Electrospinning
Introduction
Electrospinning is a fiber production method which uses electric force to draw charged threads of polymeric solutions or polymer melts up to fiber diameters in the order of some hundred nanometers. Electrospinning shares characteristics of both electrospraying and conventional solution dry spinning of fibers. The process does not require the use of coagulation chemistry or high temperatures to produce solid threads from solution. This makes the process particularly suited to the production of fibers using large and complex molecules.
History
The basic concept of electrospinning has been known and patented since the early 20th century, particularly in the textile industry. The technique was first patented by Formhals in 1934, who aimed to produce textile yarns at higher speeds and lower costs than traditional methods. However, due to the lack of understanding of the underlying principles and the absence of suitable materials and equipment, electrospinning did not gain significant attention until the late 20th century.
Principle
The principle of electrospinning is relatively simple. A high voltage is used to create an electrically charged jet of polymer solution or melt, which dries or solidifies to leave a polymer fiber. The fiber diameter can be easily controlled by adjusting the processing conditions, such as the voltage, the concentration of the solution, and the distance between the needle and the collector.
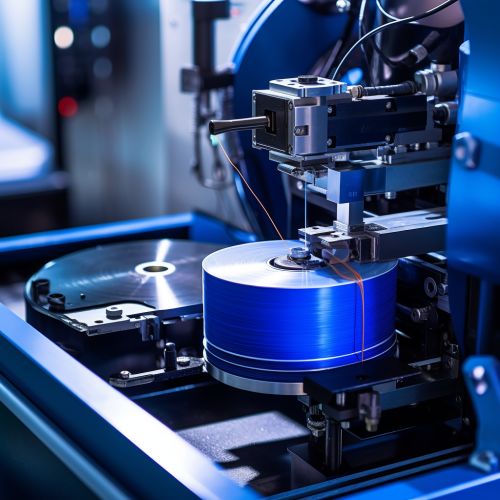
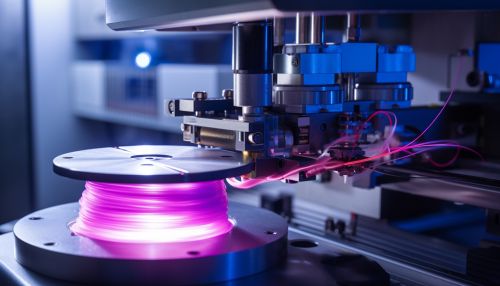
Materials
A wide range of materials can be electrospun, including polymers, composites, and ceramics. The choice of material depends on the intended application of the fibers. For example, biodegradable polymers are often used for medical applications, while ceramics can be used for filtration or catalysis.
Applications
Electrospun fibers have a wide range of potential applications, including in tissue engineering, drug delivery, filtration, protective clothing, and sensors. The high surface area to volume ratio and the high porosity of electrospun materials make them ideal for these applications.
Process Parameters
The electrospinning process is influenced by several parameters, which can be divided into three main categories: solution properties, process conditions, and ambient conditions. Solution properties include the type of polymer, the concentration of the solution, and the solvent used. Process conditions include the applied voltage, the flow rate of the solution, and the distance between the needle and the collector. Ambient conditions include the temperature and humidity of the environment.
Equipment
The basic equipment for electrospinning includes a high voltage power supply, a syringe pump, a metal needle, and a collector. More advanced setups may include a climate control chamber, a rotating collector for producing aligned fibers, or a coaxial needle for producing core-shell or hollow fibers.
Challenges and Future Directions
Despite the many advantages of electrospinning, there are also several challenges that need to be overcome. These include the difficulty of producing large quantities of fibers, the need for high voltages, and the use of toxic solvents. Future research is likely to focus on addressing these challenges and expanding the range of materials that can be electrospun.