The Role of Digital Twins in Industry 4.0
Introduction
Digital Twins are a fundamental component of the fourth industrial revolution, also known as Industry 4.0. They represent a paradigm shift in the industrial sector, enabling a new level of performance management and operational insight. By creating a virtual representation of a physical object or system, digital twins allow for real-time monitoring and simulation, leading to improved efficiency, reduced downtime, and enhanced product quality.
Definition of Digital Twins
Digital twins are virtual replicas of physical devices that data scientists and IT pros can use to run simulations before actual devices are built and deployed. They are an integral part of Industry 4.0, providing a bridge between the physical and digital world. The concept of a digital twin has been around since 2002, but it's only recently that the Internet of Things (IoT) has made it cost-effective to implement.
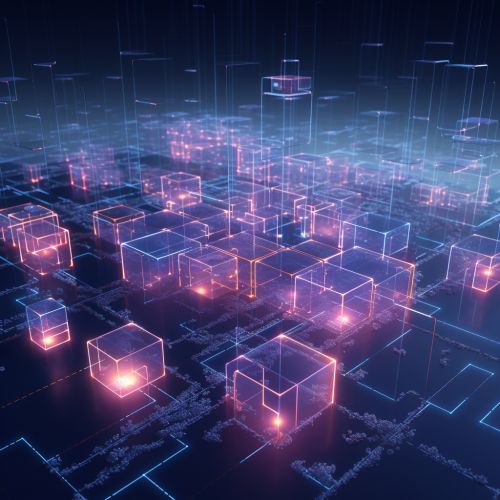
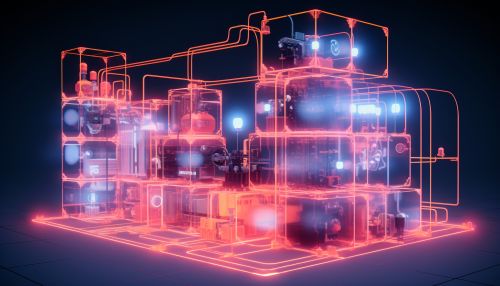
Role of Digital Twins in Industry 4.0
Digital twins play a crucial role in Industry 4.0 by providing a comprehensive view of a factory's operations and enabling predictive maintenance of machines. They can be used to simulate, predict, and optimize the factory system to better meet future challenges. This is achieved through the collection and analysis of data from various sources, including sensors embedded in the physical objects.
Predictive Maintenance
One of the key applications of digital twins in Industry 4.0 is in predictive maintenance. By creating a digital twin of a machine, it becomes possible to monitor its performance in real-time and predict when it might fail. This allows for maintenance to be scheduled before a failure occurs, reducing downtime and increasing productivity.
Performance Optimization
Digital twins can also be used to optimize the performance of a factory. By simulating different scenarios, it is possible to identify inefficiencies and make adjustments to improve productivity. This can include changes to the layout of the factory, adjustments to the production schedule, or modifications to the machines themselves.
Product Development
In the realm of product development, digital twins offer a powerful tool for design and testing. By creating a digital twin of a product, it is possible to test how it will perform under different conditions without having to build a physical prototype. This can significantly reduce the time and cost of product development.
Challenges and Future Directions
While digital twins offer significant benefits, there are also challenges to their implementation. These include the need for high-quality data, the complexity of creating accurate digital twins, and issues of data security and privacy. Despite these challenges, the future of digital twins in Industry 4.0 looks promising, with ongoing advancements in technology and increasing adoption by industry.