Computer Numerical Control
Introduction
Computer Numerical Control (CNC) is a method used in modern machining to perform a wide range of manufacturing tasks. It is a type of programmable automation directed by mathematically precise instructions encoded on a storage medium. CNC systems are used to control a range of complex industrial machinery including lathes, drill presses, and milling machines.
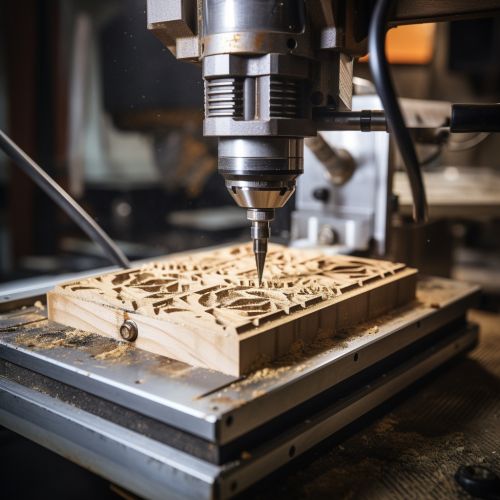
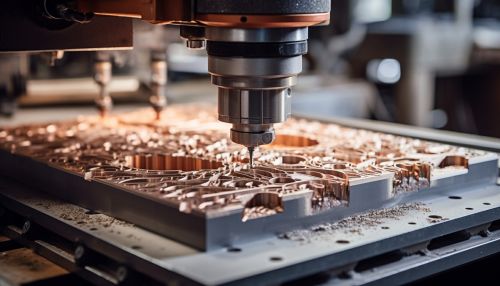
History of CNC
The concept of numerical control (NC) originated when the automation of machine tools first became a research priority during the Second World War. John T. Parsons is credited with pioneering the development of the first numerical control machines in the mid-1940s. Early NC machines were built on existing tools that were modified with motors to control the machine's movements, which were directed by punch-card data input.
The development of computer technology facilitated the evolution of NC into CNC, where a computer replaced the hardwired controller of earlier NC machines. The first CNC machines were introduced to the public in 1960 by the Monarch Machine Tool Company.
Principles of CNC
CNC machines function using a coded programmed instruction and without a manual operator. A CNC machine processes a piece of material (metal, plastic, wood, ceramic, or composite) to meet specifications by following a coded programmed instruction without a manual operator.
A key strength of CNC machining is its ability to run unattended during its entire machining cycle, freeing up an operator to do other tasks. This gives the CNC user several side benefits including reduced operator fatigue, fewer mistakes caused by human error, and consistent and predictable machining time for each piece being machined.
CNC Programming
CNC machines are programmed with a design which can then be manufactured hundreds or even thousands of times. Each manufactured product will be exactly the same. CNC programming is a process that allows machines to be driven to create the product. The language behind CNC machining is alternately referred to as G-code, and it’s written to control the various behaviors of a corresponding machine, such as the speed, feed rate and coordination.
CNC Machine Components
A typical CNC machine has the following components:
1. The part program is a detailed set of commands to be followed by the machine tool. Each command specifies a position in a Cartesian coordinate system. 2. A machine control unit (MCU) is the heart of a CNC system. It is used to perform interpolations (linear, circular, and helical) necessary to produce the contouring motion and provides other important auxiliary functions of the machine. 3. The driving system consists of amplifier circuits, drive motors, and ball lead-screw. The MCU feeds the signals (i.e., of position and speed) of each axis to the amplifier circuits. The control signals are than augmented (increased) to actuate the drive motors. 4. The machine tool includes the actual tool of the machine that will be controlled by the system, such as a milling machine, lathe or drill press.
CNC Machining Process
The CNC machining process begins with the creation of a 2D vector or 3D solid part CAD (computer-aided design) model. The completed design is then exported to a CNC-compatible file format and converted by CAM (computer-aided manufacturing) software into a CNC machine program. The machine then executes the program, cutting away material to create the finished part.
Types of CNC Machines
CNC machines can be divided into several types:
1. CNC Mills: These machines use rotary cutting tools to remove material from a workpiece. The raw material block is secured on the mill bed and the tool moves in three or more axes to machine the desired parts. 2. CNC Lathes: In these machines, the workpiece rotates against a stationary cutting tool and material is removed using axial and radial actions. This is suitable for producing cylindrical or conical parts. 3. CNC Routers: These are used for cutting softer materials like wood, plastic and foam. They are widely used in the furniture and sign-making industries. 4. CNC Plasma Cutters: These machines use a plasma torch to cut materials like steel, metal, and aluminum at high speeds. 5. CNC Electric Discharge Machines (EDM): These machines remove material from a workpiece by creating sparks that burn small holes in the material.
Applications of CNC
CNC machines are used in many industrial applications, including machining, fabricating, and manufacturing. They are also used in a variety of other industries, including woodworking, metalworking, electrical, and electronics. In addition, CNC machines are used in the production of many everyday items such as car parts, surgical tools, airplane engines, and more.
Advantages and Disadvantages of CNC
CNC machines offer numerous benefits over traditional milling equipment. If you are transitioning to CNC milling, you might benefit from the following advantages:
1. Automation: CNC machines can be left unattended during their operation, allowing operators to focus on additional tasks. 2. Precision: CNC machines offer high precision in product manufacturing. 3. Repeatability: Once a design has been fed into the computer, the machine can manufacture hundreds, or even thousands, of products that are exactly the same.
However, there are also some disadvantages of CNC machines:
1. Cost: CNC machines are more expensive and require a greater initial investment than machines that are manually operated. 2. Training: Due to the complexity of CNC machining, operators must have a higher level of skills to operate these machines. They also require training to program the machine to perform the task at hand.