Good Manufacturing Practice: Difference between revisions
(Created page with "== Good Manufacturing Practice == Good Manufacturing Practice (GMP) refers to the practices required in order to conform to the guidelines recommended by agencies that control the authorization and licensing of the manufacture and sale of food and beverages, cosmetics, pharmaceutical products, dietary supplements, and medical devices. These guidelines provide minimum requirements that a manufacturer must meet to assure that their products are consistently high in qualit...") |
No edit summary |
||
Line 3: | Line 3: | ||
Good Manufacturing Practice (GMP) refers to the practices required in order to conform to the guidelines recommended by agencies that control the authorization and licensing of the manufacture and sale of food and beverages, cosmetics, pharmaceutical products, dietary supplements, and medical devices. These guidelines provide minimum requirements that a manufacturer must meet to assure that their products are consistently high in quality, from batch to batch, for their intended use. GMPs are enforced in many countries by national regulatory agencies. | Good Manufacturing Practice (GMP) refers to the practices required in order to conform to the guidelines recommended by agencies that control the authorization and licensing of the manufacture and sale of food and beverages, cosmetics, pharmaceutical products, dietary supplements, and medical devices. These guidelines provide minimum requirements that a manufacturer must meet to assure that their products are consistently high in quality, from batch to batch, for their intended use. GMPs are enforced in many countries by national regulatory agencies. | ||
[[Image:Detail-97923.jpg|thumb|center|Pharmaceutical manufacturing facility with workers in protective clothing operating machinery.|class=only_on_mobile]] | |||
[[Image:Detail-97924.jpg|thumb|center|Pharmaceutical manufacturing facility with workers in protective clothing operating machinery.|class=only_on_desktop]] | |||
=== History === | === History === |
Latest revision as of 11:52, 11 September 2024
Good Manufacturing Practice
Good Manufacturing Practice (GMP) refers to the practices required in order to conform to the guidelines recommended by agencies that control the authorization and licensing of the manufacture and sale of food and beverages, cosmetics, pharmaceutical products, dietary supplements, and medical devices. These guidelines provide minimum requirements that a manufacturer must meet to assure that their products are consistently high in quality, from batch to batch, for their intended use. GMPs are enforced in many countries by national regulatory agencies.
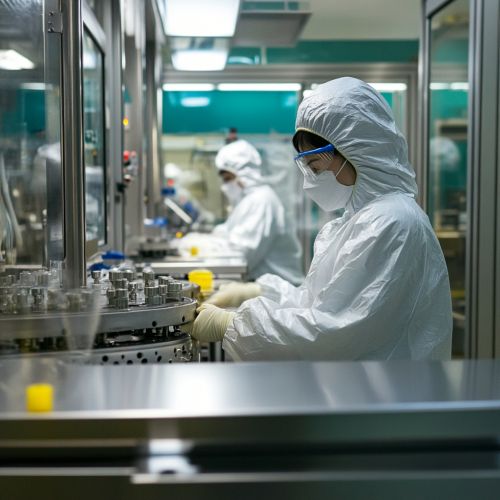
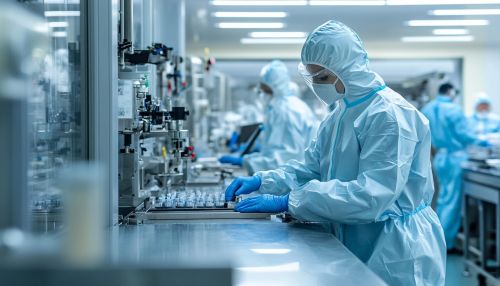
History
The concept of GMP has evolved over time. The first significant step towards modern GMP was the Food, Drug, and Cosmetic Act of 1938 in the United States, which was enacted in response to public health disasters such as the Elixir Sulfanilamide tragedy. The thalidomide disaster in the 1960s further highlighted the need for stringent quality control, leading to the establishment of GMP regulations.
Regulatory Agencies
Several regulatory agencies around the world enforce GMP standards. These include:
- The FDA in the United States
- The EMA in the European Union
- The WHO internationally
- The TGA in Australia
- The PMDA in Japan
Each of these agencies has its own set of GMP guidelines, although they share many common principles.
Key Principles
GMP guidelines are designed to ensure that products are produced and controlled consistently according to quality standards. Key principles include:
Quality Management
Quality management is a comprehensive approach that ensures all aspects of production and distribution are conducted under strict quality control. This includes:
- Quality assurance
- Quality control
- Continuous improvement
Personnel
Personnel involved in manufacturing must be adequately trained and qualified. This includes:
- Ongoing training programs
- Clear job descriptions
- Health and hygiene requirements
Premises and Equipment
The manufacturing environment must be designed to minimize risks. This includes:
- Proper maintenance of buildings and facilities
- Regular calibration and validation of equipment
- Environmental control measures
Documentation
Accurate documentation is crucial for GMP compliance. This includes:
- Standard Operating Procedures (SOPs)
- Batch records
- Logbooks
- Audit trails
Production
Production processes must be clearly defined and controlled. This includes:
- Validation of critical processes
- In-process controls
- Proper handling of raw materials and finished products
Quality Control
Quality control involves the testing of raw materials, in-process materials, and finished products. This includes:
- Sampling procedures
- Analytical testing
- Stability testing
Complaints and Recalls
A system must be in place to handle complaints and recalls. This includes:
- Complaint investigation procedures
- Recall procedures
- Root cause analysis
Implementation
Implementing GMP involves several steps:
- Gap analysis to identify areas of non-compliance
- Development of a quality management system
- Training of personnel
- Regular internal audits
- Continuous improvement initiatives
Challenges
Implementing and maintaining GMP can be challenging. Common challenges include:
- High costs associated with compliance
- Complexity of regulations
- Need for continuous training and education
- Managing supply chain quality
Benefits
Despite the challenges, GMP offers several benefits:
- Ensures product quality and safety
- Enhances customer confidence
- Reduces the risk of product recalls
- Facilitates international trade