Silicon purification
Introduction
Silicon purification is a critical process in the production of semiconductive materials, which are extensively used in various industries such as electronics, solar energy, and information technology. The process involves refining raw silicon, which is abundant in nature in the form of silica (SiO2), into high-purity silicon suitable for these applications.
Raw Silicon Extraction
The first step in silicon purification is the extraction of raw silicon from silica. Silica is found in abundance in sand and quartz, which are its most common forms. The extraction process involves reducing silica with carbon in an electric arc furnace at temperatures over 2000 degrees Celsius. The reaction can be represented as follows:
SiO2 + 2C → Si + 2CO
This process results in metallurgical-grade silicon (MG-Si), which has a purity of about 98-99%. However, this level of purity is not sufficient for semiconductor applications, which require a purity of 99.9999% or higher. Therefore, further purification is necessary.
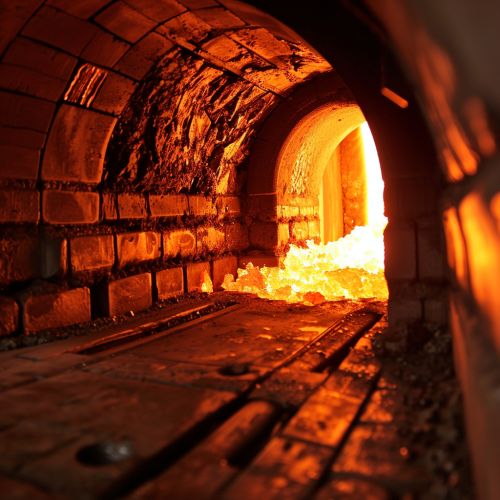
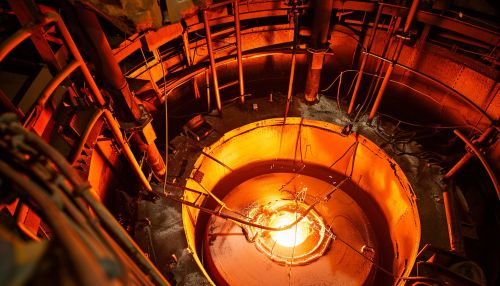
Silicon Purification Methods
There are several methods available for the purification of silicon. The choice of method depends on the required level of purity, the intended application, and economic considerations.
Siemens Process
The Siemens process is the most commonly used method for the production of high-purity silicon. In this process, MG-Si is reacted with hydrochloric acid (HCl) to produce trichlorosilane (SiHCl3). The trichlorosilane is then purified through distillation and subsequently decomposed at high temperatures to produce high-purity silicon and hydrogen chloride. The reaction can be represented as follows:
Si + 3HCl → SiHCl3 + H2
SiHCl3 → Si + 3HCl
The Siemens process can achieve a silicon purity of up to 99.9999%. However, it is energy-intensive and has a high cost of production.
Modified Siemens Process
The modified Siemens process is an improvement over the traditional Siemens process. It involves the use of additional purification steps such as fractional crystallization and zone refining to achieve higher purities. The process is more complex and requires more sophisticated equipment, but it can achieve a silicon purity of up to 99.99999%.
Fluidized Bed Reactor
The fluidized bed reactor (FBR) method is a newer technology for silicon purification. In this process, silicon particles are suspended in a gas (usually hydrogen) within a reactor. The gas is heated to high temperatures, causing the silicon particles to react with the gas and form high-purity silicon. The FBR method is less energy-intensive than the Siemens process and can achieve comparable purities. However, it is still under development and not yet widely used in industry.
Applications of High-Purity Silicon
High-purity silicon is a critical material in several industries. Its primary use is in the electronics industry, where it is used to manufacture integrated circuits and other semiconductor devices. High-purity silicon is also used in the production of solar cells for the solar energy industry. In addition, it is used in the manufacture of silicon-based optical fibers for the telecommunications industry.
Environmental Impact
The production of high-purity silicon has significant environmental impacts. The Siemens process, in particular, is energy-intensive and produces large amounts of carbon dioxide (CO2) and other greenhouse gases. In addition, the use of hydrochloric acid in the process results in the production of hydrogen chloride, a corrosive and toxic gas. Efforts are being made to develop more environmentally friendly methods of silicon purification, such as the FBR method.
Future Trends
The demand for high-purity silicon is expected to continue to grow in the future, driven by the increasing demand for electronics and renewable energy. As a result, there is a strong incentive to develop more efficient and environmentally friendly methods of silicon purification. In particular, the FBR method and other new technologies are expected to play a significant role in the future of silicon purification.