Ultrasonic Testing
Introduction
Ultrasonic testing (UT) is a family of non-destructive testing techniques based on the propagation of ultrasonic waves in the object or material tested. It is a crucial aspect of many industries, including aerospace, automotive, and power generation.

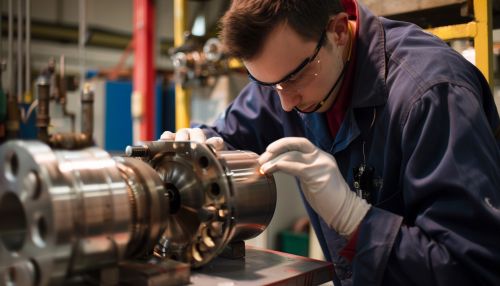
Principles of Ultrasonic Testing
Ultrasonic testing works on the principle of propagation of ultrasonic waves in a material. These waves are sound waves of frequency higher than the audible range. They are introduced into the material through a probe, which consists of a piezoelectric transducer. The piezoelectric transducer converts electrical energy into mechanical energy in the form of ultrasonic waves.
Types of Ultrasonic Testing
There are several types of ultrasonic testing, each with its own specific applications and advantages. The most commonly used types include:
Pulse Echo Testing
Pulse echo testing is the most common type of ultrasonic testing. In this method, a single transducer sends an ultrasonic pulse into the material. The transducer then switches to receive mode and waits for the echo of the pulse to return.
Through Transmission Testing
In through transmission testing, one transducer sends the ultrasonic pulse while another transducer on the opposite side of the material receives it. This method is particularly useful for detecting flaws that are perpendicular to the surface of the material.
Phased Array Ultrasonic Testing
Phased array ultrasonic testing (PAUT) is a more advanced method that uses multiple transducers to send and receive ultrasonic waves. This allows for more precise control over the direction and focus of the ultrasonic beam.
Applications of Ultrasonic Testing
Ultrasonic testing has a wide range of applications across various industries. Some of the most common applications include:
Aerospace Industry
In the aerospace industry, ultrasonic testing is used to inspect aircraft components for defects that could lead to catastrophic failure. This includes inspection of engine components, wings, and fuselage structures.
Automotive Industry
In the automotive industry, ultrasonic testing is used to inspect welded joints, castings, and other critical components for defects. It is also used to measure the thickness of materials, such as brake rotors, to ensure they meet specified tolerances.
Power Generation Industry
In the power generation industry, ultrasonic testing is used to inspect turbines, boilers, and other critical components for defects. It is also used to monitor the condition of these components over time to predict when maintenance or replacement may be necessary.
Advantages and Limitations
Ultrasonic testing has several advantages over other non-destructive testing methods. It can detect both surface and subsurface defects, and it can provide precise information about the size, shape, and location of defects. It can also be used to measure the thickness of materials and the depth of defects.
However, ultrasonic testing also has some limitations. It requires a medium to propagate the ultrasonic waves, so it cannot be used on materials that are not solid or that have a high air or water content. It also requires a high level of skill and experience to interpret the results accurately.