Artificial Muscles: Difference between revisions
(Created page with "== Introduction == Artificial muscles are a class of materials or devices that mimic the function of natural muscle tissue by contracting, expanding, or rotating in response to an external stimulus. These stimuli can include electrical voltage, chemical reactions, temperature changes, or magnetic fields. Artificial muscles have garnered significant attention due to their potential applications in robotics, biomedical engineering, and wearable technology. Unl...") |
No edit summary |
||
Line 11: | Line 11: | ||
Electroactive polymers are materials that change shape or size when stimulated by an electric field. They are divided into two main categories: ionic EAPs and electronic EAPs. Ionic EAPs, such as ionic polymer-metal composites (IPMCs), operate through ion migration and require a wet environment. Electronic EAPs, like dielectric elastomers, rely on electrostatic forces and can function in dry conditions. | Electroactive polymers are materials that change shape or size when stimulated by an electric field. They are divided into two main categories: ionic EAPs and electronic EAPs. Ionic EAPs, such as ionic polymer-metal composites (IPMCs), operate through ion migration and require a wet environment. Electronic EAPs, like dielectric elastomers, rely on electrostatic forces and can function in dry conditions. | ||
[[Image:Detail-98465.jpg|thumb|center|Close-up of a flexible polymer strip bending under electrical stimulation.|class=only_on_mobile]] | |||
[[Image:Detail-98466.jpg|thumb|center|Close-up of a flexible polymer strip bending under electrical stimulation.|class=only_on_desktop]] | |||
=== Shape Memory Alloys (SMAs) === | === Shape Memory Alloys (SMAs) === |
Latest revision as of 19:25, 13 October 2024
Introduction
Artificial muscles are a class of materials or devices that mimic the function of natural muscle tissue by contracting, expanding, or rotating in response to an external stimulus. These stimuli can include electrical voltage, chemical reactions, temperature changes, or magnetic fields. Artificial muscles have garnered significant attention due to their potential applications in robotics, biomedical engineering, and wearable technology. Unlike traditional actuators, artificial muscles offer advantages such as lightweight, flexibility, and the ability to produce complex movements.
Types of Artificial Muscles
Artificial muscles can be categorized based on the type of stimulus they respond to. The primary types include:
Electroactive Polymers (EAPs)
Electroactive polymers are materials that change shape or size when stimulated by an electric field. They are divided into two main categories: ionic EAPs and electronic EAPs. Ionic EAPs, such as ionic polymer-metal composites (IPMCs), operate through ion migration and require a wet environment. Electronic EAPs, like dielectric elastomers, rely on electrostatic forces and can function in dry conditions.
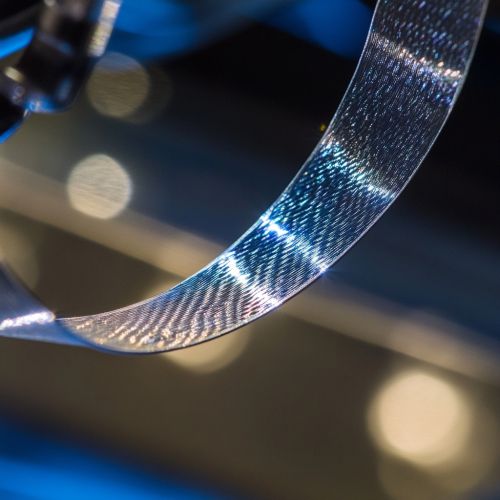

Shape Memory Alloys (SMAs)
Shape memory alloys are metals that can return to a pre-defined shape when heated. The most common SMA is Nitinol, an alloy of nickel and titanium. SMAs are known for their high energy density and are used in applications requiring significant force generation, such as in medical devices and aerospace components.
Conducting Polymers
Conducting polymers, such as polypyrrole and polyaniline, change their volume in response to electrical stimulation. These materials are advantageous for their low operating voltage and ability to produce significant strain. They are often used in micro-actuators and sensors.
Carbon Nanotube Actuators
Carbon nanotube actuators leverage the unique mechanical and electrical properties of carbon nanotubes. When a voltage is applied, the nanotubes expand or contract due to electrostatic forces. These actuators are known for their high strength-to-weight ratio and rapid response times.
Liquid Crystal Elastomers (LCEs)
Liquid crystal elastomers combine the properties of liquid crystals and elastomers, allowing them to undergo large deformations in response to temperature changes or light exposure. LCEs are being explored for applications in soft robotics and adaptive optics.
Mechanisms of Action
The mechanisms by which artificial muscles operate vary depending on the material and stimulus involved. Understanding these mechanisms is crucial for optimizing performance and expanding their applications.
Ionic Movement
In ionic EAPs, the movement of ions within the polymer matrix causes the material to bend or expand. This process is typically slow but can produce large deformations. The efficiency of ionic movement is influenced by factors such as ion size, concentration, and the polymer's ionic conductivity.
Electrostatic Forces
Electronic EAPs and carbon nanotube actuators primarily rely on electrostatic forces. When an electric field is applied, charges accumulate on the surface of the material, causing it to deform. The strength of the electrostatic forces depends on the dielectric constant of the material and the applied voltage.
Thermal Activation
SMAs and LCEs utilize thermal activation to induce shape changes. In SMAs, heating causes a phase transformation from martensite to austenite, resulting in a shape change. LCEs undergo a transition from an ordered to a disordered state, leading to expansion or contraction.
Chemical Reactions
Conducting polymers often rely on redox reactions to induce volume changes. The insertion or removal of ions during these reactions causes the polymer to swell or shrink. The speed and magnitude of these changes are influenced by the polymer's chemical structure and the type of ions involved.
Applications
Artificial muscles have a wide range of applications across various fields, each leveraging their unique properties to solve specific challenges.
Robotics
In robotics, artificial muscles are used to create soft, flexible actuators that can mimic the complex movements of natural organisms. This is particularly useful in soft robotics, where traditional rigid actuators are unsuitable. Artificial muscles enable robots to perform delicate tasks, such as handling fragile objects or navigating uneven terrain.
Biomedical Engineering
Artificial muscles are being developed for use in prosthetics and orthotics, providing more natural movement and improved comfort for users. They are also explored for use in artificial organs, such as artificial hearts and muscles for facial reconstruction.
Wearable Technology
In wearable technology, artificial muscles can be used to create adaptive clothing and exoskeletons that enhance human performance. These devices can provide additional strength, support, or protection, making them valuable in fields such as healthcare, military, and sports.
Aerospace
In the aerospace industry, artificial muscles are used in morphing structures that can change shape to optimize performance. This includes adaptive wings and control surfaces that improve fuel efficiency and maneuverability.
Challenges and Future Directions
Despite their potential, artificial muscles face several challenges that must be addressed to realize their full capabilities.
Material Limitations
Many artificial muscle materials suffer from limitations such as low durability, slow response times, and limited force output. Research is ongoing to develop new materials and improve existing ones to overcome these issues.
Energy Efficiency
The energy efficiency of artificial muscles is a critical factor in their practical application. Many current systems require high power inputs, limiting their use in portable or battery-operated devices. Advances in material science and engineering are needed to develop more energy-efficient solutions.
Scalability
Scaling artificial muscle technologies for mass production is another significant challenge. This involves developing cost-effective manufacturing processes and ensuring consistent quality and performance across large batches.
Integration with Existing Systems
Integrating artificial muscles with existing mechanical and electronic systems requires careful consideration of factors such as control algorithms, power supply, and mechanical interfaces. This integration is essential for the successful deployment of artificial muscles in real-world applications.