Ceramic Engineering
Introduction
Ceramic engineering is a branch of materials science that focuses on the development and creation of objects from inorganic, non-metallic materials. This field of engineering is unique due to its work with materials that are brittle, heat resistant, and insulating. Ceramic engineers work on a wide range of products that include glassware, electronic components, nuclear materials, and space materials.
History
The history of ceramics dates back to ancient civilizations where pottery and bricks were among the first objects created. The industrial revolution in the 19th century brought about significant advancements in ceramic engineering. The development of porcelain electrical insulators and the discovery of silicon carbide and silicon nitride were some of the major breakthroughs during this period.
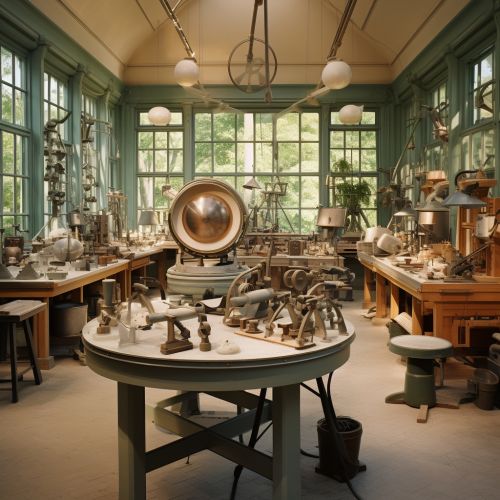
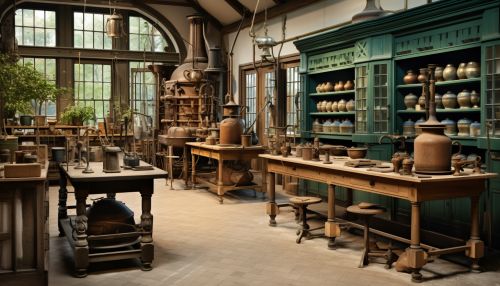
Materials
Ceramic materials are typically hard, porous, and brittle. They are formed by the action of heat and subsequent cooling. Ceramic materials can be divided into two types: traditional ceramics and advanced ceramics.
Traditional Ceramics
Traditional ceramics include clay products such as bricks, tiles, pipes, and pottery. These materials are generally composed of silicate minerals mixed with water.
Advanced Ceramics
Advanced ceramics, also known as technical ceramics, are made from refined powders and can be tailored to have a wide range of properties. These include alumina, zirconia, silicon carbide, and silicon nitride.
Processes
Ceramic engineering involves several key processes. These include:
Raw Material Procurement
The first step in the ceramic engineering process is the procurement of raw materials. The raw materials used in ceramic engineering are generally non-metallic, inorganic powders such as clay, talc, silica, and feldspar.
Forming
The raw materials are then formed into the desired shape. This can be achieved through various methods such as pressing, extrusion, slip casting, and tape casting.
Firing
After the ceramic has been formed, it is fired in a kiln at a high temperature. This process, known as sintering, causes the ceramic particles to bond together, resulting in a hard, dense material.
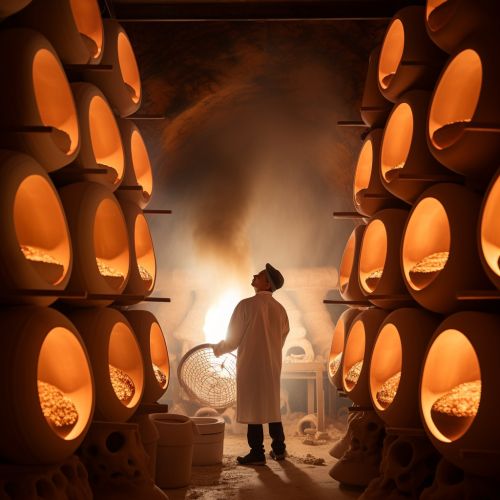
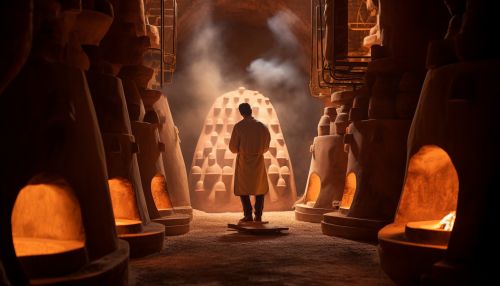
Applications
Ceramic engineering has a wide range of applications. These include:
Electronics
Ceramics are used in the production of electronic components such as capacitors, transistors, and insulators. They are also used in the manufacture of semiconductors.
Energy
In the energy sector, ceramics are used in the production of solar panels and fuel cells. They are also used in nuclear reactors due to their ability to withstand high temperatures and radiation.
Biomedical
Ceramic materials are used in the biomedical field for applications such as dental implants, bone grafts, and joint replacements.
Aerospace
In the aerospace industry, ceramics are used in the production of heat shields, engine components, and sensors.
Future Trends
The future of ceramic engineering lies in the development of new materials and processes. This includes the use of nanotechnology to create ceramics with improved properties, the development of bioceramics for medical applications, and the creation of energy-efficient ceramics for use in green technologies.