Electroplating
Introduction
Electroplating is a process that uses an electric current to reduce dissolved metal cations so that they form a thin coherent metal coating on an electrode. The term is also used for electrical oxidation of anions on to a solid substrate, as in the formation of silver chloride on silver wire to make silver/silver-chloride electrodes. Electroplating is primarily used to change the surface properties of an object (such as abrasion and wear resistance, corrosion protection, lubricity, aesthetic qualities), but may also be used to build up thickness on undersized parts or to form objects by electroforming.
History
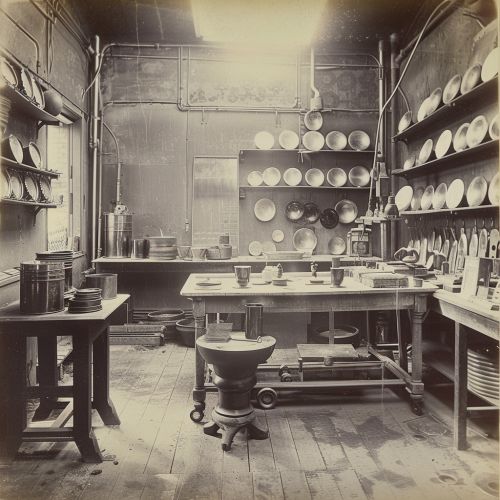
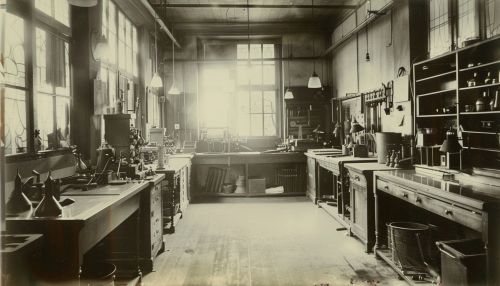
The process of electroplating was first discovered in 1805 by Italian chemist Luigi Brugnatelli. He used the method of electrodeposition to apply a layer of gold onto silver medals, using a voltaic pile as a source of electricity. However, his work was suppressed by the French Academy of Sciences and did not receive public recognition or support until the mid-19th century.
Process
The electroplating process involves several steps. First, the object to be plated is thoroughly cleaned to remove any dirt, grease, or oxidation. This is typically done through a series of chemical baths and rinses. Following this, the object is submerged in a solution containing a salt of the metal to be plated. An electric current is then passed through the solution, causing the metal ions to be reduced and deposit onto the object, forming a thin layer of metal.
Applications
Electroplating has a wide range of applications in various industries. In the electronics industry, it is used to plate connectors and components for improved conductivity and corrosion resistance. In the automotive industry, electroplating is used to coat parts such as brake pistons and heat sinks to improve their performance and longevity. In the jewelry industry, electroplating is commonly used to apply thin layers of precious metals onto less expensive metals to provide the appearance of the more costly material.
Types of Electroplating
There are several types of electroplating processes, each suited to different applications. These include:
Hard Gold Plating
Hard gold plating is a method of depositing a thin layer of gold onto the surface of another metal, most often copper or silver, by chemical or electrochemical plating. This method is primarily used in the electronics industry due to the superior conductivity and corrosion resistance of gold.
Silver Plating
Silver plating is the process of depositing a layer of silver onto a surface. This is often used in the manufacturing of jewelry and tableware, as well as in certain industrial applications where high conductivity is required.
Nickel Plating
Nickel plating is a technique of electroplating a thin layer of nickel onto a metal object. Nickel plating is often used in the automotive and aerospace industries to improve corrosion resistance and wear resistance.
Copper Plating
Copper plating is the process of electrodepositing a layer of copper. This is often used in the electronics industry, where it is used to provide a conductive layer on the surface of printed circuit boards.
Advantages and Disadvantages
Like any industrial process, electroplating has its advantages and disadvantages. On the positive side, electroplating can greatly enhance the appearance and durability of objects. It can also be used to apply a variety of different metals, allowing for a high degree of customization. On the downside, electroplating requires a significant amount of energy and can produce harmful byproducts if not properly managed.
Environmental Impact
Electroplating can have a significant environmental impact if not properly managed. The process involves the use of potentially harmful chemicals, which can pose a risk to both human health and the environment if not handled correctly. However, with proper waste management and recycling practices, the environmental impact of electroplating can be minimized.
Future of Electroplating
The future of electroplating is likely to be influenced by advances in technology and environmental regulations. New methods of electroplating, such as pulse plating, are being developed that offer improved efficiency and environmental performance. At the same time, stricter environmental regulations are likely to drive the development of cleaner, more sustainable electroplating processes.