Distributed Control System
Introduction
A Distributed Control System (DCS) is a computerized control system for a process or plant, wherein controller elements are not central in location (like the brain) but are distributed throughout the system with each component sub-system controlled by one or more controllers. The entire system of controllers is connected by networks for communication and monitoring.
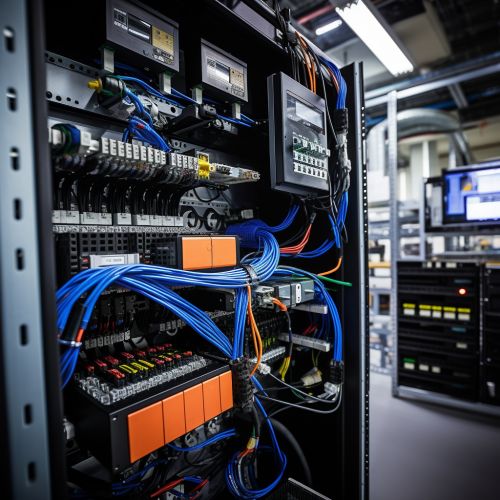
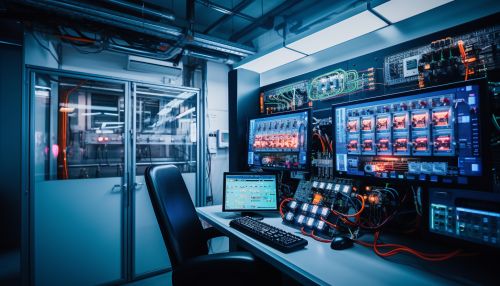
History
The concept of distributed control systems first emerged in the 1970s from the need to improve efficiency and performance of control systems for large industrial processes. The development of DCS was a significant shift from the traditional centralized control systems, which were limited by their inability to handle large amounts of data and their lack of flexibility.
Architecture
The architecture of a DCS is hierarchical. At the top level, there is a human-machine interface (HMI), usually linked to a central control room. This interface allows operators to monitor the system and make adjustments as necessary. Below this, there is a control level, which is responsible for executing the control algorithms and communicating with the field devices. The field level includes the actual process equipment, such as sensors and actuators.
Components
A DCS typically comprises three main components:
- Controllers: These are the brains of the system. They execute the control algorithms, process the data from the field devices, and send commands back to the field.
- I/O Modules: These are the eyes and ears of the system. They interface with the field devices, converting the electrical signals from the devices into digital data that the controllers can understand.
- Communication Networks: These are the nerves of the system. They connect all the components of the DCS, allowing them to communicate with each other.
Functionality
The primary function of a DCS is to control complex, large, and geographically distributed applications in industrial processes. In a DCS, all the controller elements can communicate with each other and the operator workstations, allowing the operator to control the entire process from a central location. The DCS also provides advanced functionality such as redundancy, fault tolerance, and sophisticated alarm handling.
Applications
DCSs are used in a wide variety of industries, including:
- Chemical Plants: DCSs are used to control complex processes, such as chemical reactions, where precise control is required.
- Oil and Gas Industry: DCSs are used to control and monitor drilling operations, pipeline transport, and refinery processes.
- Power Generation: DCSs are used to control and monitor power generation processes, such as coal-fired power plants and nuclear power plants.
- Water and Wastewater Treatment: DCSs are used to control and monitor water treatment processes, ensuring the safe and efficient treatment of water and wastewater.
Advantages and Disadvantages
Advantages of DCS include:
- Improved Process Quality: DCSs provide precise control over industrial processes, resulting in improved product quality.
- Increased Efficiency: DCSs can automate complex processes, reducing the need for manual intervention and increasing efficiency.
- Enhanced Safety: DCSs can monitor and control safety-critical processes, reducing the risk of accidents.
Disadvantages of DCS include:
- High Initial Cost: The initial cost of a DCS can be high, particularly for large and complex systems.
- Complexity: DCSs are complex systems that require specialized knowledge to design, implement, and maintain.
- Dependence on Vendor: Many DCSs are proprietary systems, meaning that users are dependent on the vendor for support and upgrades.
Future Trends
The future of DCS lies in the integration of traditional DCS functionality with new technologies such as the Internet of Things (IoT), cloud computing, and artificial intelligence. This integration will enable more efficient and flexible control systems, capable of adapting to changing process conditions in real time.