raw composite. The composite is then cured under heat and pressure to form the final product. The curing process causes the resin to polymerize and harden, binding the fibres together and giving the composite its shape and strength.
The manufacturing process can be manual or automated, and varies depending on the type of fibre, matrix, and final product. Common manufacturing methods include hand lay-up, spray-up, resin transfer molding, pultrusion, filament winding, and compression molding.
Properties
FRP composites have many desirable properties that make them suitable for a wide range of applications. These properties include high strength-to-weight ratio, high stiffness-to-weight ratio, good durability, good corrosion resistance, good thermal insulation, and good electrical insulation. The properties of an FRP composite can be tailored by adjusting the type, amount, and orientation of the fibres, and by choosing the appropriate matrix.
Applications
FRP composites are used in a wide range of industries due to their versatile properties. In the aerospace industry, they are used in the manufacture of aircraft structures and components, such as wings, fuselages, and propellers. In the automotive industry, they are used in the manufacture of car bodies, bumpers, and engine components. In the marine industry, they are used in the manufacture of boat hulls, masts, and sails. In the construction industry, they are used in the manufacture of building materials, such as panels, beams, and columns.
Advantages and Disadvantages
FRP composites have several advantages over traditional materials. They are lightweight, strong, and durable, which makes them ideal for applications where weight savings and durability are important. They are also resistant to corrosion, which makes them suitable for use in harsh environments. However, FRP composites also have some disadvantages. They are relatively expensive compared to traditional materials, and their manufacture requires specialized equipment and skills. They are also susceptible to damage from impact and abrasion, and their properties can degrade over time due to exposure to sunlight and moisture.
Future Trends
The use of FRP composites is expected to grow in the future, driven by increasing demand from the aerospace, automotive, and construction industries. Advances in manufacturing technology, such as automated fibre placement and additive manufacturing, are expected to reduce the cost and increase the production speed of FRP composites. Advances in material science, such as the development of new types of fibres and resins, are expected to improve the properties of FRP composites.