Modern Engineering for Design of Liquid-Propellant Rocket Engines by Dieter K. Huzel (1992)
Introduction
Modern Engineering for Design of Liquid-Propellant Rocket Engines by Dieter K. Huzel, published in 1992, is a seminal work in the field of rocket propulsion. This comprehensive text delves into the intricate details of liquid-propellant rocket engines, providing an in-depth analysis of their design, development, and operational principles. The book is widely regarded as an essential resource for aerospace engineers, researchers, and students specializing in rocket propulsion systems.
Historical Context
The development of liquid-propellant rocket engines has a rich history, dating back to the early 20th century. The pioneering work of Robert H. Goddard and the subsequent advancements during World War II, particularly the development of the V-2 rocket by Wernher von Braun, laid the foundation for modern rocket propulsion. By the time Huzel's book was published in 1992, the field had seen significant advancements, including the development of engines for the Saturn V rocket and the Space Shuttle.
Fundamental Concepts
Propellant Types
Liquid-propellant rocket engines utilize two primary types of propellants: oxidizers and fuels. Common oxidizers include liquid oxygen (LOX) and nitrogen tetroxide (N2O4), while typical fuels include RP-1 (a refined form of kerosene) and liquid hydrogen (LH2). The choice of propellant combination significantly impacts the engine's performance, efficiency, and operational characteristics.
Thrust and Specific Impulse
Thrust is the force generated by the rocket engine to propel the vehicle forward. It is a function of the mass flow rate of the propellants and the exhaust velocity. Specific impulse (Isp) is a critical performance metric, representing the efficiency of the engine. It is defined as the thrust produced per unit weight flow rate of the propellant and is typically measured in seconds.
Design Principles
Combustion Chamber
The combustion chamber is where the propellants are mixed and burned to produce high-temperature, high-pressure gases. The design of the combustion chamber must ensure efficient mixing and combustion of the propellants while withstanding extreme thermal and mechanical stresses. Key parameters include chamber pressure, temperature, and the characteristic length (L*), which influences combustion efficiency.
Nozzle Design
The nozzle converts the thermal energy of the combustion gases into kinetic energy, producing thrust. The most common nozzle design is the de Laval nozzle, which features a converging section, a throat, and a diverging section. The nozzle's expansion ratio, defined as the ratio of the exit area to the throat area, is a critical parameter that affects the engine's performance, particularly at different altitudes.
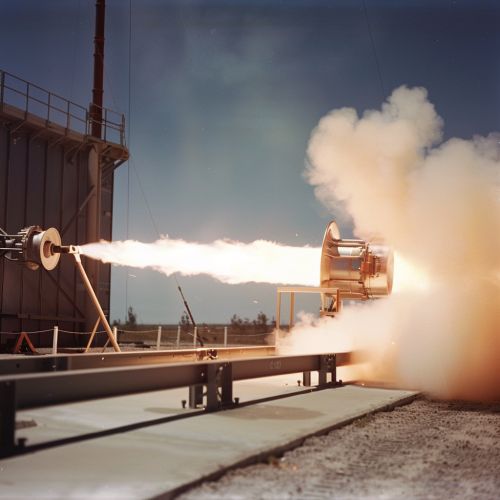
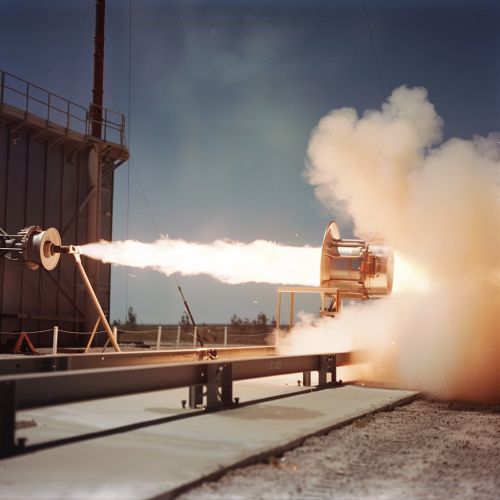
Cooling Systems
Cooling is essential to prevent the combustion chamber and nozzle from overheating. Various cooling methods are employed, including regenerative cooling, where the propellant is circulated through channels in the chamber walls before being injected into the combustion chamber. Other methods include film cooling and ablative cooling, each with its advantages and trade-offs.
Propellant Feed Systems
Pressure-Fed Systems
In pressure-fed systems, the propellants are stored in tanks pressurized by an inert gas, typically helium. This pressure forces the propellants into the combustion chamber. While simpler and more reliable, pressure-fed systems are generally limited to lower thrust levels due to the weight and volume of the pressurization system.
Pump-Fed Systems
Pump-fed systems use turbopumps to deliver propellants to the combustion chamber at high pressures. These systems are more complex but allow for higher thrust levels and better performance. The design of turbopumps involves considerations of rotordynamics, cavitation, and thermal management.
Engine Cycles
Gas Generator Cycle
In the gas generator cycle, a portion of the propellants is burned in a gas generator to drive the turbopumps. The exhaust gases are then expelled overboard, not contributing to the thrust. This cycle is relatively simple and reliable but less efficient than other cycles.
Staged Combustion Cycle
The staged combustion cycle, also known as the closed cycle, burns all the propellants in the combustion chamber. A preburner partially burns the propellants to drive the turbopumps, and the resulting hot gases are fed into the main combustion chamber. This cycle offers higher efficiency and performance but is more complex and challenging to develop.
Expander Cycle
In the expander cycle, the fuel is used to cool the combustion chamber and nozzle, absorbing heat and vaporizing. The vaporized fuel then drives the turbopumps before being injected into the combustion chamber. This cycle is typically used with cryogenic fuels like liquid hydrogen and is known for its high efficiency and simplicity.
Materials and Manufacturing
The materials used in liquid-propellant rocket engines must withstand extreme conditions, including high temperatures, pressures, and corrosive environments. Common materials include nickel-based superalloys, titanium, and carbon-carbon composites. Advanced manufacturing techniques, such as additive manufacturing (3D printing), are increasingly being used to produce complex engine components with improved performance and reduced weight.
Testing and Validation
The development of liquid-propellant rocket engines involves extensive testing and validation to ensure reliability and performance. This includes component-level testing, such as turbopump tests and combustion chamber tests, as well as full-scale engine tests. Ground testing is typically conducted on test stands, where engines are fired in controlled conditions to gather data on thrust, specific impulse, and other performance metrics.
Applications
Liquid-propellant rocket engines are used in a wide range of applications, from launch vehicles to spacecraft propulsion systems. Notable examples include the RS-25 engines used on the Space Shuttle and the Merlin engines used on SpaceX's Falcon 9 rockets. These engines play a critical role in enabling space exploration, satellite deployment, and interplanetary missions.
Future Trends
The field of liquid-propellant rocket engines continues to evolve, with ongoing research focused on improving performance, reliability, and cost-effectiveness. Emerging technologies, such as electric propulsion and nuclear thermal propulsion, offer the potential for significant advancements in space travel. Additionally, efforts to develop reusable rocket engines aim to reduce the cost of access to space, making space exploration more sustainable and accessible.
See Also
- Rocket Propulsion
- Combustion Chamber
- Turbopump
- Specific Impulse
- De Laval Nozzle
- Additive Manufacturing
- Electric Propulsion
- Nuclear Thermal Propulsion
References
- Huzel, Dieter K. Modern Engineering for Design of Liquid-Propellant Rocket Engines. 1992.