Process Management
Overview
Process management is a fundamental concept in the field of operations management and systems engineering. It involves the planning, monitoring, and control of all aspects of a process, as well as the implementation and maintenance of the process. The goal of process management is to improve efficiency, productivity, and performance in a consistent and predictable manner.
Definition
Process management is defined as the ensemble of activities of planning and monitoring the performance of a business process. The term usually refers to the management of business processes in an effective way to improve an organization's performance. In a nutshell, the process management implies a systematic approach to making an organization's workflow more effective, efficient, and adaptable to an ever-changing environment.
History
The concept of process management has its roots in the Industrial Revolution, where the need for efficiency in business operations became paramount. The early 20th century saw the emergence of scientific management principles, which sought to improve industrial efficiency through systematic measurement and control of work processes. The advent of computer technology in the mid-20th century further advanced the field of process management, allowing for the automation of complex processes and the development of sophisticated process management software.
Principles
Process management is guided by several key principles. These include:
- Process Orientation: This principle emphasizes the importance of processes in achieving business objectives. It involves viewing an organization as a system of interrelated processes, rather than individual departments or functions.
- Process Improvement: This principle involves the continuous monitoring and improvement of processes to increase efficiency and effectiveness. This is often achieved through techniques such as process mapping and benchmarking.
- Process Automation: This principle involves the use of technology to automate routine tasks within a process, freeing up human resources for more complex tasks.
- Process Measurement: This principle involves the use of metrics to measure the performance of a process. These metrics are often based on key performance indicators (KPIs) and are used to identify areas for improvement.
Process Management Cycle
The process management cycle is a framework for managing and improving processes. It typically involves the following stages:
1. Process Identification: This stage involves identifying the processes that need to be managed. This can be done through a process inventory, which lists all the processes within an organization.
2. Process Definition: This stage involves defining the process in detail, including its inputs, outputs, steps, and participants. This is often done using process maps or flowcharts.
3. Process Measurement: This stage involves measuring the performance of the process using key performance indicators (KPIs). This provides a baseline for improvement efforts.
4. Process Analysis: This stage involves analyzing the process to identify areas for improvement. This can involve techniques such as root cause analysis or Six Sigma methodologies.
5. Process Improvement: This stage involves implementing changes to the process to improve its performance. This can involve process redesign, process reengineering, or the implementation of new technology.
6. Process Control: This stage involves monitoring the process to ensure that it is performing as expected. This can involve the use of control charts or other statistical process control techniques.
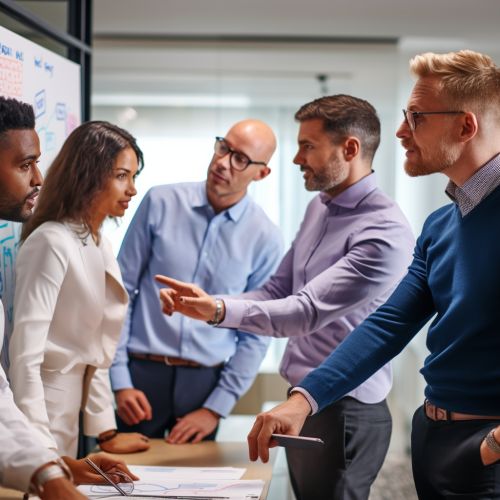
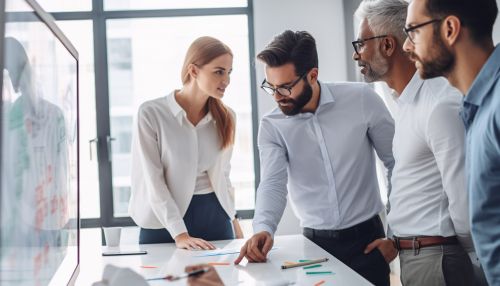
Benefits of Process Management
Process management offers several benefits to organizations. These include:
- Improved Efficiency: By streamlining and automating processes, organizations can reduce waste and improve productivity.
- Increased Quality: By standardizing processes and implementing quality control measures, organizations can improve the quality of their products or services.
- Reduced Costs: By improving efficiency and quality, organizations can reduce costs and increase profitability.
- Enhanced Flexibility: By continuously monitoring and improving processes, organizations can more easily adapt to changes in the business environment.
- Improved Customer Satisfaction: By improving the quality and efficiency of processes, organizations can better meet the needs of their customers, leading to increased customer satisfaction.
Challenges in Process Management
Despite its benefits, process management can also present several challenges. These include:
- Resistance to Change: Implementing process changes can be met with resistance from employees, particularly if they perceive the changes as threatening their jobs or altering their work routines.
- Complexity: Managing processes can be complex, particularly in large organizations with numerous interrelated processes.
- Lack of Skills: Implementing process management requires a specific set of skills, including process mapping, data analysis, and change management. Organizations may lack these skills internally and may need to invest in training or external consultants.
- Technology Integration: Implementing process automation requires the integration of various technologies, which can be complex and costly.
Conclusion
Process management is a critical component of effective operations management and systems engineering. By focusing on the management of processes, organizations can improve efficiency, quality, and customer satisfaction, while reducing costs and increasing flexibility. However, successful process management requires overcoming several challenges, including resistance to change, complexity, lack of skills, and technology integration.