Drilled Shafts
Introduction
Drilled shafts, also known as caissons or bored piles, are deep foundation elements that are constructed by drilling a cylindrical hole into the ground and filling it with concrete. These structural elements are used to support heavy vertical loads and are commonly employed in the construction of bridges, buildings, and other large structures. Drilled shafts are particularly advantageous in situations where soil conditions are unsuitable for shallow foundations or where high load-bearing capacity is required.
History and Development
The concept of drilled shafts dates back to ancient times when early civilizations used rudimentary techniques to create deep foundations. However, modern drilled shaft technology began to develop in the early 20th century with the advent of more advanced drilling equipment and techniques. The introduction of rotary drilling rigs and the use of bentonite slurry to stabilize boreholes marked significant milestones in the evolution of drilled shaft construction.
Design Considerations
Designing drilled shafts involves a thorough understanding of geotechnical engineering principles and the specific site conditions. Key factors to consider include soil and rock properties, groundwater conditions, load requirements, and potential environmental impacts. The design process typically involves the following steps:
Site Investigation
A comprehensive geotechnical investigation is essential to determine the subsurface conditions. This may involve drilling exploratory boreholes, conducting soil and rock sampling, and performing in-situ tests such as the Standard Penetration Test (SPT) and Cone Penetration Test (CPT).
Load Analysis
The load-bearing capacity of a drilled shaft is influenced by both the end-bearing resistance at the shaft tip and the side friction along the shaft's length. Engineers must analyze the vertical loads, lateral loads, and moments that the shaft will be subjected to during its service life.
Shaft Dimensions
The diameter and length of the drilled shaft are critical design parameters. The diameter is typically determined based on the load requirements and the available drilling equipment, while the length is influenced by the depth of competent bearing strata and the need to penetrate through weak or compressible soils.
Reinforcement
Reinforcement is often required to enhance the structural capacity of the drilled shaft. This may include the use of steel rebar cages, which are lowered into the borehole before concrete placement. The reinforcement design must account for factors such as bending moments, shear forces, and potential seismic loads.
Construction Techniques
The construction of drilled shafts involves several key steps, each requiring careful execution to ensure the integrity and performance of the foundation element.
Drilling
Drilling is typically performed using rotary drilling rigs equipped with various types of drill bits, such as augers, core barrels, and rock drilling tools. The choice of drilling method depends on the subsurface conditions and the shaft diameter. In unstable soils, drilling fluids such as bentonite slurry or polymer-based fluids may be used to maintain borehole stability.
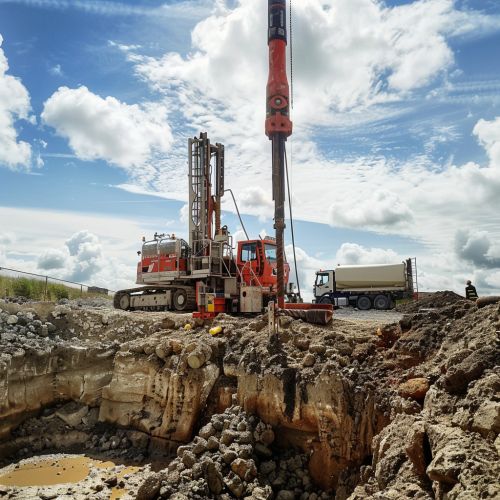
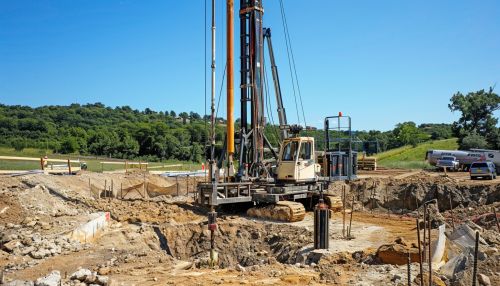
Excavation Support
In cases where the borehole walls are prone to collapse, temporary casing or slurry walls may be used to support the excavation. Temporary casing involves inserting a steel tube into the borehole, which is later removed after concrete placement. Slurry walls use a stabilizing fluid to maintain borehole integrity during drilling.
Concrete Placement
Concrete is placed into the borehole using a tremie pipe or a concrete pump to prevent segregation and ensure uniform filling. The concrete mix design must be carefully controlled to achieve the desired strength and workability. In some cases, additives such as superplasticizers or retarders may be used to improve the concrete's performance.
Quality Control
Quality control measures are essential to verify the integrity and performance of the drilled shaft. This may include non-destructive testing methods such as sonic logging, crosshole sonic logging, or low-strain integrity testing. Additionally, load tests may be conducted to confirm the shaft's load-bearing capacity.
Applications
Drilled shafts are used in a wide range of construction projects due to their versatility and high load-bearing capacity. Some common applications include:
Bridge Foundations
Drilled shafts are often used to support bridge piers and abutments, particularly in situations where deep foundations are required to reach competent bearing strata. They are well-suited for use in river crossings and other challenging environments.
Building Foundations
In urban areas with limited space and high load demands, drilled shafts provide an effective solution for supporting tall buildings and other heavy structures. They can be installed with minimal disruption to surrounding structures and infrastructure.
Retaining Structures
Drilled shafts can be used to construct retaining walls and other earth retention systems. They provide lateral support to slopes and excavations, preventing soil movement and ensuring stability.
Marine Structures
Drilled shafts are commonly used in the construction of marine structures such as docks, piers, and offshore platforms. Their ability to penetrate through soft sediments and reach stable bearing layers makes them ideal for use in coastal and offshore environments.
Advantages and Limitations
Advantages
- High Load-Bearing Capacity: Drilled shafts can support significant vertical and lateral loads, making them suitable for heavy structures.
- Versatility: They can be used in a variety of soil and rock conditions, including soft clays, dense sands, and hard rock.
- Minimal Vibration: The construction process generates minimal vibration, reducing the risk of damage to adjacent structures.
- Flexibility: Drilled shafts can be installed in confined spaces and challenging environments, such as urban areas and water bodies.
Limitations
- Cost: The construction of drilled shafts can be more expensive than other foundation types due to the specialized equipment and techniques required.
- Construction Time: The installation process can be time-consuming, particularly in difficult ground conditions.
- Quality Control: Ensuring the integrity of the shaft requires rigorous quality control measures, including testing and inspection.