Filament Winding
Introduction
Filament winding is a fabrication technique primarily used for manufacturing open (cylinders) or closed end structures (pressure vessels or tanks). This process involves winding filaments under tension over a rotating mandrelmandrel. The mandrel rotates around a spindle while a delivery eye on a carriage moves horizontally, laying down fibers in the desired pattern. The most common filaments are carbon or glass fibers impregnated with a thermosetting resin; however, other fibers and resins can be used. The development of the filament winding process has been stimulated by the increasing demand for high performance, lightweight, and cost-effective materials in various industries such as aerospace, automotive, and oil and gas.
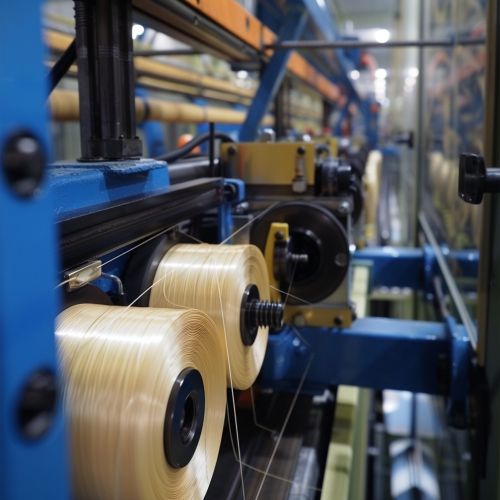
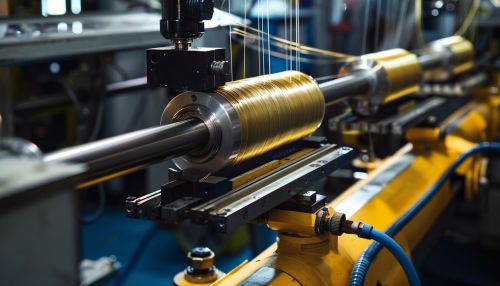
Process
The filament winding process begins with the filament impregnation. The filaments, typically in the form of a roving, are coated with a resin matrix to form what is known as a prepreg. The resin matrix, which can be a thermoset or thermoplastic polymer, binds the structural fibers together, provides the composite material with its shape, and protects the fibers from environmental and load-induced damage.
The impregnated fibers are then wound onto a rotating mandrel in a predetermined pattern. The winding pattern can be helical, polar, or hoop, and the choice of pattern depends on the desired properties of the final product. The mandrel shape and size determine the shape and size of the final product. The mandrel is typically made of steel and coated with a release agent to facilitate the removal of the wound part after curing.
Once the winding is complete, the wound part is cured. Curing involves the application of heat and/or pressure to initiate the polymerization of the resin matrix. The curing process transforms the resin matrix from a liquid or semi-solid state into a solid state, thereby hardening the composite material and locking the fibers in place. After curing, the wound part is removed from the mandrel to yield the final product.
Advantages and Disadvantages
Filament winding has several advantages over other composite manufacturing processes. It is a highly automated process that can produce parts with complex shapes and large sizes. The high degree of automation reduces labor costs and increases production speed. The process can be easily controlled and monitored to ensure product quality and consistency. Filament winding also allows for a high degree of design flexibility, as the winding pattern, fiber orientation, and resin content can be easily adjusted to meet specific performance requirements.
However, filament winding also has some disadvantages. The process is limited to parts with rotational symmetry. The quality of the wound part is highly dependent on the winding tension, which must be carefully controlled to avoid fiber slippage or breakage. The process also requires a significant amount of energy for curing, especially for thermoset resins. Furthermore, the removal of the wound part from the mandrel can be challenging, particularly for parts with complex shapes or large sizes.
Applications
Filament winding is used in a wide range of industries due to its versatility and efficiency. In the aerospace industry, it is used to manufacture rocket motor casings, fuel tanks, and other structural components. In the automotive industry, it is used to produce drive shafts, leaf springs, and pressure vessels for natural gas vehicles. In the oil and gas industry, it is used to make pipes, tanks, and other pressure vessels. Other applications include sporting goods (such as golf club shafts and fishing rods), utility poles, and wind turbine blades.
Future Trends
The future of filament winding looks promising with the increasing demand for lightweight, high-performance materials. Advances in fiber and resin technologies are expected to enhance the performance and reduce the cost of wound products. The development of winding machines with greater precision and speed is also anticipated. Furthermore, the adoption of filament winding in emerging applications such as renewable energy and electric vehicles is likely to drive the growth of this technology.