Quality Assessment: Difference between revisions
No edit summary |
No edit summary |
||
Line 101: | Line 101: | ||
* [[Code Review]] | * [[Code Review]] | ||
[[Image:Detail-92719.jpg|thumb|center|Factory worker inspecting products on an assembly line.]] | [[Image:Detail-92719.jpg|thumb|center|Factory worker inspecting products on an assembly line.|class=only_on_mobile]] | ||
[[Image:Detail-92720.jpg|thumb|center|Factory worker inspecting products on an assembly line.|class=only_on_desktop]] | |||
[[Category:Quality Control]] | [[Category:Quality Control]] | ||
[[Category:Management]] | [[Category:Management]] | ||
[[Category:Assessment]] | [[Category:Assessment]] |
Latest revision as of 16:07, 20 June 2024
Introduction
Quality assessment is a systematic process used to evaluate the quality of products, services, or processes. This evaluation is essential in various fields, including manufacturing, healthcare, education, and software development. The primary goal of quality assessment is to ensure that the subject being evaluated meets predefined standards and criteria. This article delves into the methodologies, tools, and applications of quality assessment, providing a comprehensive understanding of its significance and implementation.
Methodologies of Quality Assessment
Quality assessment methodologies can be broadly categorized into qualitative and quantitative approaches. Each approach has its own set of techniques and tools, which are chosen based on the specific requirements of the assessment.
Qualitative Approaches
Qualitative approaches focus on the descriptive aspects of quality. These methods often involve subjective judgments and are used when numerical data is insufficient or inappropriate.
Expert Judgment
Expert judgment involves the evaluation of quality by individuals with extensive knowledge and experience in the relevant field. This method is commonly used in fields such as healthcare, where clinical expertise is crucial for assessing the quality of patient care.
Focus Groups
Focus groups gather a small group of individuals to discuss and evaluate the quality of a product or service. This method is particularly useful for understanding user experiences and identifying areas for improvement.
Case Studies
Case studies involve an in-depth analysis of a single instance or a small number of instances. This method provides detailed insights into specific aspects of quality and is often used in educational research.
Quantitative Approaches
Quantitative approaches rely on numerical data and statistical methods to assess quality. These methods provide objective and reproducible results.
Surveys and Questionnaires
Surveys and questionnaires are widely used tools for collecting quantitative data on quality. They can be administered to large populations, providing a broad perspective on quality issues.
Statistical Process Control
Statistical process control (SPC) involves the use of statistical methods to monitor and control a process. SPC tools, such as control charts, help identify variations in the process that may affect quality.
Benchmarking
Benchmarking compares the quality of a product, service, or process against industry standards or best practices. This method helps organizations identify gaps in quality and implement improvements.
Tools for Quality Assessment
Various tools are employed in quality assessment to collect, analyze, and interpret data. These tools are essential for ensuring accurate and reliable evaluations.
Checklists
Checklists are simple yet effective tools for ensuring that all necessary criteria are considered during the assessment. They provide a structured approach to evaluating quality and help prevent oversight.
Control Charts
Control charts are graphical tools used in SPC to monitor process variability. They help identify trends and patterns that may indicate quality issues.
Root Cause Analysis
Root cause analysis (RCA) is a method used to identify the underlying causes of quality problems. Techniques such as the "5 Whys" and fishbone diagrams are commonly used in RCA.
Failure Mode and Effects Analysis
Failure mode and effects analysis (FMEA) is a systematic approach to identifying potential failure modes and their impact on quality. FMEA helps prioritize quality issues based on their severity, occurrence, and detectability.
Applications of Quality Assessment
Quality assessment is applied in various fields to ensure that products, services, and processes meet the required standards.
Manufacturing
In manufacturing, quality assessment ensures that products meet specifications and are free from defects. Techniques such as Six Sigma and Total Quality Management (TQM) are commonly used to improve product quality.
Healthcare
Quality assessment in healthcare focuses on patient safety, clinical outcomes, and patient satisfaction. Tools such as clinical audits and patient surveys are used to evaluate the quality of care.
Education
In education, quality assessment evaluates the effectiveness of teaching methods, curriculum, and student performance. Standardized testing and accreditation processes are commonly used to assess educational quality.
Software Development
Quality assessment in software development involves evaluating the functionality, performance, and security of software applications. Techniques such as code review and automated testing are used to ensure software quality.
Challenges in Quality Assessment
Despite its importance, quality assessment faces several challenges that can impact its effectiveness.
Subjectivity
Qualitative methods often involve subjective judgments, which can lead to inconsistencies in the assessment results. Ensuring inter-rater reliability is crucial for minimizing subjectivity.
Data Quality
The accuracy and reliability of the data used in quality assessment are critical. Poor data quality can lead to incorrect conclusions and ineffective quality improvement efforts.
Resource Constraints
Quality assessment can be resource-intensive, requiring significant time, effort, and financial investment. Organizations must balance the need for thorough assessments with available resources.
Resistance to Change
Implementing quality improvements based on assessment results can encounter resistance from stakeholders. Effective communication and change management strategies are essential for overcoming this challenge.
Future Trends in Quality Assessment
The field of quality assessment is continuously evolving, with new trends and technologies shaping its future.
Artificial Intelligence and Machine Learning
Artificial intelligence (AI) and machine learning (ML) are increasingly being used to enhance quality assessment. These technologies can analyze large datasets, identify patterns, and provide predictive insights, improving the accuracy and efficiency of assessments.
Big Data Analytics
Big data analytics enables organizations to analyze vast amounts of data from various sources, providing a comprehensive view of quality. This approach helps identify correlations and trends that may not be apparent through traditional methods.
Real-Time Quality Monitoring
Advancements in sensor technology and the Internet of Things (IoT) are enabling real-time quality monitoring. This approach allows organizations to detect and address quality issues promptly, reducing the risk of defects and improving overall quality.
Integrated Quality Management Systems
Integrated quality management systems (QMS) combine various quality assessment tools and methodologies into a cohesive framework. This approach streamlines the assessment process and ensures a holistic evaluation of quality.
Conclusion
Quality assessment is a vital process for ensuring that products, services, and processes meet the required standards. By employing a combination of qualitative and quantitative methodologies, utilizing appropriate tools, and addressing challenges, organizations can effectively evaluate and improve quality. As new technologies and trends emerge, the field of quality assessment will continue to evolve, offering new opportunities for enhancing quality in various domains.
See Also
- Total Quality Management
- Six Sigma
- Statistical Process Control
- Root Cause Analysis
- Failure Mode and Effects Analysis
- Automated Testing
- Code Review
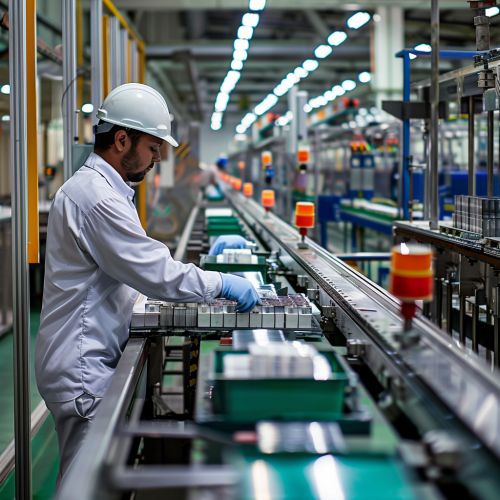
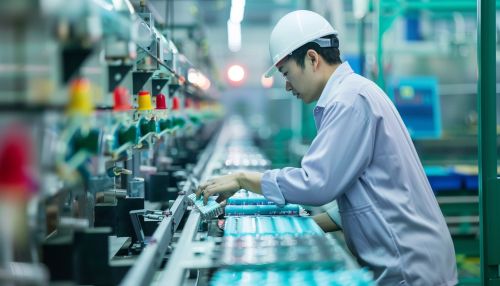