Profibus
Overview
Profibus (Process Field Bus) is a standard for fieldbus communication in automation technology. It was first promoted in 1989 by the German federal department of education and research, together with several companies and institutes. Profibus is not one communication system, but a variety of protocols built on the same field-bus technology bundle. These protocols are Profibus DP (Decentralized Peripherals), Profibus PA (Process Automation), and Profibus FMS (Fieldbus Message Specification).
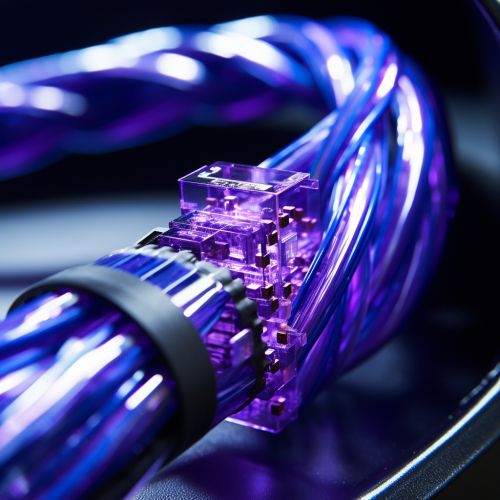
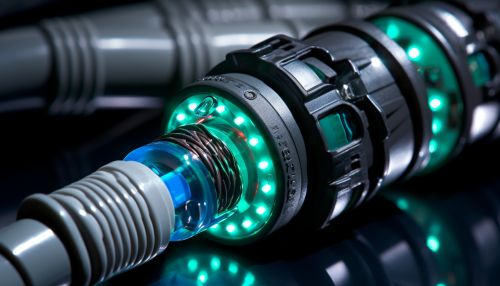
History
The development of Profibus can be traced back to a publicly funded project in Germany in the late 1980s. The aim was to create a fieldbus standard that could be used in a wide range of industrial automation applications. The result was Profibus, which was officially launched in 1989. The Profibus User Organization (PNO) was established in the same year to promote the use of Profibus and to ensure its continued development.
Profibus Protocols
Profibus DP
Profibus DP (Decentralized Peripherals) is used to operate sensors and actuators via a centralized controller in production (discrete) automation applications. The high-speed communication is particularly suitable for fast control and data acquisition tasks. The DP protocol includes the Profisafe profile for fail-safe data transmission.
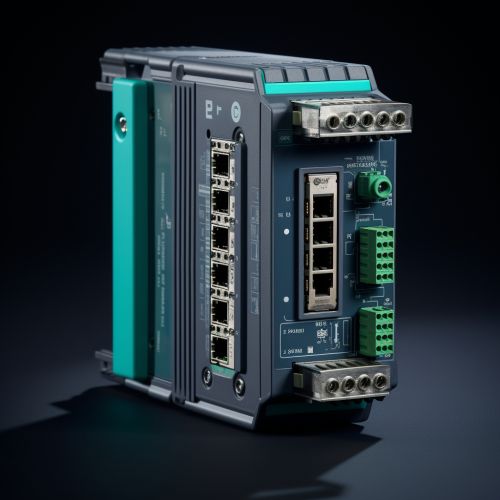
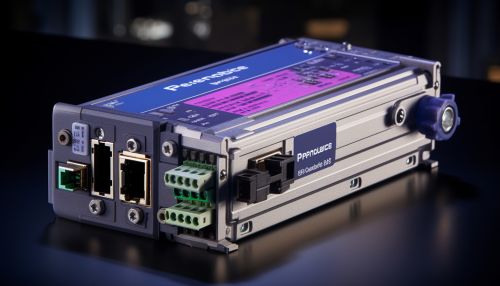
Profibus PA
Profibus PA (Process Automation) is used to monitor measuring devices via a process control system in process automation applications. This protocol is designed to use the same bus for communication and power supply to the field devices, reducing the need for separate power cables. The PA protocol includes the Profisafe profile for fail-safe data transmission and the Profinet profile for communication with Profinet networks.
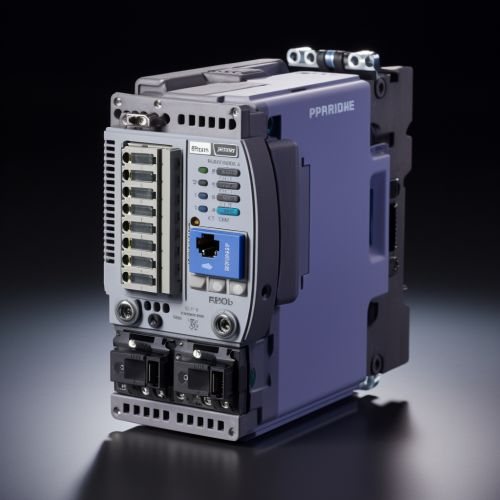
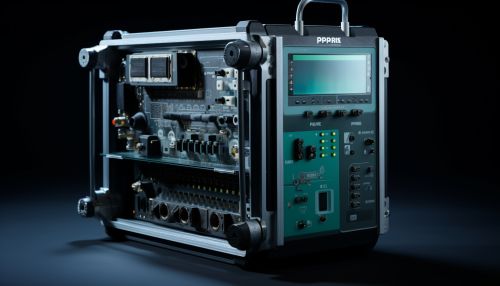
Profibus FMS
Profibus FMS (Fieldbus Message Specification) is a comprehensive, high-level protocol for complex communication tasks. It is rarely used in new installations but is still supported for legacy systems.
Profibus Physical Layers
Profibus uses several physical layers, including RS-485 for high-speed data transmission and MBP (Manchester Bus Powered) for power and data transmission over the same bus in process automation applications.
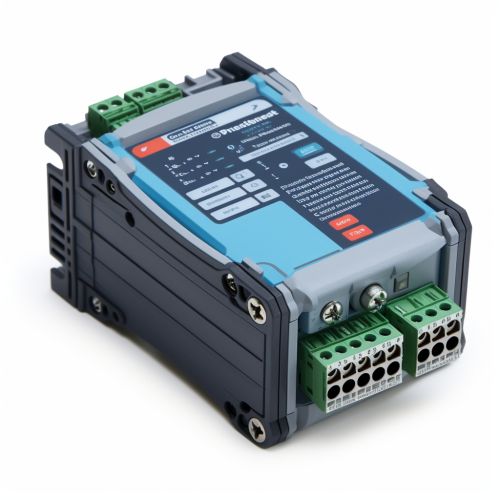
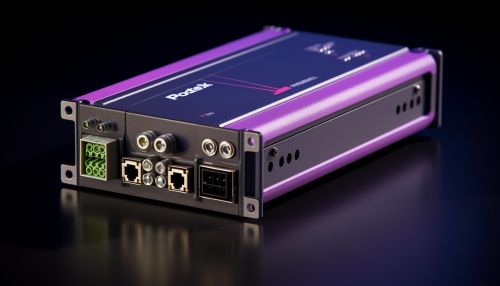
Profibus Network Configuration
Profibus networks can be configured in several ways, including line, star, and ring topologies. The choice of topology depends on the specific requirements of the application, such as the number of devices, the distance between devices, and the need for redundancy.
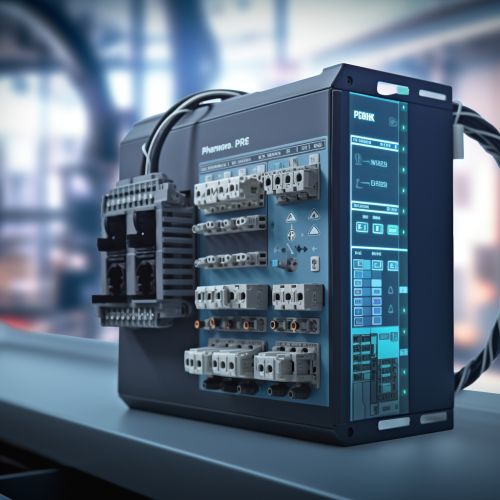
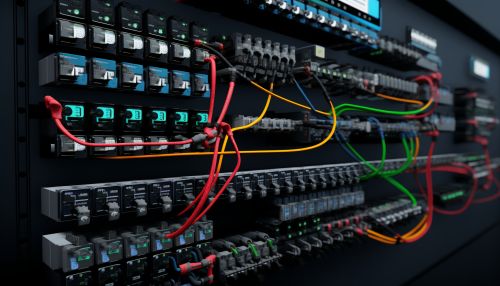
Profibus Communication
Profibus communication is based on the producer/consumer model. Data is exchanged in cyclic data exchange where the controller (producer) sends output data to the devices and the devices (consumers) send input data to the controller.
Profibus and Profinet
Profibus and Profinet are complementary technologies. While Profibus is widely used for fast, deterministic data exchange in factory automation, Profinet is used for real-time Ethernet communication and is increasingly used in process automation as well.
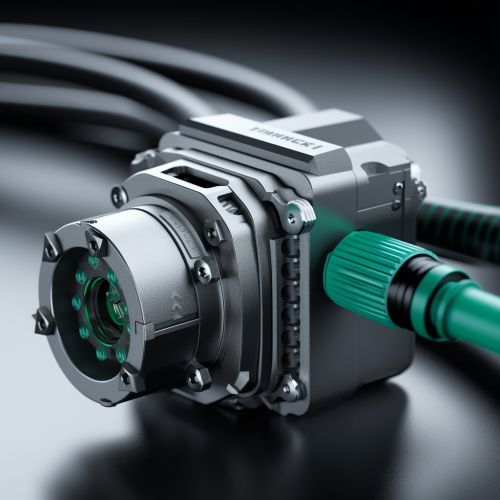
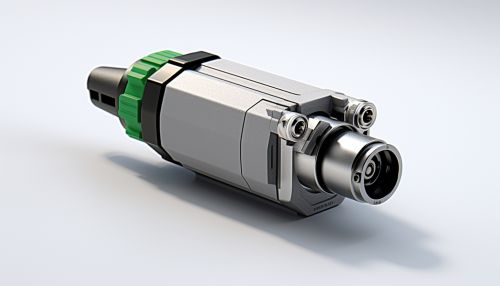