Copper extraction
Introduction
Copper extraction refers to the methods used to obtain copper from its ores. The conversion of copper consists of a series of physical and electrochemical processes. Methods have evolved and vary with country depending on the ore source, local environmental regulations, and other factors.
Ore Processing
Copper ores contain only 0.5-6% copper, though most of the ores mined contain less than 1%. Copper ore is mined and crushed to produce a copper concentrate, which is then smelted and refined to produce pure copper.
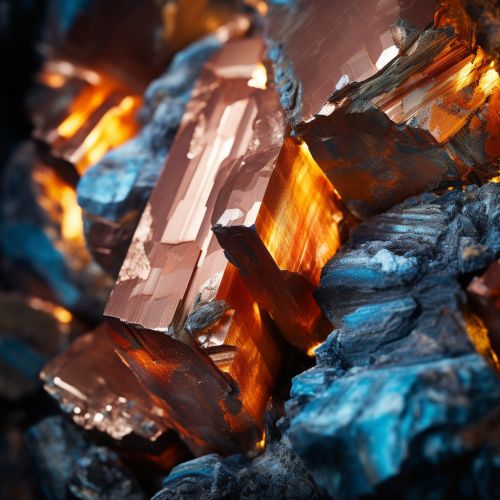
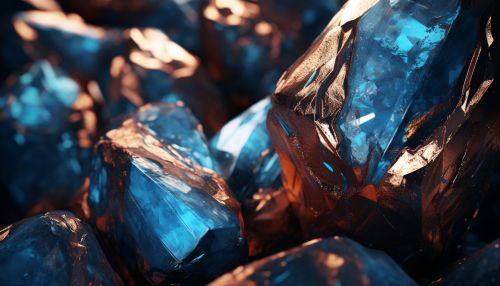
Concentration
The concentration of copper in ores averages only 0.6%, and most commercial ores are sulfides, especially chalcopyrite (CuFeS2) and to a lesser extent chalcocite (Cu2S). The concentration of these minerals in an ore body is low. Typical copper ores contain from 0.5% Cu to 1 or 2% Cu.
Smelting
The process of smelting involves the use of heat and a reducing agent like coal to remove the oxygen from the ore, leaving behind the metal. The smelting process for sulfide ores includes a series of steps:
- Roasting
- Smelting
- Converting
- Fire refining
Electrolytic Refining
Electrolytic refining involves the use of an electrolyte and an electric current to separate the pure metal from impurities. In the case of copper, the anode is made of impure copper and the cathode is made of pure copper. The electrolyte is a solution of copper sulfate and sulfuric acid. When the electric current is passed through the solution, copper ions move from the anode to the cathode, where they are deposited as pure copper.
Environmental Impact
The extraction of copper has significant environmental impacts, including the production of waste materials and the release of sulfur dioxide and other air pollutants. The industry is regulated by environmental laws and regulations, and companies are required to take measures to minimize their environmental impact.