Process simulation
Introduction
Process simulation is a model-based representation of chemical, physical, biological, and other technical processes and unit operations in software. It allows the user to simulate an actual process in real-time and study the model's behavior under different process conditions. This method is used extensively in process design, process development, process optimization, and process operations read more.
Overview
Process simulation is a powerful tool used in both the design and operation of chemical processes. It provides a detailed mathematical model of a chemical plant or process, which can be used to analyze the system and predict how changes in the process conditions will affect the overall performance of the plant. This allows engineers to optimize the design and operation of the plant, resulting in significant cost savings and improved process safety read more.
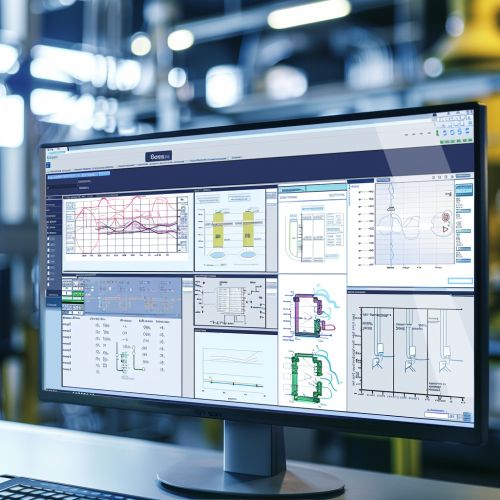
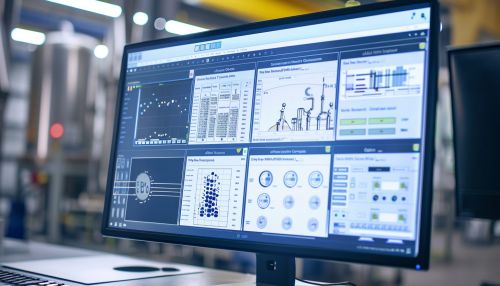
History
The concept of process simulation has its roots in the chemical engineering discipline, but its use has expanded to other industries such as petroleum refining, pharmaceutical manufacturing, and food processing. The development of process simulation software began in the 1960s with the advent of digital computers. Early simulation software was primarily used for process design and optimization. However, as the power of computers increased, the capabilities of process simulation software also expanded, allowing for more complex and accurate models to be developed.
Types of Process Simulation
There are several types of process simulation, each with its own strengths and weaknesses. These include steady-state simulation, dynamic simulation, and discrete event simulation.
Steady-State Simulation
Steady-state simulation is the most common type of process simulation. It assumes that the process is in a steady state, meaning that the conditions in the process do not change over time. This type of simulation is particularly useful in the design phase of a process, as it allows engineers to evaluate the performance of the process under a variety of conditions.
Dynamic Simulation
Dynamic simulation, on the other hand, allows for the simulation of processes that change over time. This is particularly useful in the operation phase of a process, as it allows operators to predict how changes in the process conditions will affect the performance of the plant. Dynamic simulation can also be used to simulate the startup and shutdown of a process, as well as any disturbances that may occur during operation.
Discrete Event Simulation
Discrete event simulation is a type of process simulation that is particularly useful in the design and operation of batch processes. It allows for the simulation of processes that are driven by discrete events, such as the arrival of a batch of material or the completion of a unit operation. This type of simulation is particularly useful in the pharmaceutical and food processing industries, where batch processes are common.
Applications of Process Simulation
Process simulation is used in a variety of applications, including process design, process optimization, and process operations.
Process Design
In the design phase of a process, simulation can be used to evaluate the performance of different process configurations and select the best one. This can significantly reduce the time and cost associated with process design, as it allows for the evaluation of different designs without the need for physical prototypes.
Process Optimization
Once a process has been designed, simulation can be used to optimize its performance. This can involve adjusting the process conditions to maximize the yield of a desired product, minimize the consumption of raw materials, or minimize the production of waste products.
Process Operations
In the operation phase of a process, simulation can be used to predict how changes in the process conditions will affect the performance of the plant. This can allow operators to make informed decisions about how to operate the plant, resulting in improved process safety and efficiency.
Process Simulation Software
There are many different process simulation software packages available, each with its own strengths and weaknesses. Some of the most popular include Aspen Plus, HYSYS, Pro/II, and CHEMCAD. These software packages provide a wide range of capabilities, including steady-state and dynamic simulation, process optimization, and process design.
Conclusion
Process simulation is a powerful tool that can significantly improve the design and operation of chemical processes. By providing a detailed mathematical model of a process, it allows engineers to analyze the system and predict how changes in the process conditions will affect the overall performance of the plant. This can result in significant cost savings and improved process safety.