Gate valve
Introduction
A Gate valve is a type of valve used to control the flow of liquids or gases in a pipeline. It is one of the most commonly used valves in industrial applications due to its simplicity, reliability, and ability to handle high pressures and temperatures.
Design and Operation
The gate valve consists of a body, a bonnet, a gate, and a stem. The body houses the flow path and the gate, which is a flat or wedge-shaped disk that moves up and down to control the flow. The stem connects the gate to the handwheel or actuator, which is used to operate the valve.
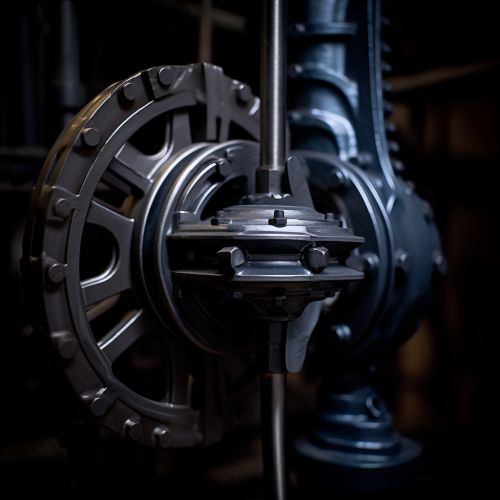
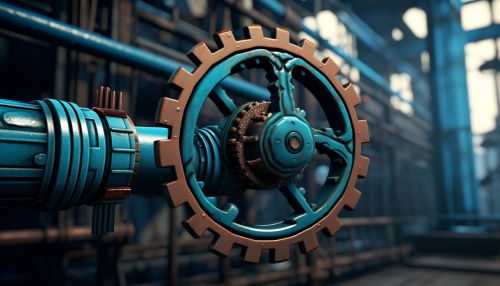
The operation of a gate valve is simple. When the handwheel or actuator is turned in one direction, the stem moves the gate down to close the flow path. Turning the handwheel or actuator in the opposite direction moves the gate up, opening the flow path. This is known as a rising stem design. In a non-rising stem design, the stem stays stationary while the gate moves up and down.
Types of Gate Valves
There are several types of gate valves, each with its own advantages and disadvantages. The most common types are the solid wedge, flexible wedge, and split wedge or double-disc gate valves.
Solid Wedge Gate Valve
The solid wedge gate valve has a single-piece gate that is robust and simple. It is suitable for almost all types of fluids and is widely used in a variety of applications.
Flexible Wedge Gate Valve
The flexible wedge gate valve has a two-piece gate that can flex slightly to compensate for changes in the pipeline's internal diameter due to temperature fluctuations or pressure changes. This makes it suitable for applications where thermal expansion or contraction of the pipeline is a concern.
Split Wedge or Double-Disc Gate Valve
The split wedge or double-disc gate valve has a two-piece gate that can move independently. This allows it to seal more effectively against the valve seats, making it suitable for applications where tight sealing is required.
Applications
Gate valves are used in a wide range of applications, including oil and gas production, chemical processing, power generation, water and wastewater treatment, and many others. They are suitable for both on-off control and throttling service, although they are primarily used for on-off control.
Advantages and Disadvantages
Gate valves have several advantages. They provide a straight-through, unobstructed flow path, which results in very low pressure loss. They are also capable of handling high pressures and temperatures, and they can be used with a wide variety of fluids, including corrosive and abrasive ones.
However, gate valves also have some disadvantages. They are generally slower to operate than other types of valves, and they can be more prone to leakage if not properly maintained. In addition, the gate and seats can be damaged if the valve is frequently opened and closed, or if it is used for throttling service.
Maintenance and Troubleshooting
Like all mechanical devices, gate valves require regular maintenance to ensure their proper operation and longevity. This typically involves periodic inspection, cleaning, and replacement of worn or damaged parts.
If a gate valve is not operating properly, troubleshooting may be required to identify and correct the problem. Common issues include leakage, difficulty in operation, and failure to fully open or close.
Conclusion
Gate valves are a vital component in many industrial processes. Their simple design, reliability, and ability to handle a wide range of conditions make them a popular choice for controlling the flow of liquids and gases. However, like all mechanical devices, they require proper maintenance and operation to ensure their longevity and performance.