Flow Coating: Difference between revisions
(Created page with "== Introduction == Flow coating is a sophisticated surface finishing technique used extensively in various industries to apply a uniform coating to substrates. This method involves the controlled application of a liquid coating material over a surface, allowing gravity and surface tension to create a smooth, even layer. Flow coating is particularly valued for its ability to produce high-quality finishes with minimal waste and is commonly used in automotive, aerospace, el...") |
No edit summary |
||
Line 38: | Line 38: | ||
In furniture manufacturing, flow coating is used to apply finishes to wooden and metal furniture pieces. The method provides a smooth, even finish that enhances the appearance and durability of the furniture. | In furniture manufacturing, flow coating is used to apply finishes to wooden and metal furniture pieces. The method provides a smooth, even finish that enhances the appearance and durability of the furniture. | ||
[[Image:Detail-97771.jpg|thumb|center|Technician applying flow coating to an automotive part in a controlled environment.|class=only_on_mobile]] | |||
[[Image:Detail-97772.jpg|thumb|center|Technician applying flow coating to an automotive part in a controlled environment.|class=only_on_desktop]] | |||
== Equipment and Materials == | == Equipment and Materials == |
Latest revision as of 12:56, 30 August 2024
Introduction
Flow coating is a sophisticated surface finishing technique used extensively in various industries to apply a uniform coating to substrates. This method involves the controlled application of a liquid coating material over a surface, allowing gravity and surface tension to create a smooth, even layer. Flow coating is particularly valued for its ability to produce high-quality finishes with minimal waste and is commonly used in automotive, aerospace, electronics, and furniture manufacturing.
Process Overview
Flow coating involves several critical steps to ensure the desired finish quality. The process can be broken down into the following stages:
Surface Preparation
Proper surface preparation is essential for achieving a high-quality finish. The substrate must be cleaned thoroughly to remove any contaminants such as dust, grease, or oils. This can be achieved through various cleaning methods, including solvent wiping, abrasive blasting, or ultrasonic cleaning. Surface preparation may also involve the application of a primer to enhance adhesion and improve the durability of the final coating.
Coating Application
The coating material, typically a liquid such as paint, varnish, or resin, is applied to the substrate using a controlled flow. The substrate is positioned at an angle, and the coating material is poured or sprayed onto the surface. The coating flows over the substrate, covering it uniformly. The excess coating material is collected and recirculated, minimizing waste.
Curing and Drying
After the coating is applied, it must be cured or dried to achieve the desired properties. The curing process can involve air drying, oven baking, or exposure to ultraviolet (UV) light, depending on the type of coating material used. Proper curing is crucial for achieving the final hardness, adhesion, and resistance properties of the coating.
Advantages of Flow Coating
Flow coating offers several advantages over other coating methods, making it a preferred choice in many applications:
- **Uniform Coating Thickness**: The flow coating process ensures a consistent and uniform coating thickness, which is essential for achieving high-quality finishes.
- **High Transfer Efficiency**: Flow coating minimizes material waste by recirculating excess coating material, resulting in high transfer efficiency.
- **Reduced Overspray**: Unlike spray coating, flow coating generates minimal overspray, reducing the need for extensive masking and cleanup.
- **Versatility**: Flow coating can be used with a wide range of coating materials, including paints, varnishes, and resins, making it suitable for various applications.
- **Cost-Effective**: The efficient use of coating materials and reduced labor costs make flow coating a cost-effective finishing method.
Applications
Flow coating is used in numerous industries due to its versatility and ability to produce high-quality finishes. Some of the key applications include:
Automotive Industry
In the automotive industry, flow coating is used to apply protective and decorative coatings to various components, including body panels, wheels, and interior trim. The method ensures a smooth, durable finish that enhances the appearance and longevity of the vehicle.
Aerospace Industry
Aerospace manufacturers use flow coating to apply coatings to aircraft components, such as wings, fuselages, and engine parts. The coatings provide corrosion resistance, reduce drag, and improve the overall performance of the aircraft.
Electronics Industry
Flow coating is employed in the electronics industry to apply conformal coatings to printed circuit boards (PCBs) and other electronic components. These coatings protect the components from moisture, dust, and other environmental factors, ensuring their reliability and longevity.
Furniture Manufacturing
In furniture manufacturing, flow coating is used to apply finishes to wooden and metal furniture pieces. The method provides a smooth, even finish that enhances the appearance and durability of the furniture.
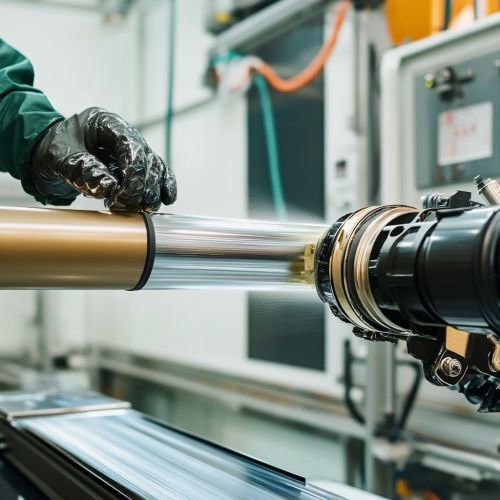
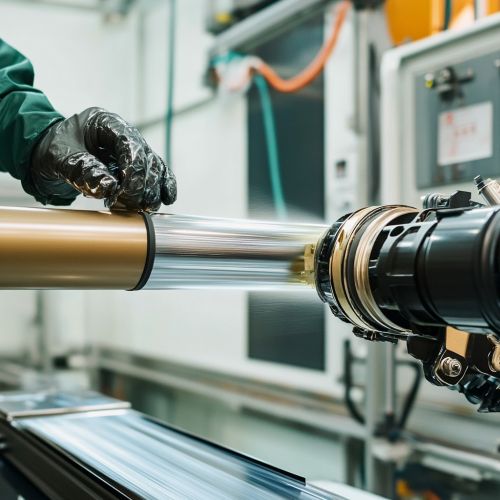
Equipment and Materials
The effectiveness of the flow coating process depends on the quality of the equipment and materials used. Key components include:
Coating Materials
The choice of coating material is critical for achieving the desired finish. Common materials used in flow coating include:
- **Paints**: Solvent-based and water-based paints are widely used for their excellent adhesion and durability.
- **Varnishes**: Varnishes provide a clear, protective finish that enhances the natural beauty of wood and other substrates.
- **Resins**: Epoxy and polyurethane resins offer superior chemical resistance and mechanical properties, making them ideal for demanding applications.
Flow Coating Equipment
Specialized equipment is used to control the flow and application of the coating material. Key components include:
- **Flow Coating Booths**: Enclosed booths provide a controlled environment for the flow coating process, minimizing contamination and ensuring consistent results.
- **Pumps and Dispensers**: Precision pumps and dispensers control the flow rate and volume of the coating material, ensuring uniform application.
- **Recirculation Systems**: Recirculation systems collect and reuse excess coating material, reducing waste and improving transfer efficiency.
Quality Control and Testing
Ensuring the quality of the flow-coated finish requires rigorous quality control and testing procedures. Key aspects include:
Visual Inspection
Visual inspection is the first step in quality control, allowing operators to identify any defects such as runs, sags, or uneven coverage. Inspections are typically conducted under controlled lighting conditions to ensure accurate assessment.
Thickness Measurement
Measuring the coating thickness is crucial for ensuring uniformity and adherence to specifications. Various methods, such as magnetic induction, eddy current, and ultrasonic thickness gauges, are used to measure the coating thickness accurately.
Adhesion Testing
Adhesion testing evaluates the bond strength between the coating and the substrate. Common methods include the cross-cut test, pull-off test, and tape test. These tests help ensure that the coating will not peel or delaminate during service.
Environmental Testing
Environmental testing assesses the performance of the coating under various conditions, such as humidity, temperature, and exposure to chemicals. Tests such as salt spray, humidity chamber, and UV exposure are conducted to evaluate the coating's resistance to corrosion, degradation, and other environmental factors.
Challenges and Considerations
While flow coating offers numerous advantages, it also presents certain challenges and considerations that must be addressed to achieve optimal results:
Substrate Compatibility
Not all substrates are suitable for flow coating. The surface energy, porosity, and chemical composition of the substrate can affect the adhesion and performance of the coating. Proper surface preparation and the use of compatible primers are essential for ensuring good adhesion.
Coating Material Properties
The viscosity, surface tension, and drying characteristics of the coating material can influence the flow coating process. Selecting the appropriate coating material and adjusting its properties through additives and formulation changes are critical for achieving the desired finish.
Process Control
Maintaining consistent process parameters, such as flow rate, temperature, and humidity, is essential for achieving uniform coatings. Automated systems and real-time monitoring can help ensure precise control of the flow coating process.
Environmental and Safety Considerations
Flow coating operations must comply with environmental regulations and safety standards. Proper ventilation, waste management, and the use of personal protective equipment (PPE) are essential for protecting workers and minimizing environmental impact.
Innovations and Future Trends
The flow coating industry continues to evolve, with ongoing innovations and advancements aimed at improving efficiency, quality, and sustainability. Some of the key trends include:
Advanced Coating Materials
The development of new coating materials with enhanced properties, such as self-healing, anti-microbial, and superhydrophobic coatings, is expanding the range of applications for flow coating. These advanced materials offer improved performance and durability, meeting the demands of various industries.
Automation and Robotics
The integration of automation and robotics in flow coating operations is increasing efficiency and consistency. Automated systems can precisely control the flow rate, application angle, and curing conditions, reducing human error and improving repeatability.
Sustainable Practices
Sustainability is a growing focus in the flow coating industry. Efforts to reduce waste, energy consumption, and the use of hazardous materials are driving the adoption of eco-friendly coating materials and processes. Innovations such as water-based coatings, low-VOC formulations, and closed-loop recirculation systems are contributing to more sustainable flow coating practices.