Cylindrical Robots
Overview
A cylindrical robot is a type of industrial robot with a cylindrical work envelope. It operates within a cylindrical-shaped work space, hence its name. The robot's movements are based on a cylindrical coordinate system, which is defined by a distance measurement, an angle measurement, and a vertical measurement.
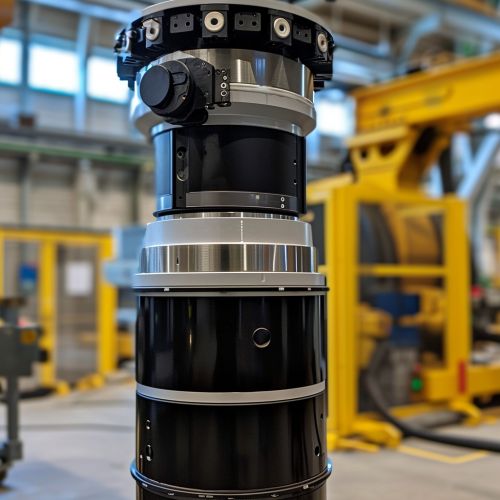
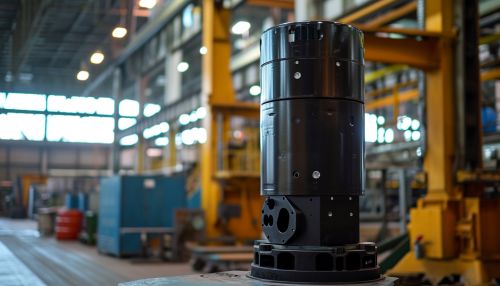
Design and Structure
The design of a cylindrical robot is based on a cylindrical coordinate system. This system is defined by three axes: the radial axis (R), the angular axis (θ), and the vertical axis (Z). The robot's arm moves along these axes, allowing it to perform tasks within a cylindrical work space.
The base of the robot is typically stationary, while the arm can move up and down (Z-axis), rotate around the base (θ-axis), and extend or retract (R-axis). This combination of movements allows the robot to reach any point within its cylindrical work space.
Applications
Cylindrical robots are commonly used in industrial settings for tasks such as assembly, handling, machine tending, and spot welding. Their design makes them particularly suitable for tasks that require a large vertical range of motion, such as stacking items on shelves or moving objects from one conveyor belt to another.
In addition to industrial applications, cylindrical robots are also used in research and development settings. For example, they may be used in laboratories for tasks such as sample handling and testing.
Advantages and Disadvantages
One of the main advantages of cylindrical robots is their large vertical range of motion. This makes them ideal for tasks that require a high degree of vertical movement, such as stacking items on shelves.
Another advantage is their simplicity. Cylindrical robots are relatively simple to design and build, and their movements are easy to program and control. This makes them a cost-effective choice for many applications.
However, cylindrical robots also have some disadvantages. One of the main disadvantages is their limited reach. Because their movements are based on a cylindrical coordinate system, they can only reach points within a cylindrical work space. This limits their flexibility and makes them less suitable for tasks that require a large horizontal range of motion.
Another disadvantage is their speed. Cylindrical robots are typically slower than other types of industrial robots, such as Cartesian robots or SCARA robots. This can limit their effectiveness in high-speed applications.
Future Developments
As technology advances, it is likely that cylindrical robots will become faster, more flexible, and more efficient. Advances in materials science may lead to the development of lighter, stronger robot arms. Improvements in control systems may allow for more precise movements and faster response times. And advances in artificial intelligence and machine learning may enable cylindrical robots to perform more complex tasks and adapt to changing conditions in real time.
Despite these potential advancements, it is unlikely that cylindrical robots will replace other types of industrial robots. Instead, they will continue to be used in applications where their unique capabilities provide the most benefit.