Cobots
Introduction
Cobots, or collaborative robots, are a type of industrial robot designed to work alongside human operators in a shared workspace. Unlike traditional industrial robots, which operate in isolation from human workers, cobots are designed with safety features that allow them to interact directly with human workers in a co-operative manner. This interaction can be in the form of assisting in tasks that are difficult, dangerous, or monotonous for humans.
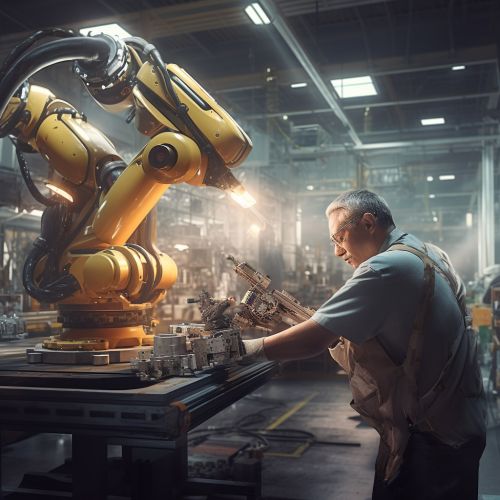
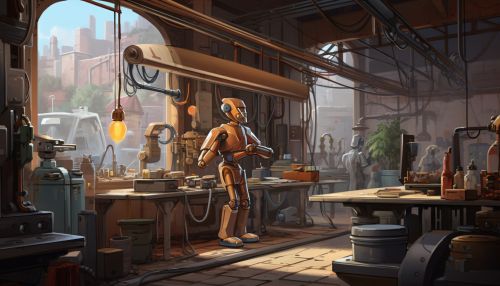
History and Development
The concept of cobots was first introduced in the late 1990s by researchers at the General Motors Foundation and the Northwestern University. The term "cobot" was coined to describe a new class of robots that were designed to physically interact with humans in a shared workspace.
The development of cobots was driven by the need to improve the safety and efficiency of industrial processes. Traditional industrial robots are typically large, powerful machines that operate in isolation from human workers due to safety concerns. However, this separation can limit the flexibility and adaptability of industrial processes, as it requires significant time and resources to reconfigure the workspace when changes are needed.
Cobots, on the other hand, are designed to be flexible and adaptable, capable of working alongside humans without the need for physical barriers or complex safety systems. This allows for a more dynamic and responsive industrial process, where robots and humans can work together in a collaborative manner.
Design and Functionality
Cobots are designed with a number of features that differentiate them from traditional industrial robots. These features are primarily focused on ensuring the safety of human workers and enabling effective collaboration in a shared workspace.
Safety Features
One of the key design features of cobots is their built-in safety systems. These systems are designed to ensure that the cobot can operate safely alongside human workers without the need for physical barriers or complex safety systems. This is achieved through a combination of sensors, software, and mechanical design features.
For example, many cobots are equipped with force sensors that allow them to detect when they come into contact with a human or another object. If the cobot detects a collision, it can immediately stop or reduce its force to prevent injury. Some cobots also use machine vision systems to monitor their surroundings and avoid collisions.
Flexibility and Adaptability
Another key design feature of cobots is their flexibility and adaptability. Unlike traditional industrial robots, which are typically programmed to perform a specific task in a specific way, cobots are designed to be easily reprogrammable and adaptable to a wide range of tasks.
This flexibility is achieved through a combination of software and hardware features. On the software side, cobots are typically equipped with user-friendly programming interfaces that allow operators to easily reprogram the robot for different tasks. On the hardware side, many cobots are designed with modular end-effectors that can be easily swapped out to perform different tasks.
Applications
Cobots are used in a wide range of industries and applications, including manufacturing, healthcare, logistics, and more. Their flexibility and adaptability make them well-suited to a variety of tasks, from assembly and packaging to inspection and testing.
Manufacturing
In the manufacturing industry, cobots are often used for tasks such as assembly, packaging, and inspection. They can work alongside human operators to handle parts, assemble products, or inspect finished goods. Their flexibility and adaptability make them well-suited to these tasks, as they can be easily reprogrammed to handle different parts or perform different tasks as needed.
Healthcare
In the healthcare industry, cobots are used in a variety of applications, from assisting in surgeries to helping with patient care. For example, cobots can be used to assist surgeons during complex procedures, providing steady, precise movements that can enhance the surgeon's capabilities. They can also be used in patient care settings, helping to lift and move patients or assist with rehabilitation exercises.
Logistics
In the logistics industry, cobots are used for tasks such as picking and packing, sorting, and transportation. They can work alongside human operators to pick items from shelves, pack boxes, or sort items for shipment. Their ability to work safely alongside humans, combined with their flexibility and adaptability, make them well-suited to these tasks.
Future of Cobots
The future of cobots is likely to see continued growth and development, as advances in technology and changes in industrial processes drive increased demand for flexible, collaborative robots.
One area of potential growth is in the development of more advanced safety systems. While current cobots are designed with a range of safety features, there is ongoing research into new technologies and techniques that could further enhance the safety of cobots. This could include advances in sensor technology, machine vision systems, and artificial intelligence.
Another area of potential growth is in the development of more advanced programming interfaces. While current cobots are designed to be easily programmable, there is ongoing research into new methods and tools that could make it even easier for operators to program and control cobots. This could include advances in natural language processing, augmented reality interfaces, and machine learning.