TIG Welding
Introduction
Tungsten Inert Gas (TIG) welding, also known as Gas Tungsten Arc Welding (GTAW), is a type of arc welding process that uses a non-consumable tungsten electrode to produce the weld. The weld area is protected from atmospheric contamination by an inert shielding gas (such as argon or helium), and a filler metal is normally used, though some welds, known as autogenous welds, do not require it.
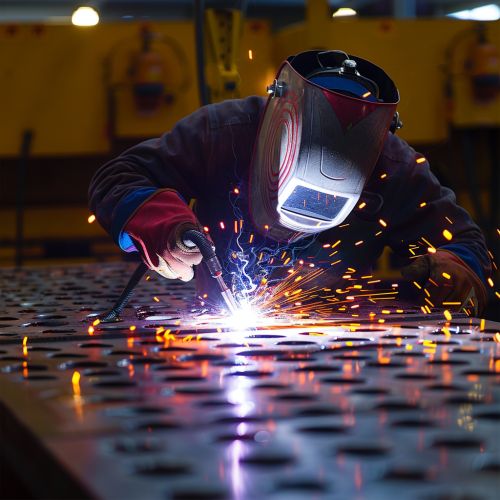
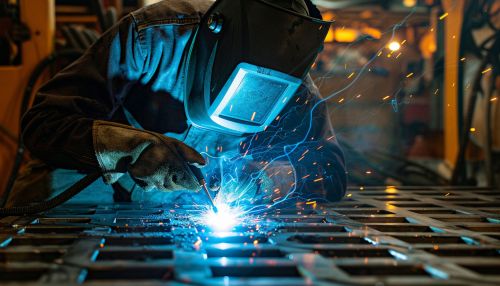
History
The TIG welding process was developed in the 1940s as a result of the need for welding lightweight materials during World War II. The process was patented by Russell Meredith of Northrop Aircraft, who used the term "Heliarc welding" due to the use of helium as the shielding gas.
Process
TIG welding is most commonly used to weld thin sections of stainless steel and non-ferrous metals such as aluminium, magnesium, and copper alloys. The process grants the operator greater control over the weld than competing processes such as Shielded Metal Arc Welding (SMAW) or Gas Metal Arc Welding (GMAW), allowing for stronger, higher quality welds.
Equipment
The equipment used for TIG welding includes a welding torch, power supply, electrode, shielding gas supply, and a filler material. The welding torch is designed to provide cooling (either air or water-based), and the power supply provides the necessary current for the welding process.
Electrodes
The electrodes used in TIG welding are made of tungsten or tungsten alloys due to their high melting point. The electrode is typically sharpened to a point to provide a concentrated arc, but can also be shaped to a ball or truncated shape depending on the welding requirements.
Shielding Gas
The shielding gas in TIG welding serves to protect the weld area from atmospheric gases such as nitrogen and oxygen, which can cause fusion defects, porosity, and weld metal embrittlement if they come in contact with the electrode, the arc, or the welding metal.
Filler Material
The filler material, if used, is added to the weld pool separately from the electrode. This allows the welder to control the deposit of filler metal into the weld joint.
Advantages and Disadvantages
TIG welding has several advantages over other welding methods. It provides excellent control over the welding variables, allowing for precise and high-quality welds. It also allows for welding at lower amperages, which is beneficial when welding thin materials. Additionally, TIG welding does not produce spatter, which can contaminate the weld and surrounding area.
However, TIG welding also has its disadvantages. It is a slower process compared to other welding methods, and it requires a high level of skill to perform effectively. It is also more expensive due to the cost of the equipment and shielding gas.
Applications
TIG welding is used in a variety of applications, including the aerospace industry, automotive repair and restoration, and in the manufacture of high-quality and critical welds in the nuclear and food industry.
Safety
As with any welding process, safety is a critical aspect of TIG welding. Welders are exposed to a number of hazards, including electric shock, harmful radiation, and inhalation of toxic fumes. Therefore, proper safety equipment such as welding helmets, gloves, and protective clothing should be used.