Engineered Wood
Introduction
Engineered wood, also known as composite wood, man-made wood, or manufactured board, encompasses a range of derivative wood products which are manufactured by binding or fixing the strands, particles, fibers, veneers, or boards of wood, together with adhesives, or other methods of fixation to form composite materials. These products are engineered to precise design specifications which are tested to meet national or international standards.
Types of Engineered Wood
Engineered wood products are categorized based on their manufacturing process and the type of wood used. The primary types include:
Plywood
Plywood is made from thin layers or "plies" of wood veneer that are glued together with adjacent layers having their wood grain rotated up to 90 degrees to one another. This cross-graining technique reduces the wood's tendency to split when nailed at the edges, reduces expansion and shrinkage, and makes the strength of the panel consistent in all directions.
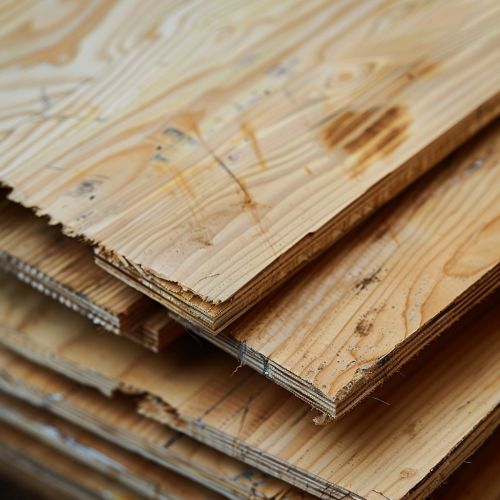
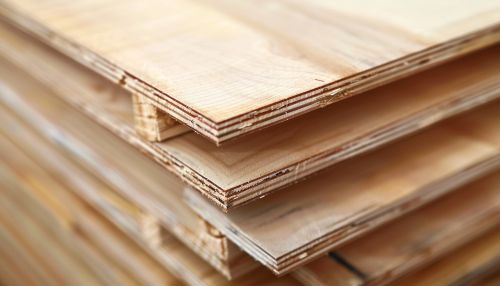
Oriented Strand Board (OSB)
Oriented Strand Board (OSB) is a type of engineered wood similar to particle board, formed by adding adhesives and then compressing layers of wood strands (flakes) in specific orientations. OSB is a material with favorable mechanical properties that make it particularly suitable for load-bearing applications in construction.
Medium-Density Fiberboard (MDF)
Medium-Density Fiberboard (MDF) is an engineered wood product made by breaking down hardwood or softwood residuals into wood fibers, often in a defibrator, combining it with wax and a resin binder, and forming panels by applying high temperature and pressure. MDF is denser than plywood and can be used for a variety of applications including furniture and cabinetry.
Particle Board
Particle board, also known as chipboard, is an engineered wood product manufactured from wood chips, sawmill shavings, or even sawdust, and a synthetic resin or other suitable binder, which is pressed and extruded. Particle board is cheaper, denser, and more uniform than conventional wood and plywood and is used in furniture and building construction.
Laminated Veneer Lumber (LVL)
Laminated Veneer Lumber (LVL) is an engineered wood product that uses multiple layers of thin wood assembled with adhesives. It offers several advantages over traditional milled lumber: it is stronger, straighter, and more uniform. LVL is used for headers, beams, rimboard, and edge-forming material.
Cross-Laminated Timber (CLT)
Cross-Laminated Timber (CLT) is a wood panel product made from gluing layers of solid-sawn lumber together. Each layer of boards is oriented perpendicular to adjacent layers and glued on the wide faces of each board, usually in a symmetric way so that the outer layers have the same orientation. CLT is used for long spans and all assemblies, such as floors, walls, or roofs.
Manufacturing Process
The manufacturing process of engineered wood involves several steps, including the selection of raw materials, preparation, assembly, and finishing. The specific steps can vary depending on the type of engineered wood being produced.
Raw Material Selection
The first step in the manufacturing process is the selection of raw materials. This typically involves choosing the appropriate type of wood and ensuring that it meets the necessary quality standards. The wood is then processed to remove any defects and to ensure that it is of uniform size and shape.
Preparation
Once the raw materials have been selected, they are prepared for assembly. This can involve a variety of processes, such as drying, cutting, and shaping. The goal is to ensure that the wood is in the best possible condition for the next stage of the process.
Assembly
The assembly process involves combining the prepared wood materials with adhesives or other binding agents. This can be done in a variety of ways, depending on the type of engineered wood being produced. For example, in the case of plywood, thin layers of wood veneer are glued together with their grains oriented in different directions. In the case of particle board, wood chips are mixed with a binder and then pressed into sheets.
Finishing
The final step in the manufacturing process is finishing. This can involve a variety of processes, such as sanding, painting, or coating. The goal is to ensure that the finished product meets the necessary quality standards and is ready for use.
Applications
Engineered wood products are used in a wide variety of applications, including construction, furniture, and cabinetry. Their versatility, strength, and cost-effectiveness make them a popular choice for many different types of projects.
Construction
In construction, engineered wood products are used for a variety of purposes, including framing, flooring, and roofing. They are often used in place of traditional lumber because they are stronger, more uniform, and less prone to warping or splitting.
Furniture
Engineered wood products are also commonly used in the manufacture of furniture. They are often used for the structural components of furniture, such as frames and supports, as well as for decorative elements, such as veneers and laminates.
Cabinetry
In cabinetry, engineered wood products are used for both structural and decorative purposes. They are often used for the carcasses of cabinets, as well as for doors, drawers, and other components.
Environmental Impact
The environmental impact of engineered wood products can vary depending on a variety of factors, including the type of wood used, the manufacturing process, and the end use of the product. In general, engineered wood products are considered to be more environmentally friendly than traditional lumber because they make use of wood that might otherwise go to waste.
Resource Efficiency
One of the main environmental benefits of engineered wood products is their resource efficiency. Because they are made from smaller pieces of wood, they can make use of wood that might otherwise be discarded. This can help to reduce the demand for new timber and to minimize the amount of waste generated by the wood industry.
Energy Use
The manufacturing process for engineered wood products can be energy-intensive, particularly in the case of products that require high temperatures and pressures. However, advances in technology and manufacturing processes have helped to reduce the energy requirements for many types of engineered wood.
Carbon Footprint
The carbon footprint of engineered wood products can vary depending on a variety of factors, including the type of wood used, the manufacturing process, and the transportation of the finished product. In general, engineered wood products are considered to have a lower carbon footprint than traditional lumber because they make use of wood that might otherwise go to waste.
Advantages and Disadvantages
Engineered wood products offer a number of advantages over traditional lumber, but they also have some disadvantages. Understanding these can help to determine the best use for these materials.
Advantages
- **Strength and Durability**: Engineered wood products are often stronger and more durable than traditional lumber. This is because they are manufactured to precise specifications and are less prone to defects such as knots and splits.
- **Versatility**: Engineered wood products can be used in a wide variety of applications, from construction to furniture to cabinetry. They can also be manufactured in a wide range of sizes and shapes, making them suitable for many different types of projects.
- **Cost-Effectiveness**: Engineered wood products are often more cost-effective than traditional lumber. This is because they make use of smaller pieces of wood that might otherwise go to waste, and because they can be manufactured to precise specifications, reducing the need for additional processing.
Disadvantages
- **Environmental Impact**: While engineered wood products are generally considered to be more environmentally friendly than traditional lumber, they can still have a significant environmental impact. This is particularly true in the case of products that require high temperatures and pressures for their manufacture.
- **Chemical Use**: The adhesives and other binding agents used in the manufacture of engineered wood products can contain chemicals that may be harmful to human health and the environment. This is particularly true in the case of formaldehyde-based adhesives, which can off-gas over time.
- **Aesthetic Limitations**: Engineered wood products can sometimes lack the natural beauty and character of traditional lumber. This can be a disadvantage in applications where the appearance of the wood is important.
Future Trends
The future of engineered wood products looks promising, with a number of trends and developments that are likely to shape the industry in the coming years.
Sustainable Practices
One of the most significant trends in the engineered wood industry is the move towards more sustainable practices. This includes the use of more environmentally friendly adhesives and binding agents, as well as the development of new manufacturing processes that reduce energy use and waste.
Advanced Technologies
Advances in technology are also likely to play a significant role in the future of engineered wood products. This includes the development of new materials and manufacturing processes, as well as the use of advanced computer modeling and simulation techniques to optimize the design and performance of engineered wood products.
Market Growth
The market for engineered wood products is expected to continue to grow in the coming years, driven by increasing demand for sustainable building materials and the continued development of new and innovative products. This growth is likely to be particularly strong in emerging markets, where the demand for construction materials is high.