Pultrusion
Introduction
Pultrusion is a continuous manufacturing process used to create products of constant cross-section like tubes, rods, and structural shapes. The term "pultrusion" combines "pull" and "extrusion". Extrusion is a process where material is pushed through a die of the desired cross-section, while pultrusion is where the material is pulled through the dieExtrusion.
Process
The process of pultrusion involves pulling raw materials (rather than pushing, as is the case with extrusion) through a heated steel die to create a continuous composite profile. The raw materials used in the pultrusion process are typically a liquid resin mixture (containing resin, fillers, and specialized additives) and flexible textile reinforcing fibers.
The process begins with the pulling of the reinforcement materials through a resin bath or resin impregnation system. The resin bath contains a mixture of a polymer resin and various additives such as pigments and fire retardants. The fibers are completely saturated with the resin mixture, ensuring that all voids are eliminated and the fiber is completely wetted out by the resin.
The wetted reinforcement package is then formed to the desired shape and pulled into a heated steel die. Once inside the die, the resin cure is initiated by the heat from the die and the reaction with the catalysts in the resin mix. The curing process hardens the resin and creates a rigid product with the shape of the die cavity.
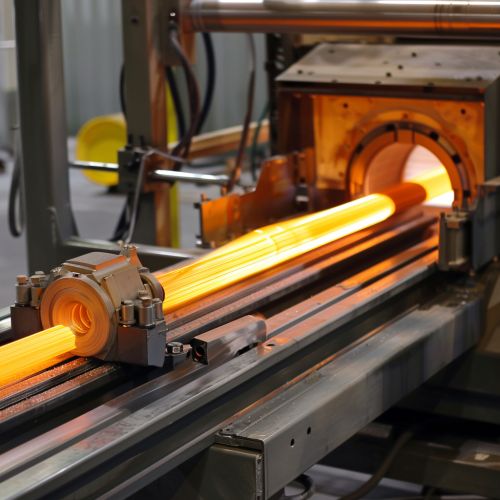
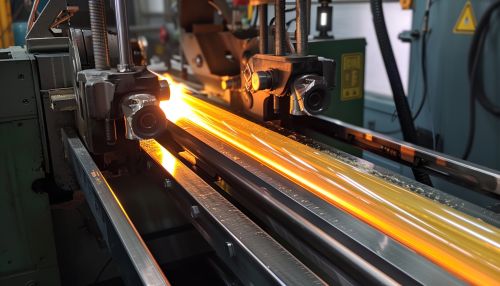
Materials
The selection of materials for the pultrusion process is key to the properties of the finished product. The two main types of materials used in pultrusion are the matrix and the reinforcement.
Matrix
The matrix binds the fibers together and provides the composite with environmental and chemical resistance. The most commonly used matrix is a polyester thermoset resin, although other resins such as vinylester, epoxy, and polyurethane are also used. The choice of matrix can have a profound effect on the properties of the finished composite.
Reinforcement
The reinforcement materials are what give the composite its strength and stiffness. These materials are typically glass fibers, although other materials such as carbon and aramid are also used. The reinforcement materials can be rovings (bundles of untwisted strands), continuous strands, mats, fabrics, or veils.
Applications
Pultruded products are used in a wide variety of applications due to their high strength, lightweight, and durability. Some of the most common applications include:
- Building and construction: Pultruded products are used in the construction industry for applications such as window frames, panels, and rebar.
- Electrical: Pultruded products are used in the electrical industry for applications such as insulators, antennas, and circuit boards.
- Infrastructure: Pultruded products are used in infrastructure for applications such as bridges, utility poles, and ladders.
- Automotive: Pultruded products are used in the automotive industry for applications such as drive shafts, leaf springs, and body parts.
Advantages and Disadvantages
Like any manufacturing process, pultrusion has its advantages and disadvantages.
Advantages
- Continuous process: Pultrusion is a continuous process, which means it can produce parts of any length.
- High strength: Pultruded products have high strength-to-weight ratios, making them ideal for many structural applications.
- Corrosion resistance: Pultruded products are highly resistant to corrosion, making them suitable for use in harsh environments.
Disadvantages
- Limited shapes: The pultrusion process is limited to parts of constant cross-section.
- High initial cost: The initial cost of setting up a pultrusion operation can be high due to the cost of the equipment and dies.