Inventory Management
Overview
Inventory Management is a systematic approach to sourcing, storing, and selling inventory—both raw materials (components) and finished goods (products). In business terms, inventory management means the right stock, at the right levels, in the right place, at the right time, and at the right cost as well as price.
Importance of Inventory Management
Inventory management is a critical management aspect in companies as it relates to the balancing of costs and benefits of inventory, including the cost of holding, ordering, and shortage costs. The objective of inventory management is to provide uninterrupted production, sales, and/or customer-service levels at the minimum cost. Since for many companies, inventory is the largest item in the current assets category, inventory problems can and do contribute to losses or even business failures.
Types of Inventory
There are mainly four types of inventory: raw material, work-in-progress, finished goods, and MRO goods inventory.
Raw Material
Raw Material is the unprocessed material that is used to produce the final product. For a furniture maker, raw material inventory might include lumber, hardware, and paint.
Work-in-Progress
Work-in-Progress (WIP) inventory includes all materials that have begun their transformation process from raw materials to finished goods. In the furniture maker example, a chair that has been assembled but not yet painted would be considered work-in-progress inventory.
Finished Goods
Finished Goods inventory consists of completed products that are ready for sale. For the furniture maker, a chair that has been assembled, painted, and is ready for sale would be considered finished goods inventory.
MRO Goods Inventory
MRO Goods (Maintenance, Repair, and Operations) inventory includes items used in support of general operations and maintenance such as cleaning supplies, lubricants, and office supplies.
Inventory Management Techniques
There are several techniques of inventory management that can help businesses effectively manage their inventory. These include the Economic Order Quantity (EOQ) model, ABC analysis, Just-in-Time (JIT) inventory, and safety stock.
Economic Order Quantity (EOQ)
The Economic Order Quantity (EOQ) is the number of units that a company should add to inventory with each order to minimize the total costs of inventory—such as holding costs, order costs, and shortage costs. The EOQ provides a model for calculating the appropriate reorder point and the optimal reorder quantity to ensure the instantaneous replenishment of inventory with no shortages.
ABC Analysis
ABC Analysis is an inventory categorization technique often used in materials management. It is also known as Selective Inventory Control. ABC analysis divides an inventory into three categories—"A" items with very tight control and accurate records, "B" items with less tightly controlled and good records, and "C" items with the simplest controls possible and minimal records.
Just-in-Time (JIT) Inventory
Just-in-Time (JIT) inventory management is a strategy that aligns raw-material orders from suppliers directly with production schedules. Companies employ this inventory strategy to increase efficiency and decrease waste by receiving goods only as they need them for the production process, which reduces inventory costs.
Safety Stock
Safety Stock is a term used by logisticians to describe a level of extra stock that is maintained to mitigate risk of stockouts (shortfall in raw material or packaging) caused by uncertainties in supply and demand.
Inventory Management Systems
Inventory management systems track goods through the entire supply chain or the portion of it a business operates in. That covers everything from production to retail, warehousing to shipping, and all the movements of stock and parts between.
Manual Systems
While most businesses start out with manual methods of inventory control, such as spreadsheets, these systems can quickly become cumbersome as the business grows. Manual systems are prone to errors and can be time-consuming.
Automated Systems
Automated Systems for inventory management involve the use of technological tools and software applications to track inventory levels, orders, sales, and deliveries. Automated systems can provide real-time and accurate inventory tracking, reduce the time and costs invested in manual inventory management, and allow businesses to make informed decisions about inventory operations.
Challenges in Inventory Management
While inventory management is crucial for the smooth functioning of any business, it can present several challenges. These include maintaining a balance between supply and demand, managing the costs associated with holding inventory, ensuring the accuracy of inventory records, and managing the risks associated with inventory.
Conclusion
Effective inventory management is crucial for any business that wants to keep its costs down and its customers happy. While it can be complex, the use of modern techniques and systems can greatly simplify the process, making it easier for businesses to manage their inventory effectively.
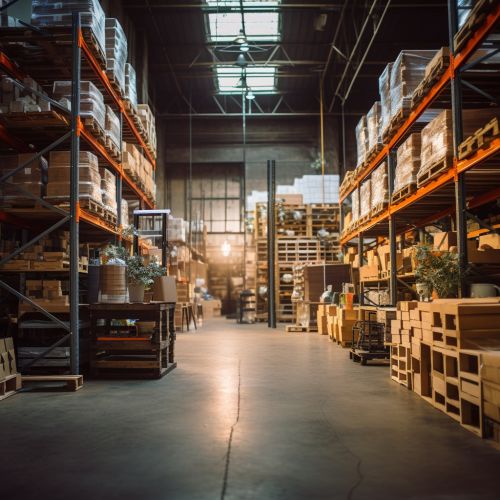
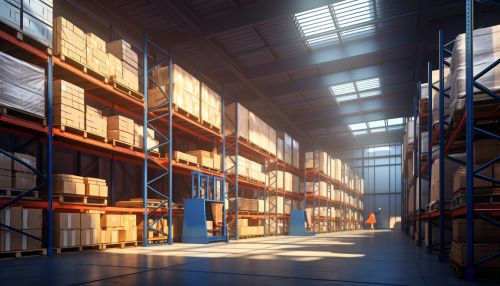