The Role of Additive Manufacturing in Aerospace Engineering
Introduction
Additive manufacturing, also known as 3D printing, is a transformative approach to industrial production that enables the creation of lighter, stronger parts and systems. It is a process that involves the creation of three-dimensional objects from a digital file. In the field of aerospace engineering, additive manufacturing plays a significant role due to its ability to produce complex geometries, reduce weight, and improve performance of aerospace components.
Overview of Additive Manufacturing
Additive manufacturing is a process that creates objects by adding material layer by layer, as opposed to subtractive manufacturing methods that remove material to create a final product. The process begins with a digital model, usually created using Computer-Aided Design software. The design is then divided into thin cross-sectional layers. These layers guide the 3D printer as it deposits material layer by layer, following the design's exact specifications.
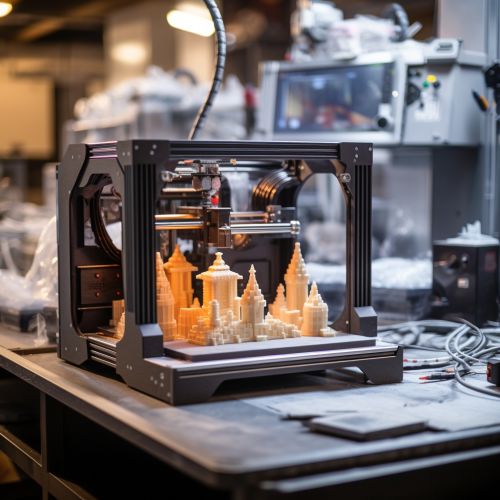
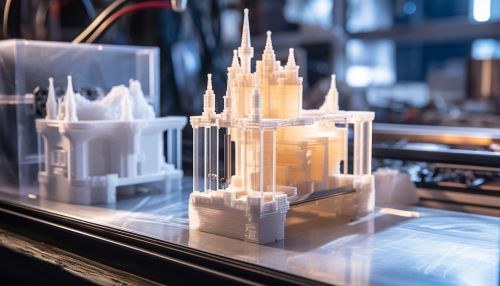
Additive Manufacturing Techniques
There are several techniques used in additive manufacturing, each with its own advantages and specific applications. Some of the most commonly used techniques in aerospace engineering include:
Stereolithography (SLA)
Stereolithography is one of the oldest forms of additive manufacturing. It uses a laser to solidify a liquid photopolymer layer by layer. The process is known for its high resolution and accuracy, making it suitable for creating detailed components.
Selective Laser Sintering (SLS)
Selective Laser Sintering involves the use of a laser to fuse powdered material layer by layer. SLS is commonly used with a variety of materials, including nylon, glass, and ceramics, and is known for its ability to create strong, durable parts.
Direct Metal Laser Sintering (DMLS)
Direct Metal Laser Sintering is similar to SLS, but it uses metal powders instead. This process is commonly used in aerospace engineering due to its ability to create complex, high-strength metal components.
Role in Aerospace Engineering
Additive manufacturing has a significant role in aerospace engineering due to its numerous advantages over traditional manufacturing methods. These include:
Weight Reduction
One of the primary benefits of additive manufacturing in aerospace engineering is the potential for weight reduction. By using additive manufacturing, engineers can create components with complex geometries that would be impossible with traditional manufacturing methods. This allows for the creation of lightweight, yet strong, components that can significantly reduce the overall weight of an aircraft.
Cost Reduction
Additive manufacturing can also lead to significant cost savings in the production of aerospace components. Traditional manufacturing methods often involve costly tooling and machining processes. In contrast, additive manufacturing requires less material and reduces the need for expensive tooling, leading to lower production costs.
Increased Performance
Additive manufacturing allows for the creation of components with improved performance characteristics. For example, it enables the production of parts with complex internal structures, which can improve the efficiency and performance of aerospace systems.
Future of Additive Manufacturing in Aerospace Engineering
The future of additive manufacturing in aerospace engineering looks promising. With ongoing advancements in technology, the potential applications and benefits of additive manufacturing are expected to increase. This includes the potential for the production of larger components, increased material options, and further improvements in cost and performance.