Non-Destructive Testing
Introduction
Non-Destructive Testing (NDT) is a broad group of analysis techniques used in the science and technology industry to evaluate the properties of a material, component, or system without causing damage. As the name suggests, NDT does not alter the article being inspected, making it a highly valuable technique that can save both money and time in product evaluation, troubleshooting, and research.
History
The development of NDT has roots in industrial manufacturing and engineering, dating back to the late 19th century. The need to ensure the structural integrity of industrial products, particularly in the railway and boiler industries, led to the creation of rudimentary testing methods. These early methods, such as oil and chalk testing, have been refined and expanded upon to create the modern field of NDT.
Types of Non-Destructive Testing
There are several different types of NDT, each with its own specific uses and limitations. These include, but are not limited to, Radiographic, Ultrasonic, Magnetic Particle, Liquid Penetrant, Eddy-Current, Visual, and Acoustic Emission.
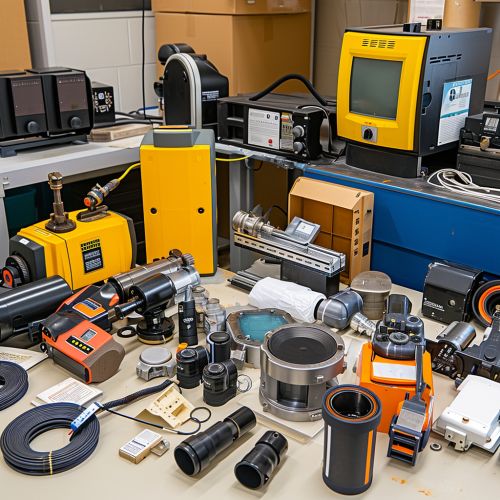
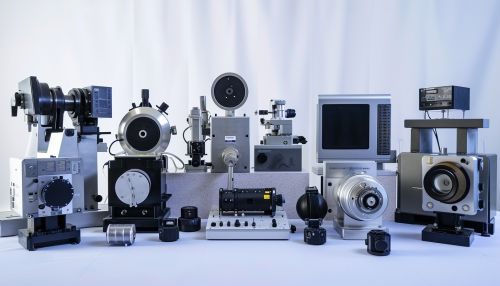
Radiographic Testing
Radiographic Testing (RT) involves the use of penetrating gamma or X-radiation to examine parts and products for imperfections. An X-ray generator or radioactive isotope is used as the source of radiation. Radiation is directed through a part and onto film or other detector. The resulting shadowgraph shows the internal features and soundness of the part.
Ultrasonic Testing
Ultrasonic Testing (UT) uses high frequency sound energy to conduct examinations and make measurements. Ultrasonic inspection can be used for flaw detection/evaluation, dimensional measurements, material characterization, and more.
Magnetic Particle Testing
Magnetic Particle Testing (MPT) is a method that is used to detect surface and near-surface discontinuities in ferromagnetic materials such as iron, nickel, cobalt, and some of their alloys.
Liquid Penetrant Testing
Liquid Penetrant Testing (LPT) is widely applied to detect surface discontinuities on materials. It involves the application of a liquid dye penetrant to the surface of a part, followed by the application of a developer to draw penetrant out of any surface-breaking discontinuities.
Eddy-Current Testing
Eddy-Current Testing (ECT) is a method that uses electromagnetic induction to detect and characterize surface and sub-surface flaws in conductive materials.
Visual Inspection
Visual Inspection (VI), or Visual Testing (VT), is the oldest and most basic method of inspection. It is the process of looking over a piece of equipment using the naked eye to see if there are any visible issues.
Acoustic Emission Testing
Acoustic Emission Testing (AET) is a method that is used to detect and locate the emission of short bursts of ultrasonic waves produced by a rapid release of energy in a material, or the transient elastic waves within the material caused by the release of localized stresses.
Applications
NDT is used in a variety of settings that require careful and precise analysis of materials, components, or systems. These include, but are not limited to, the aerospace industry, the automotive industry, civil engineering, the power industry, the petrochemical industry, and the pipeline industry.
Advantages and Limitations
Like any testing method, NDT has its advantages and limitations. The primary advantage of NDT is the ability to test materials and components without causing damage. This means that items do not have to be cut open or otherwise destroyed to be inspected. However, NDT methods can only detect and measure defects. They cannot determine if a material or component is fit for purpose or predict when failure may occur.
Future of Non-Destructive Testing
The future of NDT lies in the development of new methods and technologies, as well as the refinement of existing techniques. As industries continue to evolve and require more complex and reliable components, the demand for more sophisticated NDT techniques will continue to grow.