Compression Molding
Overview
Compression molding is a method of molding in which the molding material, generally preheated, is first placed in an open, heated mold cavity. The mold is closed with a top force or plug member, pressure is applied to force the material into contact with all mold areas, while heat and pressure are maintained until the molding material has cured. The process employs thermosetting resins in a partially cured stage, either in the form of granules, putty-like masses, or preforms.
Process
Compression molding is a high-volume, high-pressure method suitable for molding complex, high-strength fiber-reinforced parts. The material to be molded is positioned in the mold cavity and the heated platens are closed by a hydraulic ram. Bulk molding compound (BMC) or sheet molding compound (SMC), are conformed to the mold form by the applied pressure and heated until the molding compound cures. The process employs thermosetting resins in a partially cured stage, either in the form of granules, putty-like masses, or preforms.
Materials
Thermoset materials are the most commonly used materials for compression molding. Typical thermoset materials include epoxies, polyesters, and phenolics. Thermoplastic materials can also be compression molded, with the process adjusted to ensure the materials remain in the mold long enough to fully harden.
Applications
Compression molding is commonly used to manufacture large flat or moderately curved parts. Thus, it is well suited to the manufacture of panels for cars, boats, and other similar products. Other common applications include the production of complex high-strength parts, such as gears, clips, and connectors.
Advantages and Disadvantages
The advantages of compression molding include its ability to mold large, fairly intricate parts. It also has the lowest cost of operation over the long run. However, it is not suitable for some types of parts, and the initial costs can be quite high.
See Also
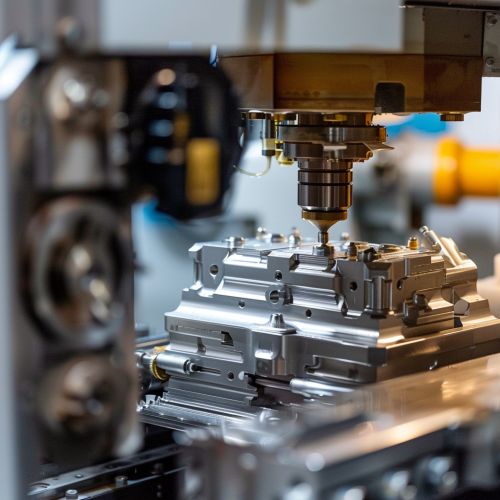
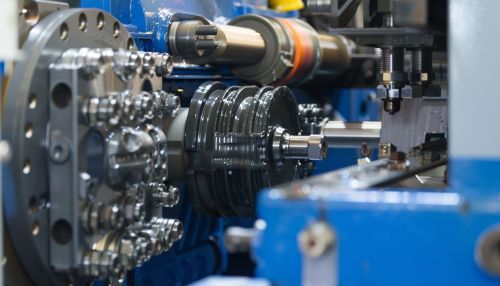
.