The Role of Robotics in Industry 4.0
Introduction
The advent of the fourth industrial revolution, also known as Industry 4.0, has brought about a significant shift in the industrial landscape. Central to this transformation is the role of robotics, which has become an integral part of modern manufacturing and industrial processes.
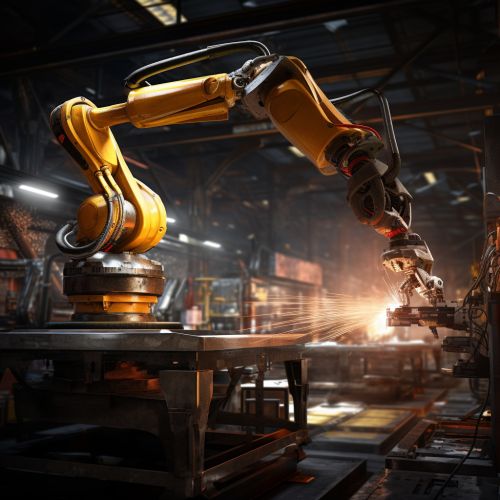
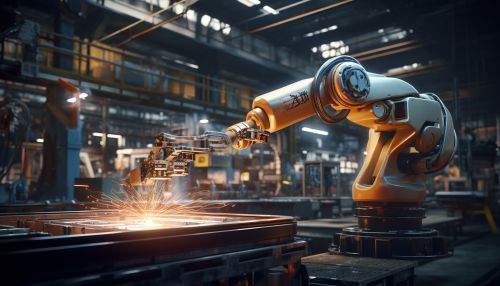
Evolution of Robotics in Industry
The application of robotics in industry is not a new phenomenon. The concept of using machines to perform tasks that were previously done by humans has been in existence since the first industrial revolution. However, the sophistication and capabilities of these machines have evolved significantly over the years, especially with the advent of Industry 4.0.
The first industrial robots were primarily used for tasks that were dangerous or unsuitable for humans, such as handling hazardous materials or working in extreme temperatures. These robots were typically large, expensive, and required significant programming and maintenance. However, with advancements in technology and the advent of Industry 4.0, the role of robotics in industry has expanded and evolved.
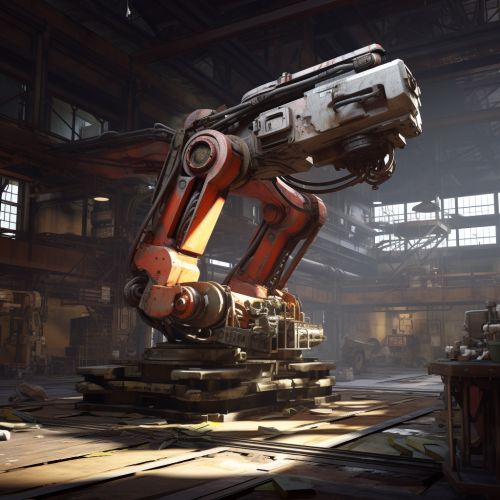
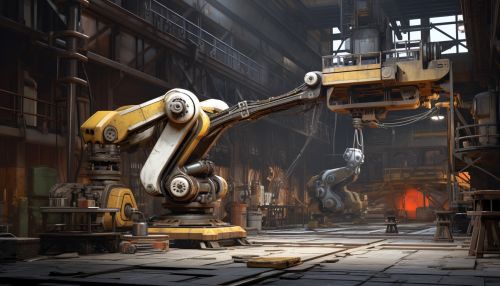
Role of Robotics in Industry 4.0
Industry 4.0 represents a new phase in the Industrial Revolution that focuses heavily on interconnectivity, automation, machine learning, and real-time data. Robotics plays a crucial role in this revolution, enabling increased productivity, efficiency, and flexibility in manufacturing processes.
Automation and Precision
One of the primary roles of robotics in Industry 4.0 is automation. Robots are used to automate repetitive tasks, freeing up human workers to focus on more complex tasks. This not only increases productivity but also reduces the risk of human error, leading to higher quality products.
In addition to automation, robots also offer a high level of precision. They can perform tasks with a degree of accuracy that is difficult for humans to achieve, making them ideal for tasks that require a high level of precision, such as assembling delicate electronics or precise machining.
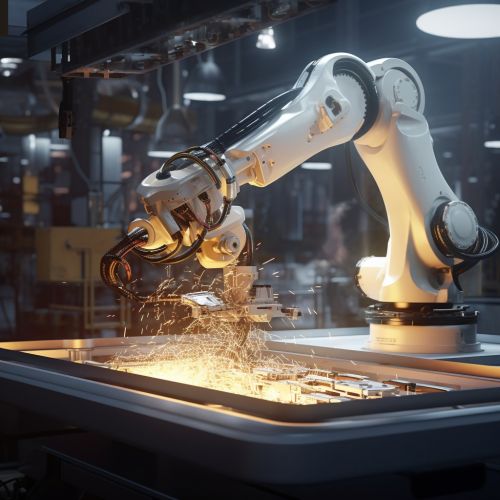
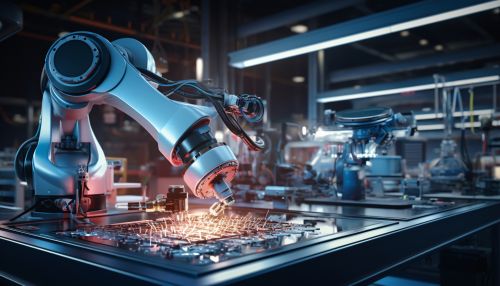
Interconnectivity and Data Analysis
Another key role of robotics in Industry 4.0 is interconnectivity. In the context of Industry 4.0, robots are not standalone entities but are part of a larger, interconnected system. They can communicate with other machines and systems, allowing for a more integrated and efficient production process.
Furthermore, robots in Industry 4.0 are capable of collecting and analyzing data. This data can be used to optimize production processes, predict maintenance needs, and make real-time adjustments to improve efficiency and productivity.
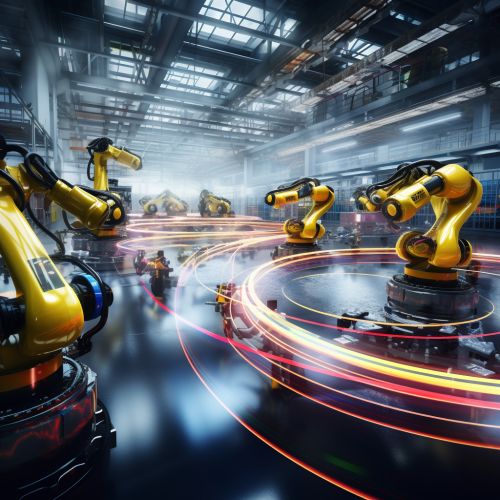
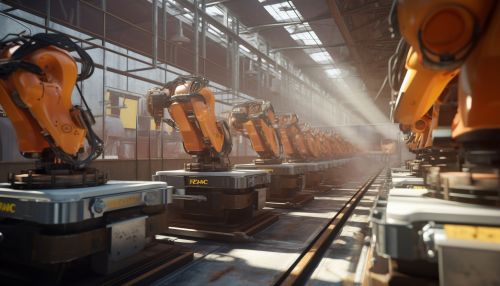
Flexibility and Adaptability
Robots in Industry 4.0 are also characterized by their flexibility and adaptability. Unlike traditional industrial robots, which are typically designed to perform a specific task, robots in Industry 4.0 can be reprogrammed to perform different tasks. This allows for greater flexibility in production processes, as the same robot can be used for different tasks as needed.
Furthermore, robots in Industry 4.0 are capable of learning and adapting to new tasks and environments. This is made possible through advancements in machine learning and artificial intelligence, which allow robots to learn from their experiences and improve their performance over time.
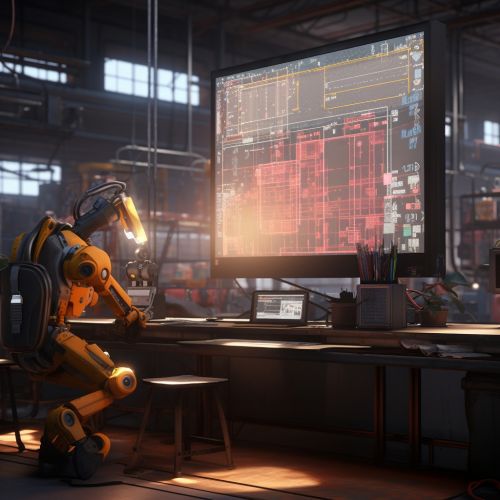
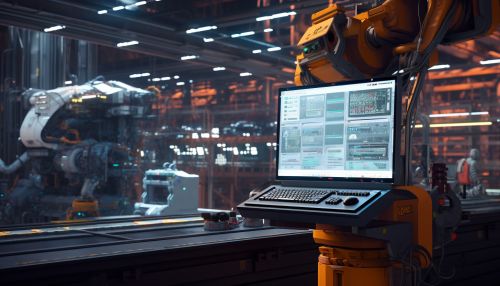
Challenges and Future Directions
Despite the many benefits of robotics in Industry 4.0, there are also challenges that need to be addressed. These include the high cost of robots, the need for skilled workers to operate and maintain them, and concerns about job displacement.
Looking ahead, the role of robotics in Industry 4.0 is likely to continue to evolve. With advancements in technology, we can expect to see robots that are even more intelligent, adaptable, and capable of working alongside humans in a collaborative manner.
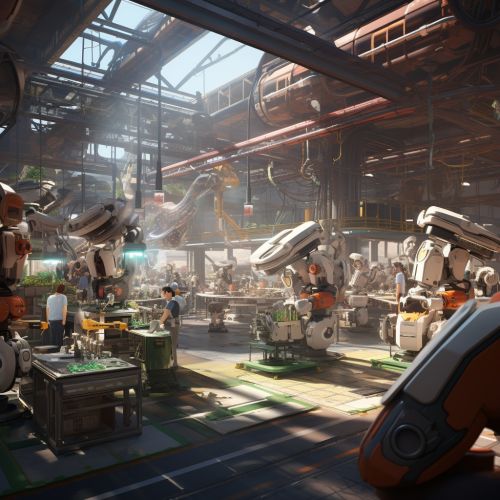
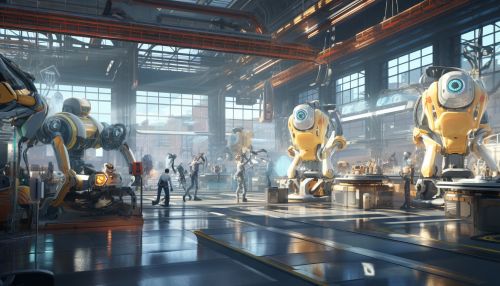