Predictive Maintenance
Introduction
Predictive maintenance (PdM) is a proactive maintenance strategy that involves assessing equipment condition by performing continuous (online) or periodic equipment monitoring. The ultimate goal of PdM is to perform maintenance at a scheduled point in time when the maintenance activity is most cost-effective and before the equipment loses performance within a threshold. This is in contrast to corrective maintenance, where maintenance is performed after failure has occurred, and preventive maintenance, where maintenance is performed in accordance with a pre-determined schedule.

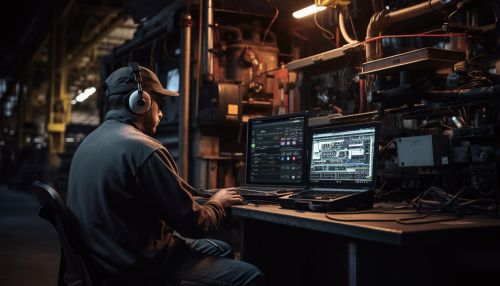
History
The concept of predictive maintenance originated in the late 20th century, as a natural evolution of preventive maintenance practices. With the advent of new technologies and the rise of Industry 4.0, predictive maintenance has gained significant traction in various industries, including manufacturing, oil and gas, and transportation.
Principles
Predictive maintenance relies on the use of various non-destructive testing techniques to evaluate the condition of in-service equipment in order to predict when maintenance should be performed. This approach offers cost savings over routine or time-based preventive maintenance, because tasks are performed only when necessary.
Techniques
There are several techniques used in predictive maintenance, including vibration analysis, oil analysis, thermal imaging, and ultrasonic leak detection. These techniques are used to monitor different indicators of equipment condition, such as temperature, vibration, and noise.
Vibration Analysis
Vibration analysis is a technique used to detect anomalies in the vibration patterns of machinery. By monitoring changes in vibration, it is possible to identify a variety of mechanical issues, such as misalignment, imbalance, and bearing wear, before they lead to equipment failure.
Oil Analysis
Oil analysis involves the sampling and laboratory analysis of a machine's lubricant. By testing for the presence of certain contaminants, the chemical composition of the oil, and its physical properties, it is possible to detect issues such as wear, overheating, and lubrication contamination.
Thermal Imaging
Thermal imaging is a technique that uses infrared imaging and measurement cameras to detect thermal energy emitted from an object. This can be used to identify hot spots in electrical systems and machinery, which can indicate potential points of failure.
Ultrasonic Leak Detection
Ultrasonic leak detection is a technique that uses high-frequency ultrasonic acoustic sensors to detect leaks in pressurized systems. This method is particularly useful for detecting gas leaks, as these often produce ultrasonic noise.
Applications
Predictive maintenance can be applied in a variety of industries and settings, including manufacturing, oil and gas, transportation, and power generation. By implementing predictive maintenance strategies, these industries can achieve significant cost savings, improve operational efficiency, and prevent unexpected equipment failures.
Benefits and Challenges
The primary benefit of predictive maintenance is cost savings. By performing maintenance only when necessary, organizations can avoid unnecessary downtime and reduce the costs associated with unnecessary maintenance. Predictive maintenance can also improve operational efficiency, as it allows for the scheduling of maintenance activities during non-productive times.
However, implementing a predictive maintenance strategy also presents several challenges. These include the need for skilled personnel to interpret condition monitoring data, the cost of condition monitoring equipment, and the need for a robust data infrastructure to support the predictive maintenance program.
Future Trends
With advancements in technology, particularly in the fields of Internet of Things (IoT) and Artificial Intelligence (AI), predictive maintenance is expected to become increasingly sophisticated. For example, machine learning algorithms can be used to predict equipment failures more accurately, and IoT devices can enable real-time condition monitoring of a wider range of equipment.