Thin Film Deposition
Introduction
Thin film deposition is a process used in semiconductor fabrication, surface science, and other related fields to create thin layers of material on a substrate. The thickness of these films can range from a few nanometers to several micrometers, depending on the application and the deposition method used.
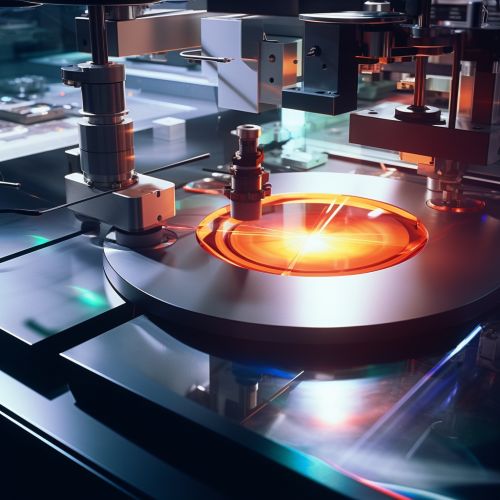
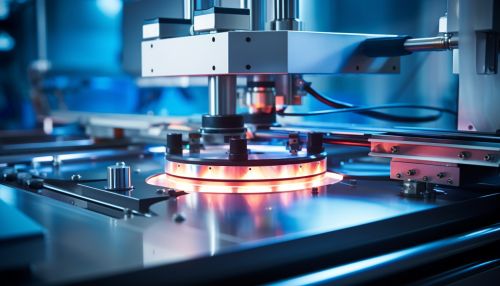
Types of Thin Film Deposition
There are two primary types of thin film deposition: physical vapor deposition (PVD) and chemical vapor deposition (CVD). Each of these methods has its own set of advantages and disadvantages, and the choice of method depends on the specific requirements of the application.
Physical Vapor Deposition (PVD)
Physical vapor deposition (PVD) is a method of thin film deposition that involves the evaporation or sputtering of a material, followed by its condensation onto a substrate. This process can be performed in a vacuum or under low pressure, and it can be used to deposit a wide range of materials, including metals, semiconductors, and insulators.
There are several types of PVD, including thermal evaporation, electron beam evaporation, sputter deposition, and pulsed laser deposition. Each of these methods has its own set of advantages and disadvantages, and the choice of method depends on the specific requirements of the application.
Chemical Vapor Deposition (CVD)
Chemical vapor deposition (CVD) is a method of thin film deposition that involves the reaction of one or more gaseous precursors on a heated substrate to form a solid film. This process can be performed at atmospheric pressure or under reduced pressure, and it can be used to deposit a wide range of materials, including metals, semiconductors, and insulators.
There are several types of CVD, including atmospheric pressure CVD, low pressure CVD, plasma-enhanced CVD, and metal-organic CVD. Each of these methods has its own set of advantages and disadvantages, and the choice of method depends on the specific requirements of the application.
Applications of Thin Film Deposition
Thin film deposition is used in a wide range of applications, including semiconductor device fabrication, optical coatings, protective coatings, and decorative coatings. In each of these applications, the properties of the thin film, such as its thickness, composition, and structure, can be precisely controlled to achieve the desired performance.
Semiconductor Device Fabrication
In Semiconductor device fabrication, thin film deposition is used to create the various layers of material that make up a semiconductor device. These layers can include the active semiconductor layer, the gate dielectric layer, the metal contacts, and the passivation layer. The properties of these layers, such as their thickness, composition, and structure, can be precisely controlled to achieve the desired device performance.
Optical Coatings
In optical coatings, thin film deposition is used to create layers of material that modify the reflection, transmission, and absorption properties of an optical surface. These coatings can be used to create anti-reflective coatings, high-reflective coatings, bandpass filters, and polarizers. The properties of these coatings, such as their thickness, composition, and structure, can be precisely controlled to achieve the desired optical performance.
Protective Coatings
In protective coatings, thin film deposition is used to create layers of material that protect a surface from environmental factors such as corrosion, wear, and oxidation. These coatings can be used to protect a wide range of materials, including metals, ceramics, and polymers. The properties of these coatings, such as their thickness, composition, and structure, can be precisely controlled to achieve the desired protective performance.
Decorative Coatings
In decorative coatings, thin film deposition is used to create layers of material that modify the appearance of a surface. These coatings can be used to create a wide range of colors, textures, and patterns. The properties of these coatings, such as their thickness, composition, and structure, can be precisely controlled to achieve the desired aesthetic effect.
Conclusion
Thin film deposition is a critical process in many areas of science and technology. By allowing the precise control of the thickness, composition, and structure of thin films, it enables the fabrication of a wide range of devices and coatings with tailored properties. As such, it is a key enabling technology in fields as diverse as semiconductor device fabrication, optical coatings, protective coatings, and decorative coatings.