Direct Reduced Iron
Introduction
Direct Reduced Iron (DRI), also known as sponge iron, is a type of iron produced by reducing iron ore in its solid state, as opposed to the conventional blast furnace method of ironmaking, which involves melting the ore. This process is a critical component in the steelmaking industry, providing an alternative to the traditional methods and offering several advantages, including lower energy consumption and reduced carbon emissions. The production of DRI involves the use of reducing gases, primarily composed of hydrogen and carbon monoxide, to remove oxygen from iron ore, resulting in a product that is highly pure and suitable for steelmaking.
Production Process
Raw Materials
The primary raw material for the production of DRI is iron ore, which can be in the form of lumps, pellets, or fines. The quality of the iron ore is crucial, as it determines the efficiency and quality of the DRI produced. High-grade iron ore with low impurities is preferred to minimize the need for additional processing and to ensure the production of high-quality DRI. Additionally, the reducing gases used in the process are typically derived from natural gas or coal, depending on the availability and economic considerations.
Reduction Process
The reduction process of iron ore to produce DRI is carried out in a reactor, where the iron ore is exposed to reducing gases at temperatures ranging from 800 to 1050 degrees Celsius. This process can be conducted in various types of reactors, including shaft furnaces, rotary kilns, and fluidized beds. The choice of reactor depends on factors such as the type of iron ore used, the desired production capacity, and the availability of resources.
In the shaft furnace process, which is the most common method, iron ore pellets are charged from the top of the furnace, and reducing gases are introduced from the bottom. As the gases rise through the furnace, they react with the iron ore, removing oxygen and leaving behind metallic iron. The reduced iron is then discharged from the bottom of the furnace as DRI.
Advantages of DRI
The production of DRI offers several advantages over traditional blast furnace methods. One of the primary benefits is the lower energy consumption, as the process does not require the high temperatures needed to melt iron ore. Additionally, DRI production results in lower carbon emissions, making it a more environmentally friendly option. The use of natural gas as a reducing agent further reduces the carbon footprint of the process.
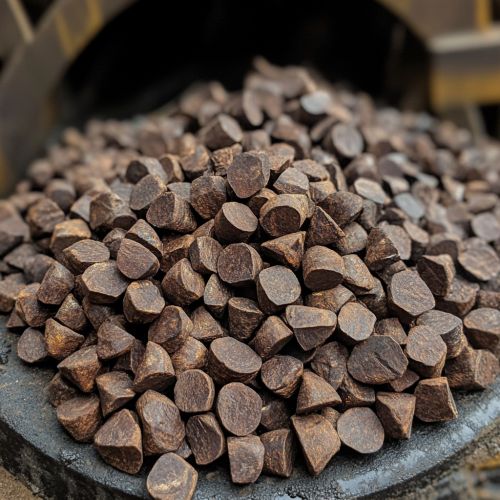
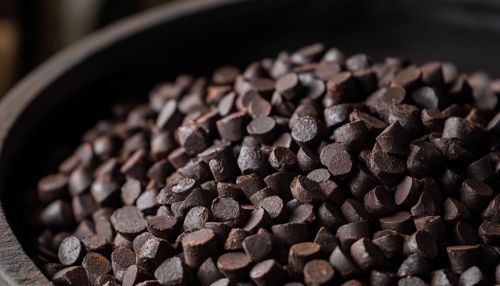
Applications in Steelmaking
DRI is primarily used as a feedstock in electric arc furnaces (EAF) for steelmaking. The high purity of DRI, with low levels of impurities such as sulfur and phosphorus, makes it an ideal raw material for producing high-quality steel. In EAF steelmaking, DRI can be used as a substitute for scrap metal, providing a consistent and reliable source of iron.
The use of DRI in steelmaking also offers flexibility in terms of raw material sourcing, as it allows steel producers to reduce their reliance on scrap metal, which can be subject to price fluctuations and quality variations. Additionally, the use of DRI can improve the overall efficiency of the steelmaking process, as it provides a more uniform and predictable input.
Environmental Impact
The production of DRI has a significantly lower environmental impact compared to traditional ironmaking methods. The use of natural gas as a reducing agent results in lower carbon dioxide emissions, contributing to efforts to reduce greenhouse gas emissions in the steel industry. Furthermore, the solid-state reduction process eliminates the need for coke, a carbon-intensive material used in blast furnaces, further reducing the environmental footprint of DRI production.
Additionally, DRI production generates less waste and by-products compared to blast furnace operations, minimizing the need for waste management and disposal. The process also allows for the recycling of waste gases, which can be used to generate energy or as a feedstock for other industrial processes.
Technological Developments
Recent advancements in DRI technology have focused on improving the efficiency and sustainability of the process. Innovations such as the use of hydrogen as a reducing agent have the potential to further reduce carbon emissions, as hydrogen produces only water as a by-product. This development aligns with global efforts to transition to a low-carbon economy and reduce the environmental impact of industrial processes.
Other technological improvements include the optimization of reactor designs and the development of more efficient gas reforming technologies, which enhance the overall efficiency of DRI production. These advancements contribute to the economic viability of DRI as a competitive alternative to traditional ironmaking methods.
Economic Considerations
The economic viability of DRI production is influenced by several factors, including the cost of raw materials, energy prices, and market demand for steel. The availability and price of natural gas, in particular, play a critical role in determining the competitiveness of DRI compared to other ironmaking methods. In regions with abundant and affordable natural gas resources, DRI production can be a cost-effective option for steel producers.
Market demand for high-quality steel also impacts the economic feasibility of DRI production. As industries such as automotive and construction increasingly require steel with specific properties, the demand for DRI as a reliable and consistent feedstock is expected to grow.
Challenges and Limitations
Despite its advantages, DRI production faces several challenges and limitations. The reliance on natural gas as a reducing agent can be a constraint in regions where natural gas is scarce or expensive. Additionally, the initial capital investment required for setting up DRI production facilities can be significant, posing a barrier to entry for some steel producers.
The quality of the iron ore used in DRI production is another critical factor, as impurities can affect the efficiency of the reduction process and the quality of the final product. Ensuring a consistent supply of high-grade iron ore is essential for maintaining the competitiveness of DRI production.
Future Prospects
The future of DRI production is closely linked to developments in energy and environmental policies. As the steel industry continues to seek ways to reduce its carbon footprint, DRI is likely to play an increasingly important role in sustainable steelmaking. The potential use of renewable energy sources and green hydrogen in DRI production offers promising opportunities for further reducing the environmental impact of the process.
Ongoing research and development efforts are expected to lead to further improvements in DRI technology, enhancing its efficiency and economic viability. As these advancements continue to unfold, DRI is poised to become a key component of the global steel industry, contributing to a more sustainable and resilient supply chain.