Industry 4.0
Introduction
Industry 4.0 represents the fourth industrial revolution in manufacturing and industry. It is characterized by the increasing digitization and interconnection of products, value chains, and business models. Industry 4.0 incorporates cyber-physical systems, the Internet of Things, and the Internet of Services into manufacturing environments to improve the process and production lines.
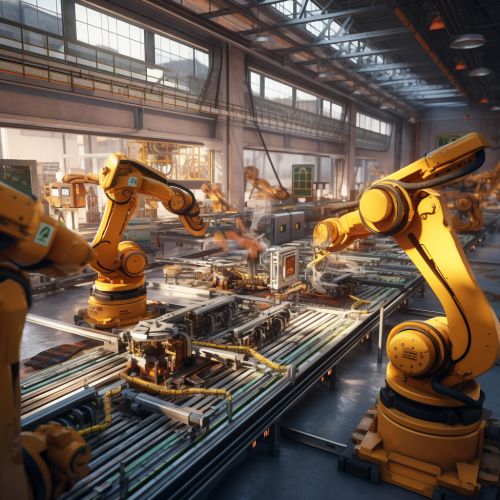
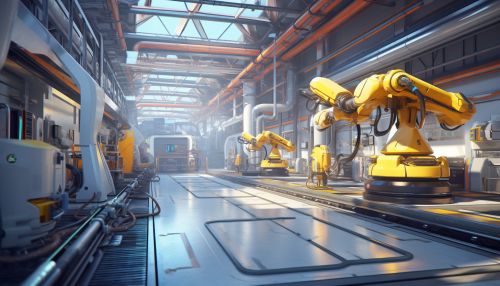
History and Development
The term "Industry 4.0" originated from a project in the high-tech strategy of the German government, which promotes the computerization of manufacturing. The concept was first introduced at the Hannover Messe industrial trade fair in 2011. The term "Industry 4.0" stands for the fourth industrial revolution, which is defined by its focus on interconnectivity, automation, machine learning, and real-time data.
Key Components of Industry 4.0
Industry 4.0 is built on nine technology pillars, each contributing to the digitization and interconnection of the industrial sector. These pillars include:
- Cyber-Physical Systems
- Internet of Things
- Internet of Services
- Big Data and Analytics
- Additive Manufacturing
- Autonomous Robots
- Simulation
- Horizontal and Vertical System Integration
- Cloud Computing
Cyber-Physical Systems
Cyber-Physical Systems (CPS) are integrations of computation, networking, and physical processes. Embedded computers and networks monitor and control the physical processes, with feedback loops where physical processes affect computations and vice versa.
Internet of Things
The Internet of Things (IoT) is a network of physical objects—devices, vehicles, appliances—embedded with sensors, software, network connectivity, and computing capability enabling them to collect, exchange, and act on data, often without human intervention.
Internet of Services
In the context of Industry 4.0, the Internet of Services (IoS) enables devices, machines, and components to provide services on the Internet. This allows for new business models that offer products as a service.
Big Data and Analytics
Big Data and Analytics in Industry 4.0 involves the collection and comprehensive evaluation of data from many different sources, especially machine and log data, which are of a very high volume, to support real-time decision making.
Additive Manufacturing
Additive Manufacturing involves the use of 3D-printing technologies to produce complex 3D-printed products. In the context of Industry 4.0, this enables more personalized and differentiated products.
Autonomous Robots
Autonomous Robots are capable of performing tasks with a high degree of autonomy, which are especially relevant in manufacturing and production processes.
Simulation
Simulation in Industry 4.0 involves the real-time connection of the virtual and physical world. This allows for the testing and optimization of machine settings in the virtual world before the physical changeover.
Horizontal and Vertical System Integration
Industry 4.0 promotes the integration of both horizontal and vertical systems. The former involves the networking of different companies across value chains. The latter integrates and links systems and processes within the same value chain.
Cloud Computing
Cloud Computing in Industry 4.0 involves the use of computing resources, both hardware and software, that are delivered as a service over a network (typically the internet).
Impact of Industry 4.0
Industry 4.0 has significant implications for production processes, work organization, and employees. These impacts can be seen in areas such as:
- Smart Factories
- Supply Chain Management
- Product Life-cycle Management
- Customer Relationship Management