Powder metallurgy
Introduction
Powder metallurgy is a term that refers to the process of creating metal objects from powdered metal. This process is used in a variety of industries, including automotive, aerospace, and electronics. The process involves the use of heat and pressure to form the powdered metal into a solid object. The resulting objects can have properties that are superior to those made from solid metal, including increased strength and durability.
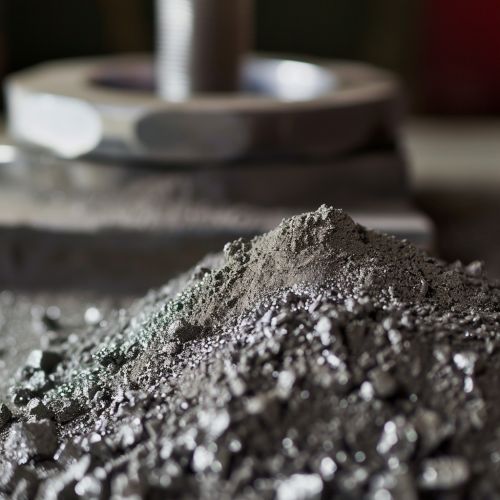
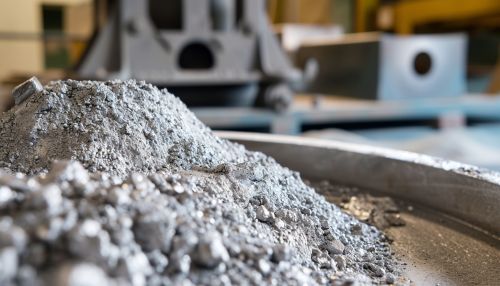
History
The history of powder metallurgy dates back to ancient times, with evidence of its use found in various cultures around the world. The Egyptians, for example, used powder metallurgy to create jewelry and decorative items. The Greeks and Romans also used this process to create weapons and armor. In the Middle Ages, powder metallurgy was used to create items such as coins and religious artifacts.
In the 19th century, powder metallurgy began to be used in industrial applications. The development of industrial machinery and equipment made it possible to produce powdered metal on a large scale, and the process was used to create items such as tools and machine parts.
In the 20th century, advances in technology led to the development of new methods for powder metallurgy. These methods allowed for the creation of more complex and intricate objects, and the process became increasingly popular in industries such as automotive and aerospace. Today, powder metallurgy is a vital part of many industries, and continues to be a subject of research and development.
Process
The process of powder metallurgy involves several steps. The first step is the creation of the metal powder. This can be done through a variety of methods, including atomization, mechanical alloying, and chemical reduction. The choice of method depends on the type of metal being used and the desired properties of the final product.
Once the metal powder has been created, it is then formed into the desired shape. This is typically done through a process known as compaction, in which the powder is placed into a mold and subjected to high pressure. The resulting object, known as a green compact, is then heated in a process known as sintering. This causes the particles of metal to bond together, forming a solid object.
The final step in the process is finishing, in which the object is polished and any necessary additional processing is carried out. This can include processes such as machining, heat treating, and coating.
Applications
Powder metallurgy is used in a wide range of applications. In the automotive industry, it is used to create parts such as gears, bearings, and engine components. In the aerospace industry, it is used to create components for aircraft and spacecraft. In the electronics industry, it is used to create components for devices such as computers and smartphones.
One of the main advantages of powder metallurgy is that it allows for the creation of objects with complex shapes and intricate details. This makes it ideal for applications where precision and detail are important. Additionally, the process allows for the creation of objects with properties that are superior to those made from solid metal, including increased strength and durability.
Advantages and Disadvantages
Like any manufacturing process, powder metallurgy has its advantages and disadvantages. One of the main advantages is that it allows for the creation of objects with complex shapes and intricate details. This makes it ideal for applications where precision and detail are important. Additionally, the process allows for the creation of objects with properties that are superior to those made from solid metal, including increased strength and durability.
However, there are also some disadvantages to powder metallurgy. One of the main disadvantages is the cost. The process can be expensive, particularly when it comes to the creation of complex objects. Additionally, the process can be time-consuming, particularly when it comes to the sintering stage.
Future Developments
The field of powder metallurgy is constantly evolving, with new developments and innovations being made on a regular basis. One area of research is the development of new materials for use in the process. This includes the development of new types of metal powders, as well as the development of new types of binders and lubricants.
Another area of research is the development of new methods for the compaction and sintering stages of the process. This includes the development of new types of equipment and machinery, as well as the development of new techniques and methods for applying heat and pressure.