Articulated Robot
Introduction
An articulated robot is a type of industrial robot characterized by rotary joints. It has a wide range of applications in various industries due to its flexibility and precision. The robot's arm is connected through a series of rotary joints, allowing for a full range of motion in multiple directions.
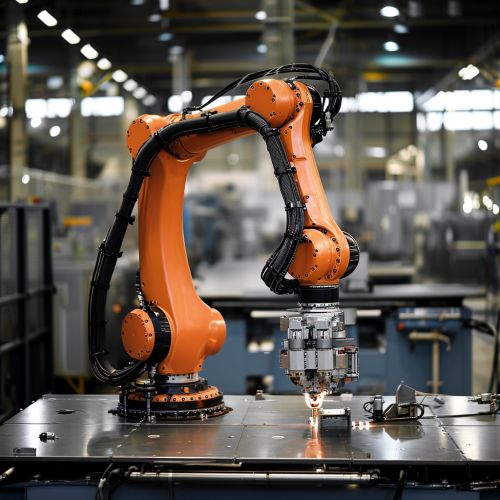
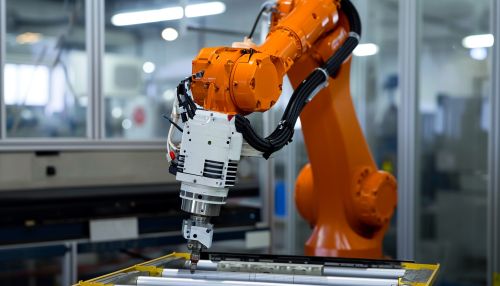
Design and Structure
The design of an articulated robot is primarily based on the human arm, consisting of three rotary joints. The arm's structure allows the robot to move in any direction within its reach. The arm is typically connected to the base of the robot, which can either be stationary or mobile. The base is responsible for the robot's stability and houses the robot's power supply and control systems.
The arm of an articulated robot is made up of several segments, each connected by a rotary joint. These joints, also known as axes, allow the robot to move in different directions. The number of axes determines the robot's degrees of freedom, which is the number of independent movements the robot can perform. Most articulated robots have six degrees of freedom, allowing them to perform complex tasks with high precision.
Applications
Articulated robots are used in a variety of industries due to their flexibility and precision. They can be found in manufacturing, where they are used for tasks such as welding, painting, assembly, and material handling. In the automotive industry, articulated robots are used for tasks such as spot welding and painting. They are also used in the electronics industry for tasks such as assembly and inspection.
In addition to industrial applications, articulated robots are also used in non-industrial settings. For example, they are used in healthcare for tasks such as surgery and patient care. In the entertainment industry, articulated robots are used for special effects and animation.
Control Systems
The control system of an articulated robot is responsible for coordinating the movements of the robot's arm. The control system receives instructions from a user or a computer program and translates these instructions into movements of the robot's arm.
The control system of an articulated robot typically consists of a controller and a series of sensors. The controller is the brain of the robot, responsible for processing instructions and controlling the robot's movements. The sensors provide feedback to the controller, allowing it to adjust the robot's movements as necessary.
Programming
Programming an articulated robot involves specifying the movements of the robot's arm in order to perform a specific task. This can be done using a variety of methods, including teach pendant programming, offline programming, and simulation-based programming.
Teach pendant programming involves manually moving the robot's arm to the desired positions and recording these positions. The robot can then repeat these movements to perform the task.
Offline programming involves using a computer program to specify the movements of the robot's arm. The program can then be loaded onto the robot's controller, allowing the robot to perform the task.
Simulation-based programming involves creating a virtual model of the robot and its environment. The movements of the robot's arm can then be specified and tested in the virtual environment before being loaded onto the robot's controller.
Advantages and Disadvantages
Articulated robots have several advantages over other types of industrial robots. They have a high degree of flexibility, allowing them to perform complex tasks with high precision. They also have a large work envelope, meaning they can reach a large area within their vicinity.
However, articulated robots also have some disadvantages. They can be complex to program, especially for complex tasks. They also require a significant amount of maintenance due to the large number of moving parts.
Future Trends
The future of articulated robots is likely to be shaped by advances in technology and changes in industry needs. One trend is the increasing use of artificial intelligence in robot control systems, which could allow robots to learn and adapt to new tasks more quickly. Another trend is the increasing use of collaborative robots, which are designed to work alongside humans in a shared workspace.