Odometry
Introduction
Odometry is a method used in robotics to estimate the change in position over time. It is a crucial aspect of mobile robotic navigation, as it provides information about the robot's current position and orientation relative to a known starting point. The term "odometry" is derived from the Greek words "hodos," meaning path or gateway, and "metron," meaning measure.
Principles of Odometry
The basic principle of odometry is to measure the change in position over time. This is typically accomplished by counting the number of wheel rotations or steps taken by a robot and using this information to calculate the distance traveled. The direction of movement is also tracked, which, when combined with the distance information, allows for the determination of the robot's current position and orientation.
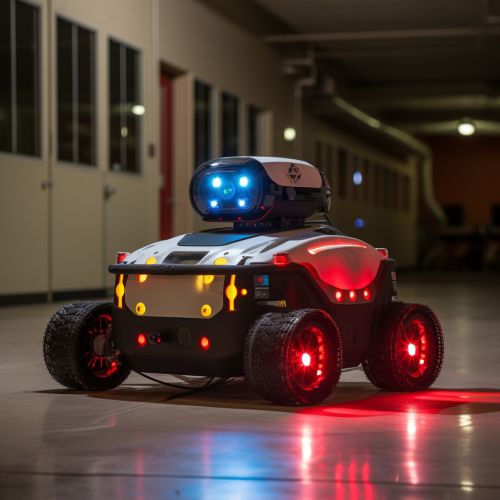
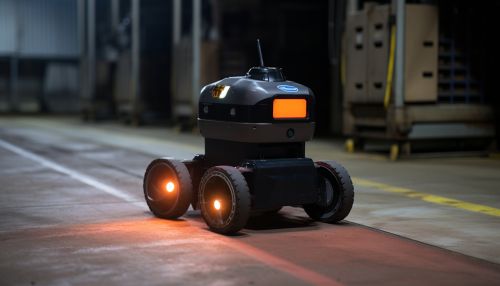
The accuracy of odometry is affected by several factors, including the precision of the measurement devices used, the surface on which the robot is moving, and the robot's speed. Errors in odometry measurements can accumulate over time, leading to a drift in the estimated position. This is often referred to as odometric drift or cumulative error.
Types of Odometry
There are several types of odometry, each with its own advantages and disadvantages. The most common types are wheel odometry, visual odometry, and inertial odometry.
Wheel Odometry
Wheel odometry is the most basic form of odometry. It involves counting the number of wheel rotations or steps taken by a robot to estimate the distance traveled. The direction of movement is also tracked, allowing for the determination of the robot's current position and orientation. Wheel odometry is simple and inexpensive to implement but is prone to errors due to wheel slippage or uneven terrain.
Visual Odometry
Visual odometry involves using cameras or other visual sensors to track the movement of features in the environment. By comparing successive images, the robot can estimate its change in position and orientation. Visual odometry can be more accurate than wheel odometry, especially in environments with rich visual features. However, it is more computationally intensive and may be affected by changes in lighting conditions or occlusion of features.
Inertial Odometry
Inertial odometry uses Inertial Measurement Units (IMUs) to estimate the robot's change in position and orientation. IMUs measure linear and angular motion, allowing for more accurate odometry measurements than wheel odometry, especially in environments where wheel slippage is likely. However, IMUs can be affected by drift over time, and their accuracy can be influenced by temperature changes and other environmental factors.
Applications of Odometry
Odometry is used in a wide range of applications, from simple tasks such as guiding a robot vacuum cleaner around a room, to complex tasks such as navigating a rover on Mars.
In industrial settings, odometry is used in automated guided vehicles (AGVs) to navigate warehouses and factories. In agriculture, odometry is used in autonomous tractors and other farming equipment to guide them around fields. In the military, odometry is used in unmanned ground vehicles (UGVs) for reconnaissance and other missions.
In research, odometry is used in a variety of fields, including robotics, computer vision, and artificial intelligence. It is a key component in the development of autonomous vehicles and is used in the study of animal and human locomotion.
Challenges and Future Directions
Despite its widespread use, odometry is not without its challenges. The main challenge is the accumulation of errors over time, known as odometric drift. This can lead to significant discrepancies between the estimated and actual position of the robot, especially over long distances or periods of time.
Various strategies have been developed to mitigate odometric drift, including the use of additional sensors, the integration of GPS data, and the use of advanced algorithms for error correction. However, these solutions often increase the complexity and cost of the system.
Looking forward, the field of odometry is likely to continue to evolve as new technologies and algorithms are developed. In particular, advances in machine learning and artificial intelligence could lead to more accurate and robust odometry systems. Furthermore, the increasing use of drones and other aerial vehicles is likely to spur further research into three-dimensional odometry.