Fatigue Testing
Introduction
Fatigue testing is a method used in materials science to assess the durability and longevity of materials under cyclic loading conditions. This process helps to determine the fatigue limit or endurance limit of a material, which is the maximum stress level a material can withstand for an infinite number of cycles without failure.
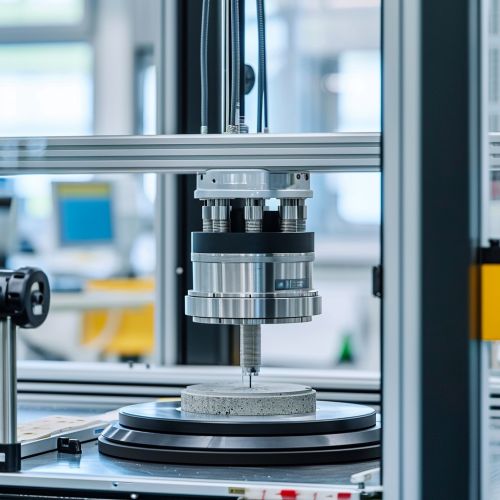
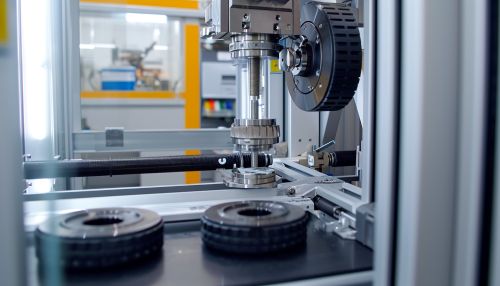
Types of Fatigue Testing
There are several types of fatigue testing, each designed to simulate different types of loading conditions that a material may experience in real-world applications.
High Cycle Fatigue Testing
High cycle fatigue (HCF) testing is used to evaluate the behavior of materials subjected to a large number of cycles at relatively low stress levels. This type of testing is typically used for materials that are expected to endure millions of cycles in their lifetime, such as engine components or turbine blades.
Low Cycle Fatigue Testing
Low cycle fatigue (LCF) testing, on the other hand, is used to evaluate materials that are subjected to high stress levels for a relatively small number of cycles. This type of testing is commonly used for materials in structures that experience significant stress levels, such as bridges or buildings.
Thermomechanical Fatigue Testing
Thermomechanical fatigue (TMF) testing involves subjecting a material to cyclic mechanical loading and cyclic thermal loading simultaneously. This type of testing is used to simulate the conditions experienced by materials in high-temperature environments, such as jet engines or power plants.
Fatigue Testing Procedures
The procedures for fatigue testing can vary depending on the type of material being tested and the specific application. However, there are some general steps that are commonly followed in most fatigue testing procedures.
Sample Preparation
The first step in any fatigue testing procedure is to prepare the material samples. This typically involves cutting the material into a specific shape and size, and then polishing the surface to remove any surface defects that could affect the test results.
Test Setup
Once the samples are prepared, they are mounted in a fatigue testing machine. The machine is then calibrated to apply a specific type of cyclic loading to the sample, such as tension, compression, bending, or torsion.
Data Collection
During the test, data is collected on the number of cycles the material can withstand before failure, as well as the stress levels at which failure occurs. This data is then used to create a S-N curve, which plots the stress levels against the number of cycles to failure.
Factors Affecting Fatigue Life
Several factors can affect the fatigue life of a material, including the type of material, the loading conditions, the environment, and the presence of defects.
Material Type
Different materials have different fatigue properties. For example, metals typically have a well-defined fatigue limit, while most polymers do not. The microstructure of the material can also affect its fatigue life. For example, materials with a fine grain size typically have a higher fatigue resistance than materials with a coarse grain size.
Loading Conditions
The type of loading applied to a material can significantly affect its fatigue life. For example, materials subjected to fully reversed loading (where the stress alternates between tension and compression) typically have a shorter fatigue life than materials subjected to pulsating loading (where the stress is always in one direction).
Environment
The environment in which a material is used can also affect its fatigue life. For example, materials used in corrosive environments typically have a shorter fatigue life due to the additional damage caused by the corrosion process.
Defects
Defects in a material, such as cracks or inclusions, can act as stress concentrators and significantly reduce the fatigue life of the material.
Applications of Fatigue Testing
Fatigue testing is used in a wide range of industries to ensure the safety and reliability of products and structures. Some of the main applications of fatigue testing include:
Aerospace Industry
In the aerospace industry, fatigue testing is used to evaluate the durability of aircraft components, such as engine parts, wings, and fuselage structures. This helps to ensure the safety of the aircraft and its passengers.
Automotive Industry
In the automotive industry, fatigue testing is used to assess the durability of various car components, such as engine parts, suspension systems, and body structures. This helps to ensure the reliability of the vehicle and the safety of its occupants.
Construction Industry
In the construction industry, fatigue testing is used to evaluate the durability of building materials and structures, such as bridges and high-rise buildings. This helps to ensure the safety and longevity of the structures.