Stamping (Metalworking)
Introduction
Stamping, also known as pressing, is a metalworking process that uses dies to shape flat sheet metal, or 'stock', into finished parts. It is a complex process that can include a number of metal forming techniques — blanking, punching, bending and piercing, to name a few.
History
The history of stamping in metalworking dates back to 4000 BC, when artisans in the ancient Near East used the process to make intricate designs on their metalwork. The process has evolved significantly since then, with the development of new materials, techniques, and machinery.
Process
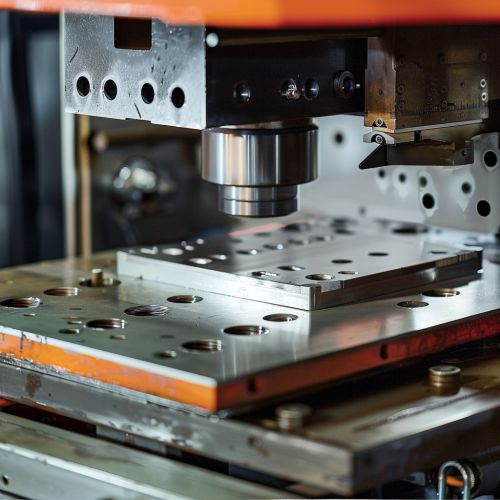
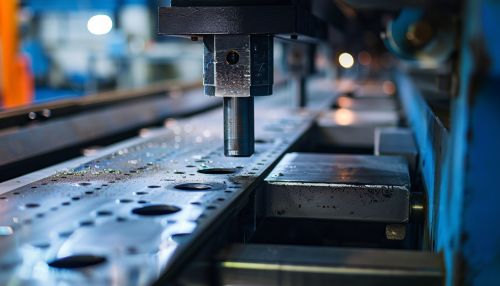
The stamping process begins with flat sheet metal, which is placed in a stamping press. The press, equipped with tool and die surfaces, shapes the metal into the desired shape. The process can be done in a single stage operation where every stroke of the press produces the desired form on the sheet metal part, or could occur through a series of stages.
Blanking
Blanking is a process in which a metal workpiece is removed from the primary metal strip or sheet when it is punched. The material that is removed is the new metal workpiece or blank.
Punching
Punching is a metal forming process that uses a punch press to force a tool, called a punch, through the workpiece to create a hole via shearing. Punching is often the cheapest method for creating holes in sheet materials in medium to high production volumes.
Bending
Bending is a manufacturing process that produces a V-shape, U-shape, or channel shape along a straight axis in ductile materials, most commonly sheet metal.
Piercing
Piercing is a shearing process where a punch and die are used to create a hole in sheet metal or a plate. The process and machinery are usually the same as that used in blanking, except that the piece being punched out is scrap in the piercing process.
Types of Stamping Operations
Stamping operations can be classified into two major types: sheet metal forming and punching.
Sheet Metal Forming
Sheet metal forming involves bending and stretching the sheet into various shapes. It includes operations like deep drawing, bending, corrugating, decambering, perforating, spinning, peen forming and more.
Punching
Punching involves creating holes in the sheet metal by applying a high force or pressure on the target area.
Equipment
The primary piece of equipment used in the stamping process is the stamping press. The press uses a tool and die surface to shape the metal. Other equipment used in the stamping process may include blanking machines, roll forming machines, and other metal forming equipment.
Materials
A wide variety of materials can be used in the stamping process, including various metals and alloys, plastics, composites, and ceramics. The choice of material depends on the requirements of the final product.
Applications
Stamping is widely used in various industries, including automotive, aerospace, electronics, and appliances. It is used to make a wide range of products, from small electronic parts to large automotive parts.
Advantages and Disadvantages
Stamping has many advantages, including high production rates, low labor costs, and the ability to make complex shapes. However, it also has some disadvantages, including high initial tooling costs and limitations on part depth and material thickness.