Selective Laser Sintering
Overview
Selective Laser Sintering (SLS) is an additive manufacturing (AM) technique that uses a laser as the power source to sinter powdered material, aiming the laser automatically at points in space defined by a 3D model, binding the material together to create a solid structure. It is a popular method used in the 3D printing industry.
History
The development of SLS technology started in the mid-1980s under the guidance of Dr. Carl Deckard and Dr. Joe Beaman at the University of Texas at Austin, with the first patent issued in 1989. The technology was initially commercialized by DTM Inc, which was later acquired by 3D Systems Corporation.
Principle
SLS involves the use of a high power laser to fuse small particles of plastic, metal, ceramic, or glass powders into a mass that has the desired three-dimensional shape. The laser selectively fuses the powdered material by scanning the cross-sections (or layers) generated by the 3D modeling program on the surface of a powder bed. After each cross-section is scanned, the powder bed is lowered by one layer thickness. A new layer of material is applied on top, and the process is repeated until the part is completed.
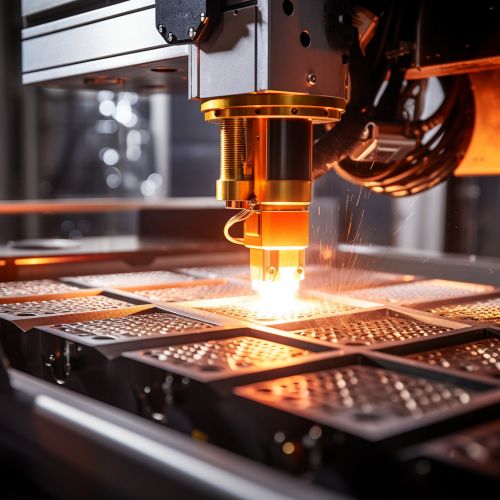
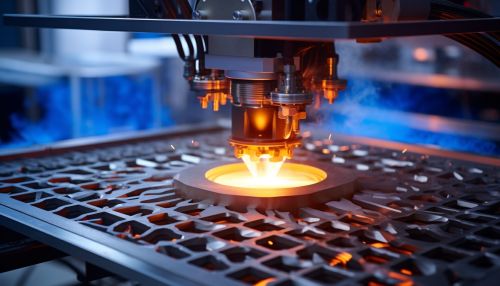
Materials
A wide range of materials can be used in SLS, from polymers like nylon (polyamide), and polystyrene to metals including steel, titanium, alloy mixtures, and composites. The physical properties of the final product are largely determined by the material used.
Applications
SLS can be used to fabricate prototypes, production parts, and functional testing. The technology is often used in the fields of aerospace, automotive, medical, and product design. In recent years, it has also been used in the fashion industry to create unique pieces of clothing and accessories.
Advantages and Disadvantages
The SLS process allows for the production of parts with complex geometries that cannot be achieved with other AM techniques. It also does not require the use of support structures which are needed in other AM techniques such as Stereolithography (SLA) and Fused Deposition Modeling (FDM). However, the surface finish in SLS is not as smooth as other techniques and the process is often more expensive due to high energy consumption and expensive materials.
Future Developments
The future of SLS technology is promising, with ongoing research and development in areas such as multi-material printing, increased build size, and improved surface finish. The technology is also expected to become more accessible as costs decrease, opening up new opportunities for innovation and design.