Advances in Electrospinning for Nanofiber Production
Introduction
Electrospinning is a versatile and viable technique for generating ultrafine fibers. This method, which has been around for over a century, has seen significant advancements in recent years, particularly in the realm of nanofiber production. These advancements have opened up new possibilities in various fields, including nanotechnology, biotechnology, and material science.
History of Electrospinning
The roots of electrospinning can be traced back to the early 20th century. The first patent related to electrospinning was filed in 1902 by John Francis Cooley, who described a method for producing threads from liquid droplets by using electric forces. Over the years, the process has been refined and improved, leading to the modern electrospinning techniques used today.
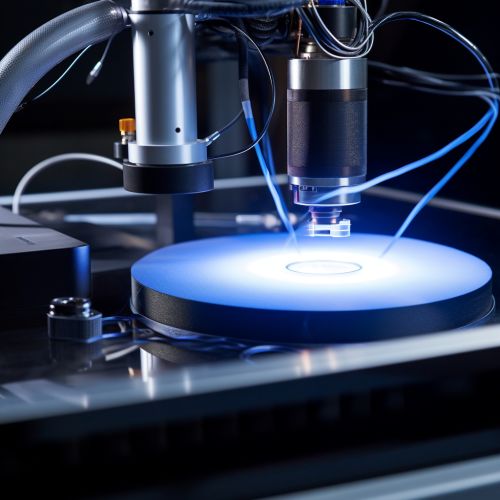
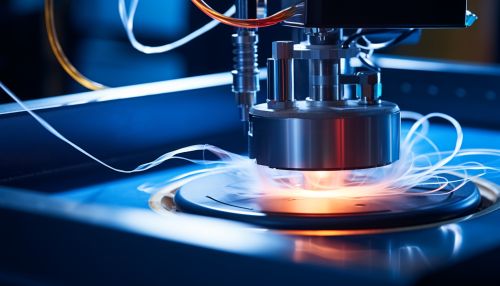
Principles of Electrospinning
The basic principle of electrospinning involves the use of an electric field to draw charged threads of polymer solutions or melts up to fiber diameters in the order of some hundred nanometers. The process begins with a droplet of polymer solution held at the end of a capillary tube, which is subjected to a high voltage to induce a charge on the droplet. The electric field causes the droplet to stretch into a cone shape, known as the Taylor cone. As the intensity of the electric field is increased, the repulsive electrostatic forces overcome the surface tension of the droplet, causing a jet of liquid to be ejected from the tip of the Taylor cone. This jet then undergoes a process of elongation and thinning, facilitated by the evaporation of the solvent, leading to the formation of a thin fiber.
Advancements in Electrospinning Techniques
While the basic principles of electrospinning have remained largely unchanged, there have been significant advancements in the techniques used for electrospinning, particularly in the production of nanofibers. These advancements have primarily focused on improving the control over the fiber formation process, enhancing the quality of the resulting fibers, and expanding the range of materials that can be electrospun.
Control over Fiber Formation
One of the key advancements in electrospinning techniques has been the development of methods for controlling the formation of fibers. This has been achieved through the use of precise control over the electrospinning parameters, such as the voltage applied, the flow rate of the polymer solution, and the distance between the capillary tube and the collector. By carefully controlling these parameters, it is possible to control the diameter of the resulting fibers, the orientation of the fibers, and the porosity of the fiber mat.
Enhancement of Fiber Quality
Another important advancement has been the development of techniques for enhancing the quality of the resulting fibers. This includes methods for reducing defects in the fibers, such as beads or irregularities in the fiber diameter, as well as techniques for improving the uniformity of the fiber mat. These advancements have been facilitated by the use of advanced imaging techniques, such as scanning electron microscopy, which allow for the detailed examination of the fiber structure and the identification of defects.
Expansion of Electrospinnable Materials
Perhaps the most significant advancement in electrospinning has been the expansion of the range of materials that can be electrospun. While early electrospinning efforts were primarily focused on polymers, recent advancements have made it possible to electrospin a wide range of materials, including ceramics, metals, and composite materials. This has opened up new possibilities for the use of electrospun fibers in a wide range of applications, from nanocomposites and biomaterials to energy storage and environmental remediation.
Applications of Electrospun Nanofibers
The advancements in electrospinning techniques have led to a significant expansion in the potential applications of electrospun nanofibers. These applications span a wide range of fields, reflecting the versatility of the electrospinning process and the unique properties of the resulting fibers.
Nanotechnology
In the field of nanotechnology, electrospun nanofibers are used in a variety of applications, from the fabrication of nanostructured materials and nanodevices to the development of nanosensors and nanocatalysts. The ability to control the size, shape, and composition of the fibers at the nanoscale level allows for the design of materials and devices with tailored properties, opening up new possibilities in nanotechnology.
Biotechnology
In biotechnology, electrospun nanofibers are used in a variety of applications, including tissue engineering, drug delivery, and biosensors. The high surface area-to-volume ratio and the ability to control the fiber structure at the nanoscale level make electrospun fibers ideal for these applications. For example, in tissue engineering, electrospun fiber mats can serve as scaffolds that mimic the extracellular matrix, promoting cell adhesion and proliferation.
Material Science
In material science, electrospun nanofibers are used in a variety of applications, including the fabrication of composite materials, membranes, and coatings. The ability to incorporate different materials into the fibers, either as blends or as core-shell structures, allows for the design of materials with tailored properties, such as enhanced mechanical strength, improved chemical resistance, or specific optical properties.
Future Perspectives
The advancements in electrospinning techniques for nanofiber production have opened up new possibilities in various fields. However, there are still challenges to be addressed, such as the need for scalable production methods, the development of techniques for the controlled assembly of fibers into complex structures, and the exploration of new materials for electrospinning. As research in this area continues, it is expected that further advancements will be made, expanding the potential applications of electrospun nanofibers and contributing to the advancement of nanotechnology, biotechnology, and material science.